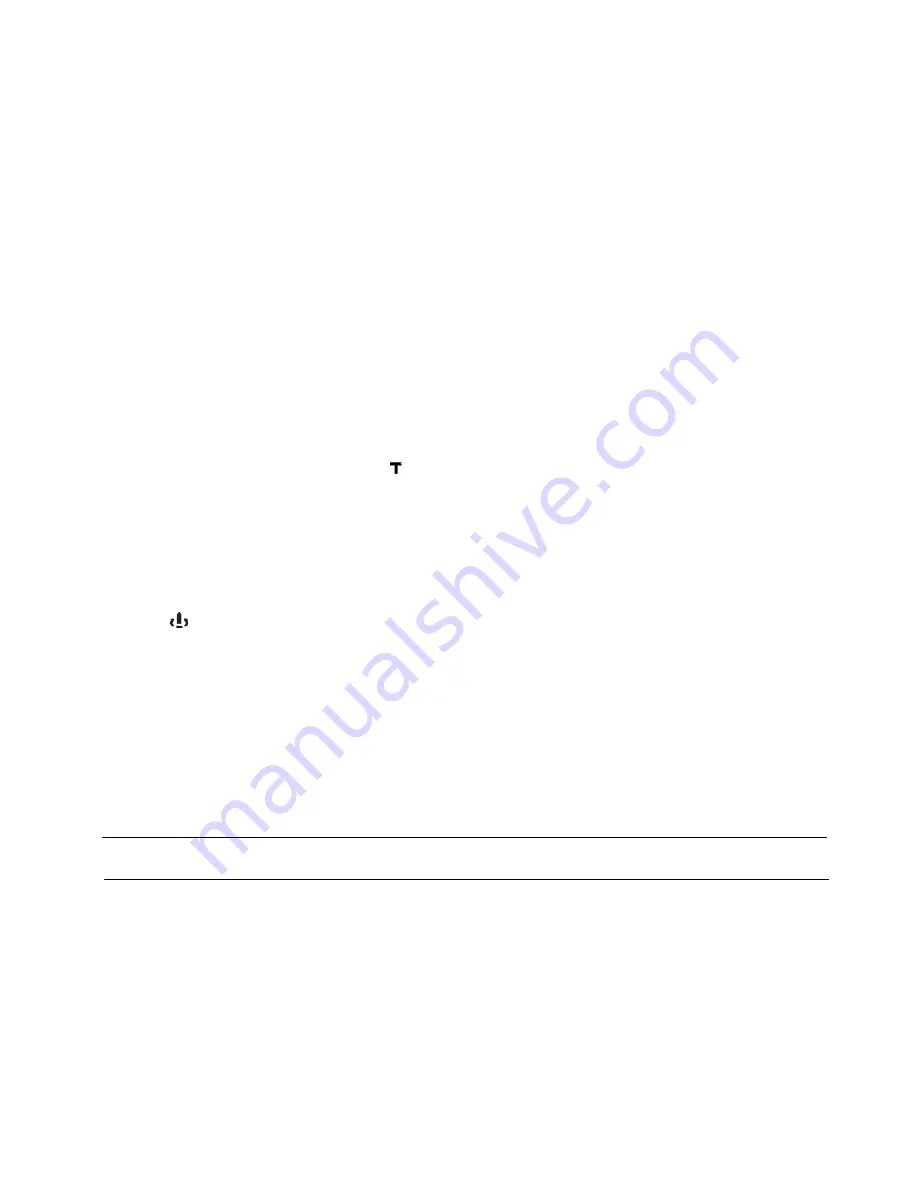
To drill wood or metal material using the drill chuck and drill chuck shank (optional accessories),
proceed as follows.
Installing drill chuck and drill chuck shank
(Fig.7).
(1) Attach the drill chuck to the drill chuck shank.
(2) Insert the drill chuck shank SDS-plus in a twisting manner into the tool holder until it latches itself
CAUTION:
{
Application of force more than necessary will not only expedite the work, but will deteriorate the tip
edge of the drill bit and reduce the service life of the rotary hammer in addition.
{
Drill bits may snap off while withdrawing the rotary hammer from the drilled hole. For withdrawing, it
is important to use a pushing motion.
{
Do not attempt to drill anchor holes or holes in concrete with the machine set in the rotation only
function.
{
Do not attempt to use the rotary hammer in the rotation and hammering function with the drill chuck
and drill chuck shank attached. This would seriously shorten the service life of every component of the
machine.
4.
When chipping and chiseling at “hammering”:
(1) Switching to “hammering”
( a) Push the locked Pushbutton, release lock and turn the function knob.
(b) Align
▲
of the function knob and
of the Gear Case as illustrated in
Fig.8.
(c) Release the locked Pushbutton to lock the function knob.
NOTE:
Turn the function knob (do not push the locked Pushbutton) to check if it is completely locked and
make sure that it does not turn.
(2) Mount the tine chisel or flat chisel.
(3) Push the locked Pushbutton, release lock and turn the function knob. Align
▲
of the function knob
and
of the Gear Case as illustrated in
Fig.9.
The rotation is released, turn adjust the flat chisel to desired position.
(Fig.10)
(4) Switch the selector lever to “hammering” according to the procedures mentioned in the above item
(1) and secure the position of the tool.
5. Using Staff Gauge (Fig.11)
(1) Loosen the auxiliary handle and insert the straight portion of the orientation staff guage into the
handle bolt hole.
(2) Move the orientation staff guage to the specified position and rotate the grip of the auxiliary handle
clockwise to fix the orientation staff guage.
HOW TO HANDLE A CORE BIT
When a core bit is used, large diameter holes and blind holes can be drilled. In this case, use optional
accessories for core bits (such as a dill bit and core bit shank) for more efficient operation.
1. Mounting
CAUTION:
Be sure to turn power OFF and disconnect the plug from the receptacle.
(1)
Mount the core bit to the core bit shank.
(Fig.12)
Lubricate the thread of the core bit shank to facilitate disassembly.
(2) Mount the core bit to the rotary hammer
(Fig.13)
(3) Engage the drill bit with the core bit, and turn the drill bit to the left or the right so that it does
not fall even if it faces downward .
(Fig.14)