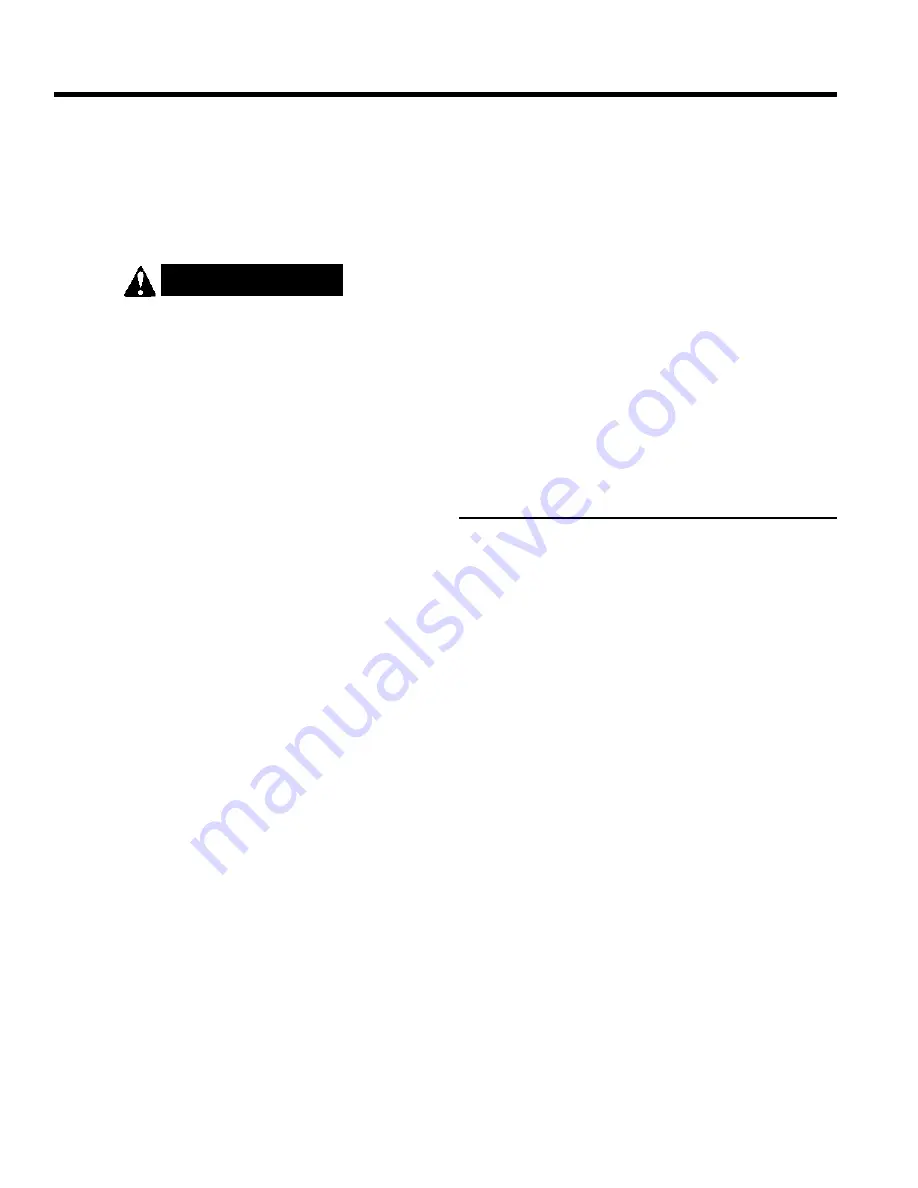
25
OWNER SERVICE
The information in this section is written for operators
who possess basic mechanical skills. Should you need
help, your dealer has trained service technicians
available. For your protection, read and follow all safety
information in this manual.
▲
▲
Before servicing the machine, disengage the PTO,
engage the parking brake or place the transmis-
sion in “Park,” shut off the power unit and remove
the key. Disconnect stump grinder driveline from
tractor PTO before performing any service or
maintenance.
