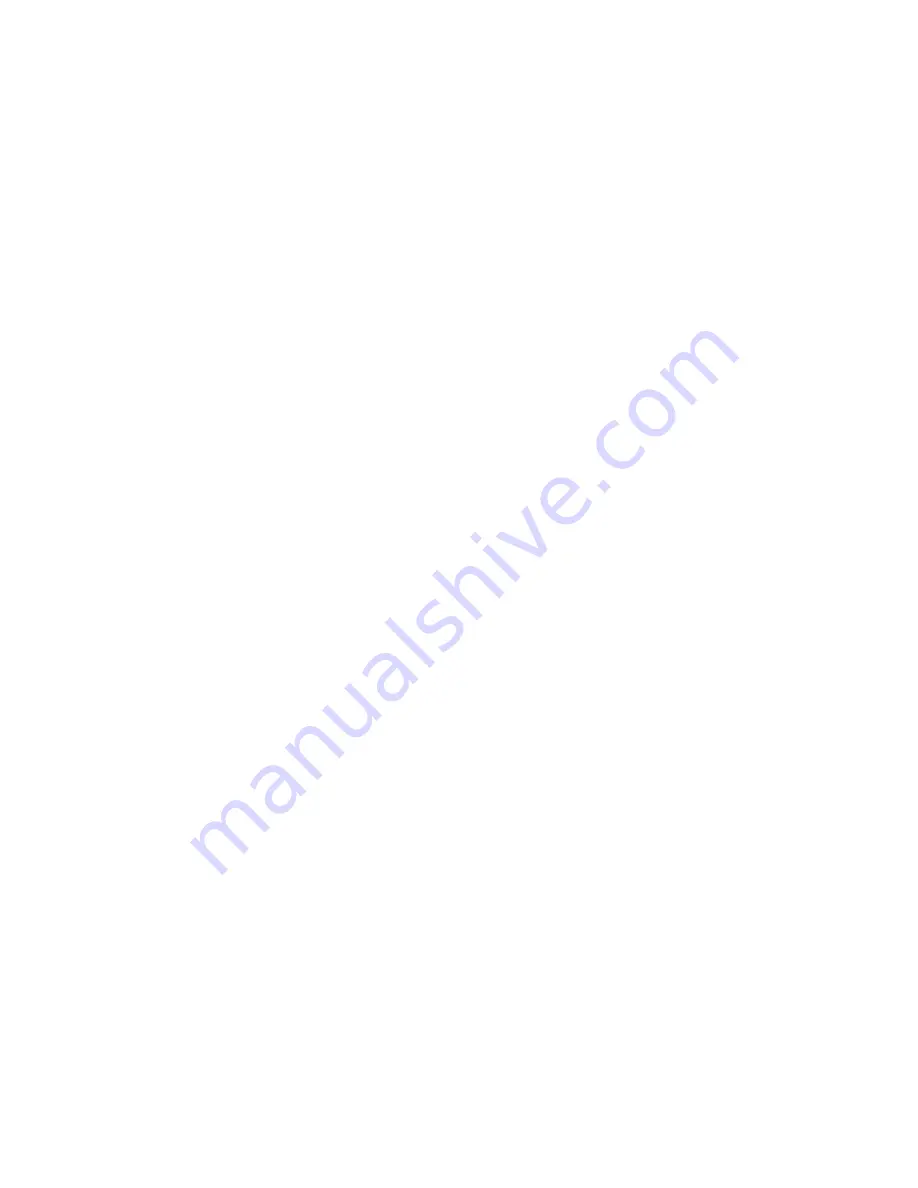
3/99
DocuPrint N24, N32 and N40 Service Manual
8-553
Options
RAP 8.5.7.15 Error Code “Fin Fail H5-83 Power Off/On”
1
Remove the Offset Home Sensor (REP 8.5.3.58). Enter Diagnostic Mode - Input H/L - Finisher
Stacker Sensor/Switch - Offset Home Sr, to test the Offset Home Sensor. Insert and remove a
piece of paper between the Sensor arms. The Control Panel LCD displays L when paper is
inserted between the Sensor arms and H when the paper is removed.
