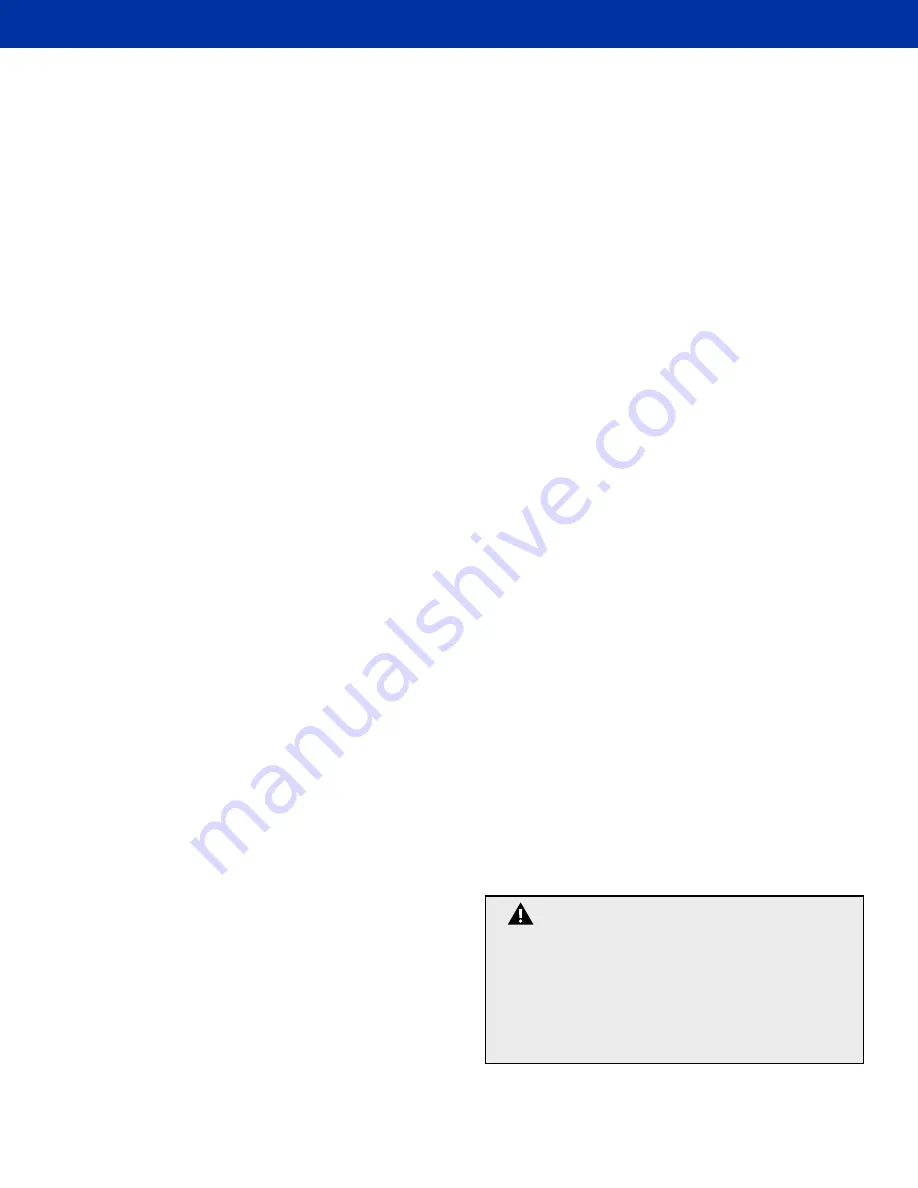
5
www.XSscuba.com
XS Scuba Valves Service Manual
Maintenance Schedules
How often a scuba valve should get serviced is very
subjective. Scuba valves are subjected to a variety of
environmental elements that, over time, can affect their
performance. Salt, sand, sediment, chlorine and other
chemicals all take their toll on a scuba valve. Soft parts
wear out and lubricants break down and wash away.
While it would be easy just to say, “Service your valves
once a year”, it would not be very forthcoming. Using
a calendar to determine servicing intervals is not
appropriate. Servicing depends upon the amount of use,
the environmental conditions and whether prescribed care
was met.
The preferred method is to evaluate the valve annually and
service it when one or more of the following indicators are
present:
• Air leaking from the handwheel / bonnet area
• Air leaking from the valve / cylinder interface
• Air leaking between modular valve and crossbar
• Corrosion on the exterior finish
• The handwheel does not spin true on its axis. It has a
wobble to it.
• The handwheel has to be closed more than “lightly”
snug to stop the air flow.
• The handwheel becomes difficult to rotate
• The handwheel does not operate smoothly and quietly
Since burst plugs weaken over time, soft parts wear and
lubricants wash away, it is required that you service the
valve at least once every 5 years whether it has seen
much use or not. Since most scuba cylinders require
hydrostatic testing every 5 years, it is recommended that
you service the valve while the cylinder is out getting
hydrostatically tested.
Standard Procedures
1. Preview the list of tools and parts required to perform
the prescribed service outlined in this manual. Follow
each step in the sequence provided. Have this manual
open next to you for reference. Do not rely upon
memory.
2. Numbers found in parenthesis reference the KEY
numbers in the exploded diagrams. If you are not sure
what a part is by its description, use this number to
cross reference it in the exploded diagrams.
3. All valve and manifold services should be performed
on a workbench specifically set up and equipped for
this purpose. Adequate lighting and cleanliness along
with easy access to the required tools should be
considered mandatory.
4. Only use factory authorized parts provided by
XS Scuba. Do not attempt to substitute other
manufacturer’s parts regardless of any similarity in
appearance. This is especially true for o-rings!
5. Do not attempt to reuse mandatory replacement
parts regardless of how much use those parts were
subjected to.
6. When reassembling, it is important to follow factory
mandated torque values using a calibrated torque
wrench. To do otherwise could lead to damage or
failure of the product.
7. Unless otherwise instructed, the following is
assumed:
• When instructed to remove, unscrew or loosen
a threaded part, turn the part counterclockwise.
The manual abbreviates counterclockwise with
CCW.
• When instructed to install, screw in or tighten
a threaded part, turn the part clockwise. The
manual abbreviates clockwise with CW.
Nitrox Compatibility
Depending upon the model, when XS Scuba Valves are
sold new, they are designated for either Compressed
Air Only service or for Maximum 40% Oxygen Premixed
service. The service designation is shown in the XS
Scuba catalog, the XS Scuba website and on the valve
itself.
A valve model designated for Compressed Air Only
service is manufactured and prepared for use only with
breathing air (21% oxygen and 79% nitrogen by volume)
that is of quality Grade E or better.
A valve model designated for Maximum 40% Oxygen
Premixed service may be used for either oxygen
enriched breathing air with a maximum oxygen content
of 40% (premixed), or for standard breathing air (21%
oxygen and 79% nitrogen by volume) with a purity rating
as low as Grade E*. If the valve is used for standard
breathing air where the hydrocarbons exceed 0.1 mg/
m3, such as Grade E, then the valve must be dedicated
to breathing air service and MAY NOT be used for
oxygen enriched breathing air until such time as the
valve is disassembled, properly cleaned and lubricated,
and assembled for Maximum 40% Oxygen Premixed
service again.
WARNING: For the valve to remain Maximum
40% Oxygen Premixed compatible, only use
hyper-filtered compressed gas (hydrocarbons <
0.1 mg/m3). Ordinary compressed breathing air
(Grade E) usually does not meet this criterion.
Once ordinary breathing air is used, the valve
is no longer Maximum 40% Oxygen Premixed
compatible until it is cleaned and serviced again.