▲
▲
Before working underneath, raise 3 pt. hitch to
highest position and block stump grinder secure-
ly. Hydraulic system leakdown and failure of
mechanical or hydraulic system can cause equip-
ment to drop.
▲
▲
Keep all persons away from operator control area
while performing adjustments, service or mainte-
nance.
Daily lubrication of the PTO slip joint is necessary.
Failure to maintain proper lubrication can result in
damage to U-joints, gearbox, tractor PTO and/or stump
grinder driveline.
LUBRICATION CHART
DESCRIPTION
FREQUENCY
Front U-Joint (PTO)
8 Hrs.
Rear U-Joint (PTO)
8 Hrs.
Gearbox – Fill to proper level
Check Daily
Slip Joint (PTO)
8 Hrs.
Swing Arm Pivot Joint
8 Hrs.
REPLACING CUTTING TEETH
——————————————————
The laminated design of this stump grinder cutting
wheel provides a “pocket” for each cutting tooth. This
“pocket” design supports each cutting tooth so it can han-
dle the loads encountered in the stump grinding opera-
tion.
It is VERY IMPORTANT that when replacing a cutting
tooth the empty “pocket” be checked for any possible dirt
accumulation. ALWAYS make sure that the “pocket” is
CLEAN BEFORE inserting a replacement cutting tooth.
If any dirt is in the “pocket” and the tooth installed, it will
not be seated properly and the bolt holding the tooth
could come loose. Operating with a loose cutting tooth
could result not only in the loss of the tooth, but damage
to the “pocket” in the wheel.
When rotating cutting teeth, always clean each tooth
before installing it in its “new” pocket location.
ROUTINE MAINTENANCE
——————————————————
DAILY CHECKS:
1. Check that all bolts, nuts, and screws are tight.
Checking the bolts and nuts on the cutting wheel is
particularly important.
2. Check daily the level of the gearbox oil and top up to
the correct level. Check for gearbox oil leaks. It should
be noted that no warranty claim can be submitted on a
gearbox that has run dry. It is essential that the gear-
box is kept correctly filled with gearbox oil.
3. Grease the PTO shaft daily.
4. Check the wear on the cutting teeth. You should keep
at least one set of cutting teeth as spares.
5. Check hydraulic hoses. Make sure they are not chafed
or pinched. Replace any damaged hose.
6. Check hydraulic hoses and fittings for leaks. Repair
any leaks immediately. Never use your hand to check
for a hydraulic leak when system is under pressure.
7. Replace any worn or damaged parts immediately. Do
not use attachment with any damaged parts.
LUBRICATION INFORMATION
——————————————————
The chart gives the frequency of lubrication in operat-
ing hours, based on normal conditions. Severe or unusu-
al conditions may require more frequent lubrication.
Do not let excess grease collect on or around parts,
particularly when operating in sandy areas.
Use an SAE 90W gear lube in gearbox.
Use a lithium grease of NO. 2 consistency with a MOLY
(molybdenum disulfide) additive for all locations. Be sure
to clean fittings thoroughly before attaching grease gun.
When applied according to the lubrication chart, one
good pump of most guns is sufficient. Do not over grease.
Thoroughly clean the grease zerks before servicing. Dirt
mixed with lubricant will rapidly wear parts and destroy
bearings. Keep it clean.
WARNING
Summary of Contents for SG-26A
Page 33: ...32 SG 26A SG 36A STUMP GRINDER HYDRAULIC DIAGRAM PARTS LIST...
Page 34: ...33 SG 26A STUMP GRINDER PARTS DRAWING...
Page 36: ...35 SG 36A STUMP GRINDER PARTS DRAWING...
Page 38: ...37 SG 26A GEARBOX PARTS DRAWING LIST...
Page 39: ...38 SG 36A GEARBOX PARTS DRAWING LIST...
Page 40: ...39 SG 26A PTO SHAFT PARTS DRAWING LIST...