Y
N
|
Replace the Offset Home Sensor (REP 8.5.3.58).
2
Reinstall the Offset Home Sensor (REP 8.5.3.58). Enter Diagnostic Mode - Input H/L - Finisher
Stacker Sensor/Switch - Offset Home Sr. Manually rotate the Eject Clamp Motor drive gear and
observe the LCD. The Control Panel LCD displays H then L as you rotate the drive gear through
360 degrees.
Y
N
|
Replace the Eject Bracket Assembly (REP 8.5.3.59).
3
Enter Diagnostic Mode - Output - Finisher Operations - Eject Cl/Off CW, to check the Eject
Clamp Motor. The Eject Clamp Motor runs.
Y
N
|
Replace the Eject Clamp Offset Motor (REP 8.5.3.82).
4
Replace the Finisher PWB (REP 8.5.3.83). The error code reappears
Y
N
|
Problem solved.
5
Replace the Printer Engine Controller PWB (REP 4.10.6).
Summary of Contents for DocuPrint N24
Page 45: ...3 99 DocuPrint N24 N32 and N40 Service Manual 3 5 Parts Lists ...
Page 47: ...2 2000 DocuPrint N24 N32 N40 N3225 and N4025 3 7 Parts Lists ...
Page 49: ...3 99 DocuPrint N24 N32 and N40 Service Manual 3 9 Parts Lists ...
Page 51: ...3 99 DocuPrint N24 N32 and N40 Service Manual 3 11 Parts Lists ...
Page 53: ...3 99 DocuPrint N24 N32 and N40 Service Manual 3 13 Parts Lists ...
Page 55: ...3 99 DocuPrint N24 N32 and N40 Service Manual 3 15 Parts Lists ...
Page 57: ...3 99 DocuPrint N24 N32 and N40 Service Manual 3 17 Parts Lists ...
Page 59: ...3 99 DocuPrint N24 N32 and N40 Service Manual 3 19 Parts Lists ...
Page 61: ...3 99 DocuPrint N24 N32 and N40 Service Manual 3 21 Parts Lists ...
Page 63: ...3 99 DocuPrint N24 N32 and N40 Service Manual 3 23 Parts Lists ...
Page 65: ...3 99 DocuPrint N24 N32 and N40 Service Manual 3 25 Parts Lists ...
Page 67: ...3 99 DocuPrint N24 N32 and N40 Service Manual 3 27 Parts Lists ...
Page 69: ...2 2000 DocuPrint N24 N32 N40 N3225 and N4025 3 29 Parts Lists ...
Page 71: ...3 99 DocuPrint N24 N32 and N40 Service Manual 3 31 Parts Lists ...
Page 73: ...3 99 DocuPrint N24 N32 and N40 Service Manual 3 33 Parts Lists ...
Page 75: ...3 99 DocuPrint N24 N32 and N40 Service Manual 3 35 Parts Lists ...
Page 77: ...3 99 DocuPrint N24 N32 and N40 Service Manual 3 37 Parts Lists ...
Page 79: ...3 99 DocuPrint N24 N32 and N40 Service Manual 3 39 Parts Lists ...
Page 81: ...3 99 DocuPrint N24 N32 and N40 Service Manual 3 41 Parts Lists ...
Page 83: ...3 99 DocuPrint N24 N32 and N40 Service Manual 3 43 Parts Lists ...
Page 85: ...3 99 DocuPrint N24 N32 and N40 Service Manual 3 45 Parts Lists ...
Page 87: ...3 99 DocuPrint N24 N32 and N40 Service Manual 3 47 Parts Lists ...
Page 89: ...2 2000 DocuPrint N24 N32 N40 N3225 and N4025 3 49 Parts Lists ...
Page 91: ...3 99 DocuPrint N24 N32 and N40 Service Manual 3 51 Parts Lists ...
