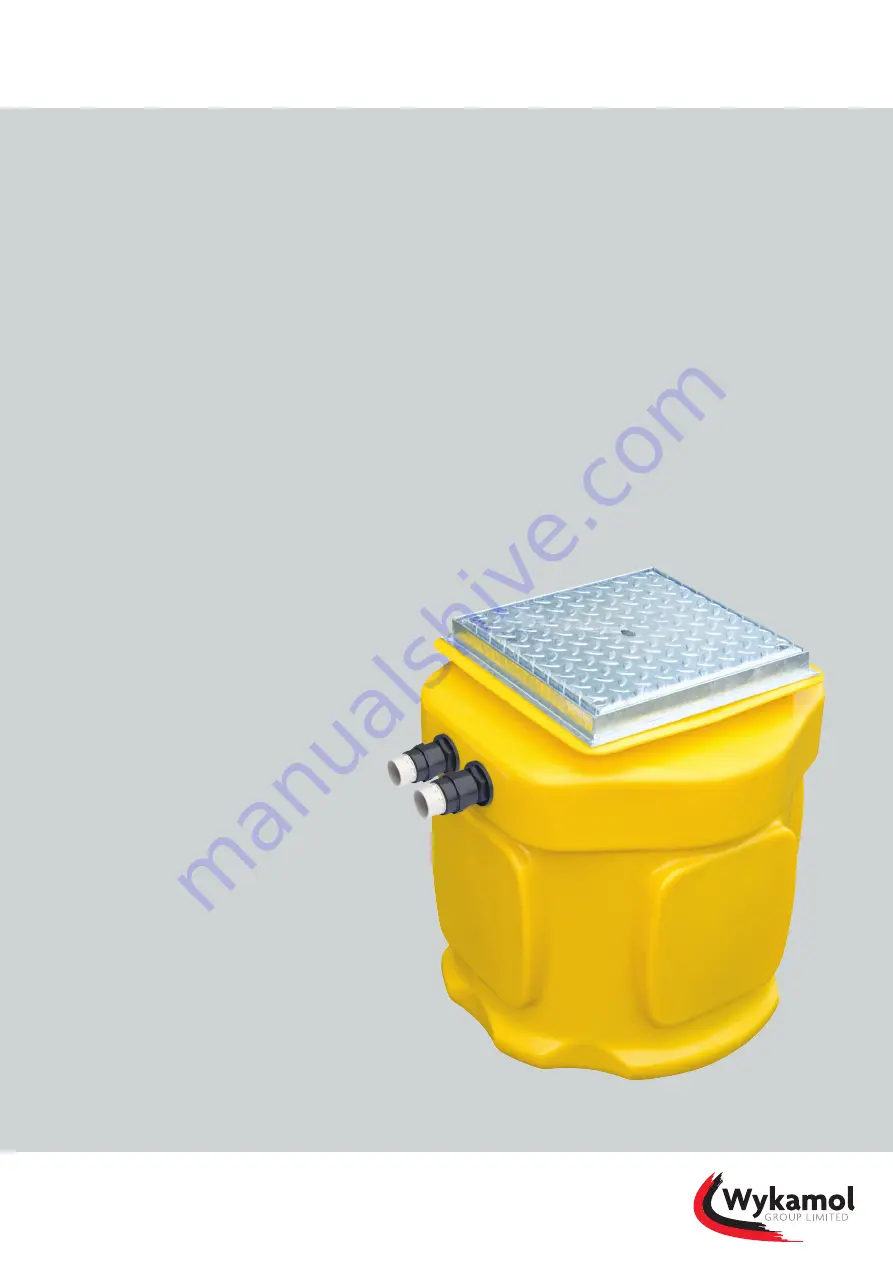
WASTE WATER PUMPING SYSTEMS
Wykamol SumpFlo
™
Installation and operating guidelines
The Wykamol SumpFlo is a range of fully automatic waste water pump station,
suitable for pumping ground water from a cavity membrane system and/or
surface water from lightwells to a higher level.
Models
SumpFlo
SumpFloTwin (single discharge)
SumpFloTwin (twin discharge)
SumpFlo BBPS (single discharge)
SumpFlo BBPS (twin discharge)
SumpFloTwin BBPS (twin discharge)
Technical advice: 0845 400 6666
www.wykamol.com