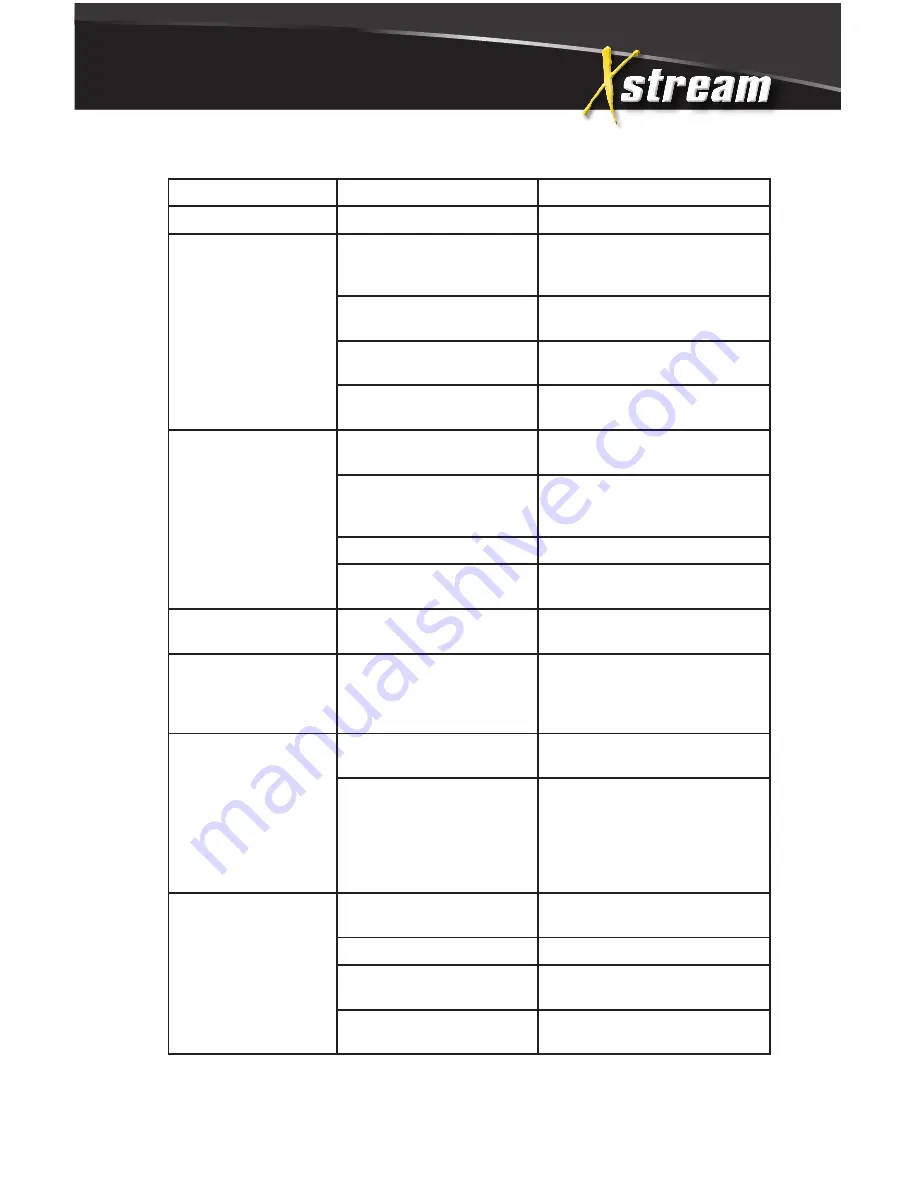
31
troubleshooting
SYMPTOM
PROBABLE CAUSE
REMEDY
Oil leaking from unit.
Worn seals or o-rings.
Contact Customer Service.
Detergent will not
siphon .
Detergent strainer is not
completely submerged in
detergent solution.
Check, submerge if necessary.
Detergent strainer
obstructed.
Inspect, clean or replace.
Detergent hose cut,
obstructed or kinked.
Inspect, clean or replace.
Detergent adjusting knob
turned to closed position.
Open adjusting knob. Refer to
“Cleaning with Detergents”.
Detergent will not
siphon into the Low
Pressure Mode
Adjustable grip on lance is
not in low pressure mode.
Turn grip clockwise to move to
low pressure
Too many high pressure
hose extensions attached to
the water outlet.
Use one extension maximum.
Nozzle assembly is plugged. Clean or replace.
Ball & Spring in Venturi
stuck.
Remove, clean or replace.
Water flows back into
detergent container.
Check valve missing or
corroded.
Remove, clean or replace.
Water flows from the
nozzle when the trigger
gun is locked in the
“OFF” position
Trigger gun is
malfunctioning.
Repair or replace.
Water is leaking under
heat exchanger coil.
Coil drain plug is not
installed.
Install.
Safety Relief device is
relieving caused by an
unloader or pressure switch
malfunction.
1.Detect and correct unloader or
pressure switch problem.
2. Replace safety relief device.
NEVER run unit without safety
relief device. Doing so can cause
an explosion!
Burner will not ignite
Switch is not in “Burner”
position.
Check switch position.
No voltage.
Contact Customer Service.
Out of fuel.
Refuel. (Reset burner primary
control on cad cell options.)
Fuel pickup screen
obstructed.
Consult Service.
Summary of Contents for HW152EMD
Page 1: ...operation manual HW152EMD HW204EMD ELECTRIC HOT WATER PRESSURE WASHER...
Page 36: ...36 flow chart 57 6 013 FLOW CHART parts list...
Page 38: ...38 frame assembly 59 10 Copyright 2013 FRAME ASSEMBLY parts list...
Page 40: ...40 motor pump assembly 61 12 Copyright 2013 MOTOR PUMP ASSEMBLY parts list...
Page 49: ...49 69 20 Copyright 2013 HEAT EXCHANGER BLOWER MOTOR heat exchanger blower motor parts list...
Page 51: ...51 boiler assembly 71 22 pyright 2013 BOILER ASSEMBLY parts list...
Page 62: ...62 wire schematic for hw204emd 83 34 ht 2013 WIRE SCHEMATIC FOR C204EMHW HW204EMD parts list...