Page 93: ...2 2000 DocuPrint N24 N32 N40 N3225 and N4025 3 53 Parts Lists ...
Page 95: ...3 99 DocuPrint N24 N32 and N40 Service Manual 3 55 Parts Lists ...
Page 97: ...3 99 DocuPrint N24 N32 and N40 Service Manual 3 57 Parts Lists ...
Page 99: ...3 99 DocuPrint N24 N32 and N40 Service Manual 3 59 Parts Lists ...
Page 101: ...3 99 DocuPrint N24 N32 and N40 Service Manual 3 61 Parts Lists ...
Page 103: ...3 99 DocuPrint N24 N32 and N40 Service Manual 3 63 Parts Lists ...
Page 105: ...3 99 DocuPrint N24 N32 and N40 Service Manual 3 65 Parts Lists ...
Page 107: ...2 2000 DocuPrint N24 N32 N40 N3225 and N4025 3 67 Parts Lists ...
Page 109: ...2 2000 DocuPrint N24 N32 N40 N3225 and N4025 3 69 Parts Lists ...
Page 114: ...2 2000 Parts Lists 3 74 DocuPrint N24 N32 N40 N3225 and N4025 Notes ...
Page 334: ...3 99 Wiring Data 6 4 DocuPrint N24 N32 and N40 Service Manual ...
Page 344: ...3 99 Wiring Data 6 14 DocuPrint N24 N32 and N40 Service Manual 6 3 2 AC Driver PWB Fuser ...
Page 353: ...3 99 DocuPrint N24 N32 and N40 Service Manual 6 23 Wiring Data 6 3 16 Offset Exit Assembly ...
Page 354: ...3 99 Wiring Data 6 24 DocuPrint N24 N32 and N40 Service Manual 6 3 17 Mailbox 6 3 18 Finisher ...
Page 455: ...3 99 DocuPrint N24 N32 and N40 Service Manual 8 17 Options ...
Page 457: ...3 99 DocuPrint N24 N32 and N40 Service Manual 8 19 Options ...
Page 459: ...3 99 DocuPrint N24 N32 and N40 Service Manual 8 21 Options ...
Page 461: ...3 99 DocuPrint N24 N32 and N40 Service Manual 8 23 Options ...
Page 463: ...3 99 DocuPrint N24 N32 and N40 Service Manual 8 25 Options ...
Page 464: ...3 99 Options 8 26 DocuPrint N24 N32 and N40 Service Manual This Page Intentionally Left Blank ...
Page 482: ...3 99 Options 8 44 DocuPrint N24 N32 and N40 Service Manual This Page Intentionally Left Blank ...
Page 484: ...3 99 Options 8 46 DocuPrint N24 N32 and N40 Service Manual This Page Intentionally Left Blank ...
Page 492: ...3 99 Options 8 54 DocuPrint N24 N32 and N40 Service Manual This Page Intentionally Left Blank ...
Page 500: ...3 99 Options 8 62 DocuPrint N24 N32 and N40 Service Manual This Page Intentionally Left Blank ...
Page 505: ...3 99 DocuPrint N24 N32 and N40 Service Manual 8 67 Options ...
Page 507: ...3 99 DocuPrint N24 N32 and N40 Service Manual 8 69 Options ...
Page 509: ...3 99 DocuPrint N24 N32 and N40 Service Manual 8 71 Options ...
Page 511: ...3 99 DocuPrint N24 N32 and N40 Service Manual 8 73 Options ...
Page 513: ...3 99 DocuPrint N24 N32 and N40 Service Manual 8 75 Options ...
Page 515: ...3 99 DocuPrint N24 N32 and N40 Service Manual 8 77 Options ...
Page 517: ...3 99 DocuPrint N24 N32 and N40 Service Manual 8 79 Options ...
Page 519: ...3 99 DocuPrint N24 N32 and N40 Service Manual 8 81 Options ...
Page 520: ...3 99 Options 8 82 DocuPrint N24 N32 and N40 Service Manual This Page Intentionally Left Blank ...
