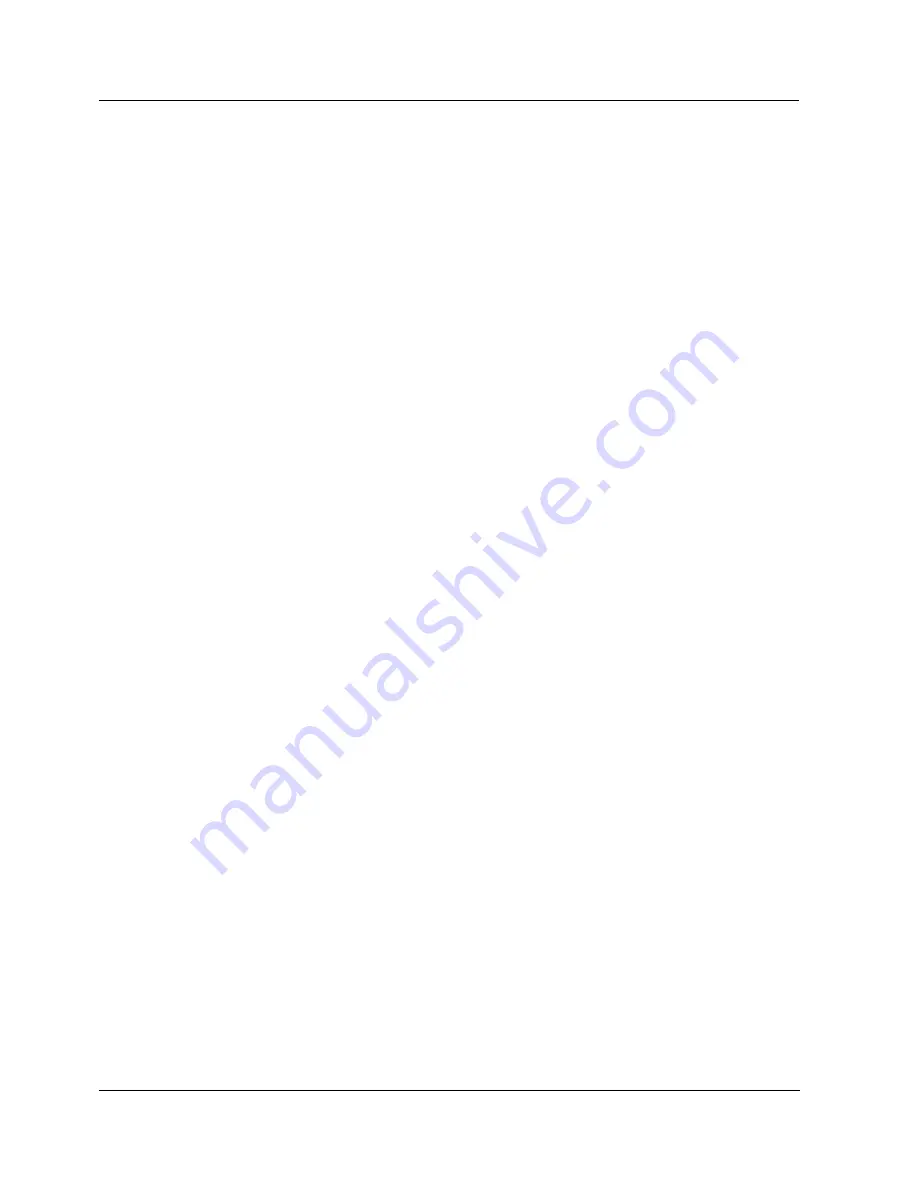
Interface for the Modbus RTU
MIQ/2-MOD
12
ba75973e01
07/2012
3.2
Modbus checklist
The following checklist supports you when planning, projecting and
installing a Modbus plant with the IQ S
ENSOR
N
ET
. For smooth
operation, you should be able to answer all questions with "Yes".
Is the [bus system] (bus segment) installed without branch lines?
Was the correct Modbus cable used (cord type A according to
EN 50170)?
Are the poles of the signal lines A line and B line correctly connected
at all bus connections?
Is it guaranteed that there is no short-circuit between A line, B line
and cable shielding?
Is the shielding installed free of interruptions?
Are the guidelines for shielding and grounding being observed, and
doesn't any unallowed potential equalization current flow
via the shielding?
Is the maximum cable length (per bus segment) observed for the
corresponding baud rate?
Do all devices support the required baud rate?
Are exactly two terminators switched on at the ends of the [bus
system] (bus segment)?
Are the terminators supplied with voltage so the following applies:
U
B line
- U
A line
> + 500 mV?
Do all devices have individual bus addresses?
After changing the bus address, have the devices been restarted
(switched off and on again)? Note: The IQ S
ENSOR
N
ET
does not
have to be restarted.
Do the addresses projected in the master correspond to the actual
addresses?
After commissioning:
Do all devices signal error-free behavior?
Is it guaranteed that the Modbus master has consistent access
to the 16 byte sensor data structure?