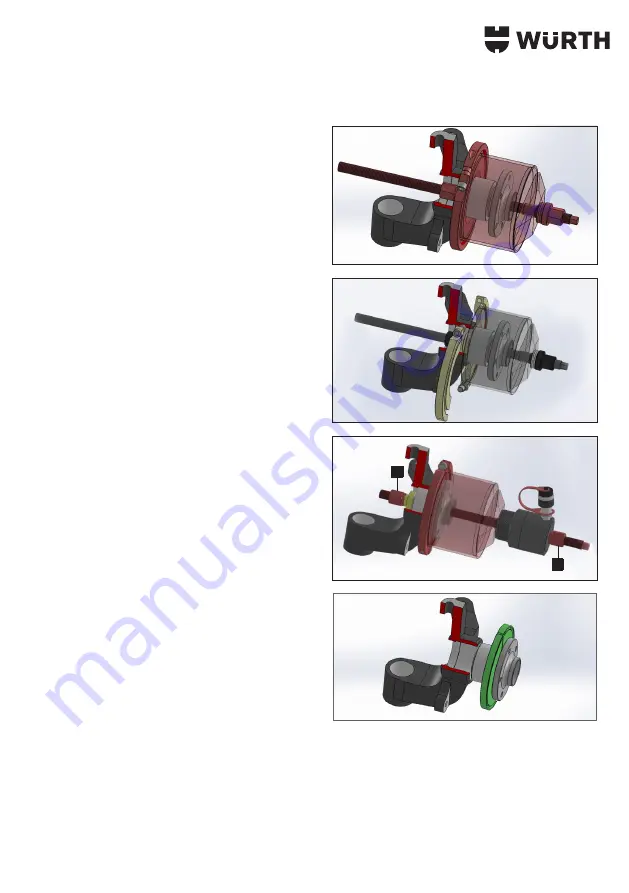
25
4
5
6
G
G
7
cylinder, fit the cylinder between the bell and a second counter-
nut (G) (Fig.6).
Now actuate the cylinder that, by axially translating the screw,
allows you to remove the integrated hub from its seat.
- Since the cylinder has a max stroke of 43 mm, if the removal
was not performed completely, this operation can be repeated
several times by discharging the hydraulic cylinder (single-acting
cylinder with spring return) and then tightening the counter-nut
(G) again against the cylinder.
We recommend the use of the cylinder combined with the 700-bar
manual hydraulic pump, 1952 004 001, in our WÜRTH catalog.
INSERTION
During insertion, the thrust force is exerted in the groove at the bottom
of the bearing's outer cage (see fig. 1), through the insertion semirings
(H) that are held together by means of the bell (D).
Carry out the insertion by assembling the following tool set
components as shown in fig. 9:
•
2 insertion semirings (H), of suitable diameter (see fig. 1 and 8,
for correct positioning);
•
Insertion ring (I), appropriately sized to the diameter of the
bearing seat;
•
Thrust bell (D);
•
Screw M20x1.5 (E);
•
Nut + bearing (F);
•
Counter-nut (G).
Manual operation
- Manually tighten only the nut + bearing (F) on the screw
M20x1.5 (E), so as to push the bell (D), jointly with the 2
insertion semirings (H) and the integrated HBU bearing, against
the insertion ring (I), until the integrated HBU bearing has been
fully inserted into its seat (fig. 9).
Operation with 17-ton hydraulic cylinder (UPGRADE
OPTION - 1952 004 090)
- The hydraulic cylinder is placed between the bell (D) and a
second counter-nut (G) (fig. 11). Now actuate the cylinder
that, by axially translating the screw, allows you to insert the
integrated HBU bearing into its seat. As when the bearing
had been removed, repeat the operation until it is completely
inserted.
We recommend the use of the cylinder combined with the 700-bar
manual hydraulic pump, 1952 004 001, in our WÜRTH catalog.