Page 550: ...3 99 Options 8 112 DocuPrint N24 N32 and N40 Service Manual ...
Page 551: ...3 99 DocuPrint N24 N32 and N40 Service Manual 8 113 Options ...
Page 552: ...3 99 Options 8 114 DocuPrint N24 N32 and N40 Service Manual WIR 8 2 5 2 Plug Jack Locator ...
Page 556: ...3 99 Options 8 118 DocuPrint N24 N32 and N40 Service Manual ...
Page 569: ...3 99 DocuPrint N24 N32 and N40 Service Manual 8 131 Options ...
Page 571: ...3 99 DocuPrint N24 N32 and N40 Service Manual 8 133 Options ...
Page 573: ...3 99 DocuPrint N24 N32 and N40 Service Manual 8 135 Options ...
Page 603: ...3 99 DocuPrint N24 N32 and N40 Service Manual 8 165 Options ...
Page 605: ...2 2000 DocuPrint N24 N32 N40 N3225 and N4025 8 167 Options ...
Page 607: ...3 99 DocuPrint N24 N32 and N40 Service Manual 8 169 Options ...
Page 609: ...3 99 DocuPrint N24 N32 and N40 Service Manual 8 171 Options ...
Page 611: ...3 99 DocuPrint N24 N32 and N40 Service Manual 8 173 Options ...
Page 613: ...3 99 DocuPrint N24 N32 and N40 Service Manual 8 175 Options ...
Page 615: ...3 99 DocuPrint N24 N32 and N40 Service Manual 8 177 Options ...
Page 617: ...3 99 DocuPrint N24 N32 and N40 Service Manual 8 179 Options ...
Page 619: ...3 99 DocuPrint N24 N32 and N40 Service Manual 8 181 Options ...
Page 621: ...3 99 DocuPrint N24 N32 and N40 Service Manual 8 183 Options ...
Page 623: ...3 99 DocuPrint N24 N32 and N40 Service Manual 8 185 Options ...
Page 625: ...3 99 DocuPrint N24 N32 and N40 Service Manual 8 187 Options ...
Page 627: ...3 99 DocuPrint N24 N32 and N40 Service Manual 8 189 Options ...
Page 629: ...3 99 DocuPrint N24 N32 and N40 Service Manual 8 191 Options ...
Page 668: ...2 2000 Options 8 230 DocuPrint N24 N32 N40 N3225 and N4025 ...
Page 669: ...3 99 DocuPrint N24 N32 and N40 Service Manual 8 231 Options ...
Page 703: ...2 2000 DocuPrint N24 N32 N40 N3225 and N4025 8 265 Options ...
Page 705: ...3 99 DocuPrint N24 N32 and N40 Service Manual 8 267 Options ...
Page 707: ...3 99 DocuPrint N24 N32 and N40 Service Manual 8 269 Options ...
Page 709: ...3 99 DocuPrint N24 N32 and N40 Service Manual 8 271 Options ...
Page 711: ...3 99 DocuPrint N24 N32 and N40 Service Manual 8 273 Options ...
Page 713: ...3 99 DocuPrint N24 N32 and N40 Service Manual 8 275 Options ...
Page 715: ...3 99 DocuPrint N24 N32 and N40 Service Manual 8 277 Options ...
Page 717: ...3 99 DocuPrint N24 N32 and N40 Service Manual 8 279 Options ...
Page 719: ...3 99 DocuPrint N24 N32 and N40 Service Manual 8 281 Options ...
Page 721: ...3 99 DocuPrint N24 N32 and N40 Service Manual 8 283 Options ...
Page 723: ...3 99 DocuPrint N24 N32 and N40 Service Manual 8 285 Options ...
Page 725: ...3 99 DocuPrint N24 N32 and N40 Service Manual 8 287 Options ...
Page 727: ...3 99 DocuPrint N24 N32 and N40 Service Manual 8 289 Options ...
Page 729: ...2 2000 DocuPrint N24 N32 N40 N3225 and N4025 8 291 Options ...
