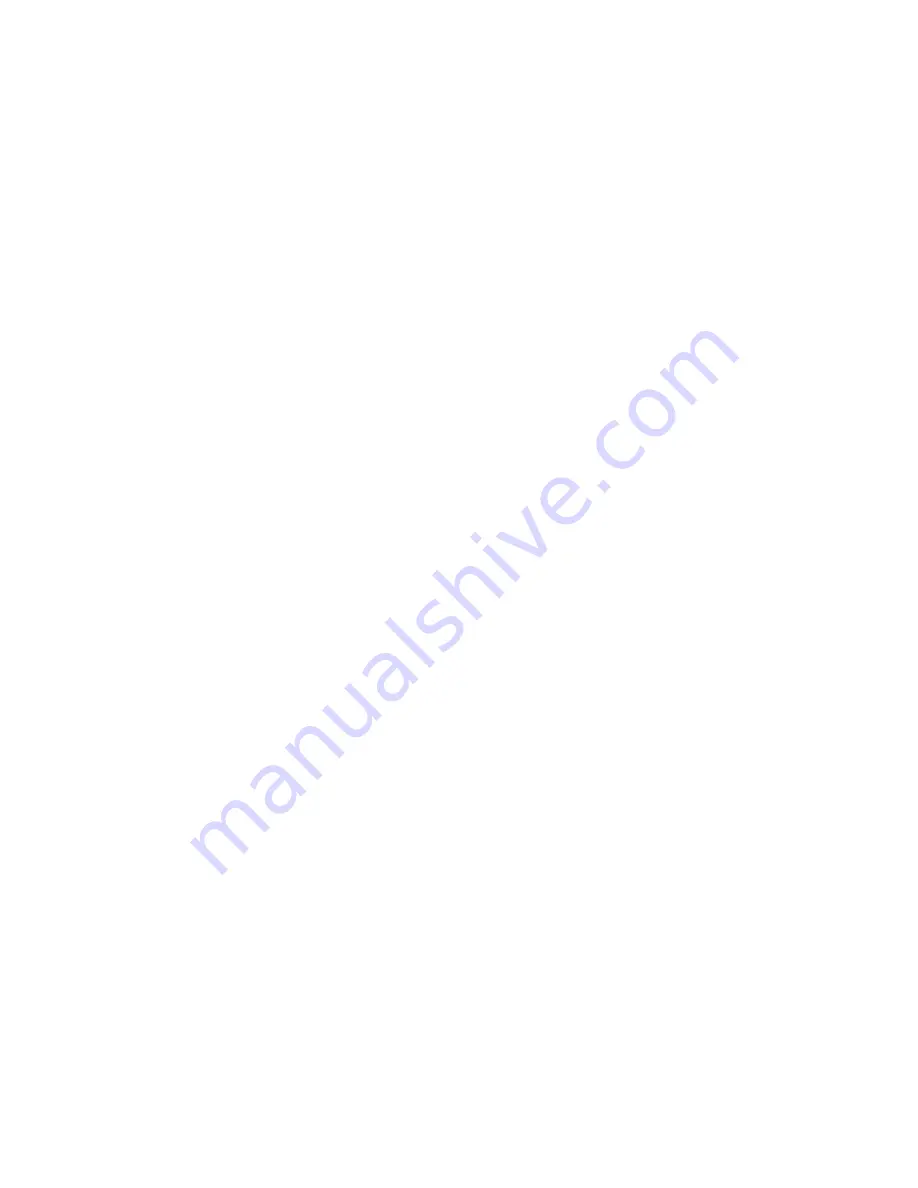
Installation
Functional Tests
44
Operating Manual for XFR 2.8kW Series Power Supply
Current Mode
Operation
Check
1. Ensure the front panel AC power switch is set to OFF.
2. Turn the voltage and current controls on the front panel fully counter-clockwise.
3. Connect the DC shunt across the output terminals on the rear panel.
4. Connect the DVM across the DC shunt.
5. Turn the AC power switch to ON.
6. Turn the voltage control 1 or 2 turns clockwise.
7. Turn the current control slowly clockwise.
8. Compare the DVM reading with the front panel ammeter reading using I=V/R
where I is the current, V is the DVM reading, and R is the DC shunt resistance.
The minimum control range is from zero to the maximum rated output for the
power supply model. The current mode LED turns on.
9. Turn the AC power switch to OFF.
10. Disconnect the DVM and the shunt.
Front Panel
Function
Checks
1. Turn the front panel AC switch to ON.
2. Set voltage and current controls fully clockwise. Push the STANDBY switch to
its IN position and check that the voltmeter reading falls to zero and the red S/D
(Shutdown) LED turns on. Push the STANDBY switch once again to reset it to
its OUT position. The S/D LED turns off and the voltmeter reading returns to its
previous value.
3. Press the STANDBY switch to its IN position.
4. Press the OVP CHECK switch and check that the voltmeter displays
approximately the model-rated output voltage plus 10%.
5. Turn the OVP SET potentiometer counter-clockwise and check that the
voltmeter reading decreases. Continued turning (up to 20 turns) will see the
reading decrease to approximately 5% of the model-rated voltage output. Turn
the OVP SET potentiometer clockwise until the voltmeter once again displays
approximately the model-rated output voltage plus 10%.
6. Press the STANDBY switch to its OUT position.
7. Press the V/I CHECK switch and check that the voltmeter and ammeter display
the power supply output ratings.
8. Turn the front panel AC power switch to OFF.
Note:You can use the front panel LOCAL button only when a digital programming
interface has been installed in your power supply