Page 731: ...3 99 DocuPrint N24 N32 and N40 Service Manual 8 293 Options ...
Page 733: ...3 99 DocuPrint N24 N32 and N40 Service Manual 8 295 Options ...
Page 735: ...3 99 DocuPrint N24 N32 and N40 Service Manual 8 297 Options ...
Page 737: ...3 99 DocuPrint N24 N32 and N40 Service Manual 8 299 Options ...
Page 739: ...2 2000 DocuPrint N24 N32 N40 N3225 and N4025 8 301 Options ...
Page 741: ...3 99 DocuPrint N24 N32 and N40 Service Manual 8 303 Options ...
Page 743: ...3 99 DocuPrint N24 N32 and N40 Service Manual 8 305 Options ...
Page 745: ...3 99 DocuPrint N24 N32 and N40 Service Manual 8 307 Options ...
Page 747: ...2 2000 DocuPrint N24 N32 N40 N3225 and N4025 8 309 Options ...
Page 749: ...2 2000 DocuPrint N24 N32 N40 N3225 and N4025 8 311 Options ...
Page 791: ...3 99 DocuPrint N24 N32 and N40 Service Manual 8 353 Options Figure 8 5 3 27a Bottom Bin ...
Page 793: ...3 99 DocuPrint N24 N32 and N40 Service Manual 8 355 Options Figure 8 5 3 28a Bin Assembly ...
Page 807: ...3 99 DocuPrint N24 N32 and N40 Service Manual 8 369 Options Figure 8 5 3 37a Middle Bin ...
Page 809: ...3 99 DocuPrint N24 N32 and N40 Service Manual 8 371 Options Figure 8 5 3 38a Bin Assembly ...
Page 823: ...3 99 DocuPrint N24 N32 and N40 Service Manual 8 385 Options Figure 8 5 3 47a Top Bin ...
Page 839: ...3 99 DocuPrint N24 N32 and N40 Service Manual 8 401 Options Figure 8 5 3 56a End Wall Motor ...
Page 857: ...3 99 DocuPrint N24 N32 and N40 Service Manual 8 419 Options Figure 8 5 3 65a Exit Shaft ...
Page 881: ...3 99 DocuPrint N24 N32 and N40 Service Manual 8 443 Options Figure 8 5 3 81a Eject Motor ...
Page 885: ...3 99 DocuPrint N24 N32 and N40 Service Manual 8 447 Options Figure 8 5 3 83a Finisher PWB ...
Page 906: ...3 99 Options 8 468 DocuPrint N24 N32 and N40 Service Manual ...
Page 907: ...3 99 DocuPrint N24 N32 and N40 Service Manual 8 469 Options ...
Page 908: ...3 99 Options 8 470 DocuPrint N24 N32 and N40 Service Manual ...
Page 909: ...3 99 DocuPrint N24 N32 and N40 Service Manual 8 471 Options ...
Page 910: ...3 99 Options 8 472 DocuPrint N24 N32 and N40 Service Manual ...
Page 911: ...3 99 DocuPrint N24 N32 and N40 Service Manual 8 473 Options ...
Page 912: ...3 99 Options 8 474 DocuPrint N24 N32 and N40 Service Manual ...
Page 913: ...3 99 DocuPrint N24 N32 and N40 Service Manual 8 475 Options ...
Page 914: ...3 99 Options 8 476 DocuPrint N24 N32 and N40 Service Manual ...
Page 915: ...3 99 DocuPrint N24 N32 and N40 Service Manual 8 477 Options ...
Page 916: ...3 99 Options 8 478 DocuPrint N24 N32 and N40 Service Manual ...
Page 926: ...3 99 Options 8 488 DocuPrint N24 N32 and N40 Service Manual ...
Page 932: ...3 99 Options 8 494 DocuPrint N24 N32 and N40 Service Manual ...
Page 937: ...3 99 DocuPrint N24 N32 and N40 Service Manual 8 499 Options ...