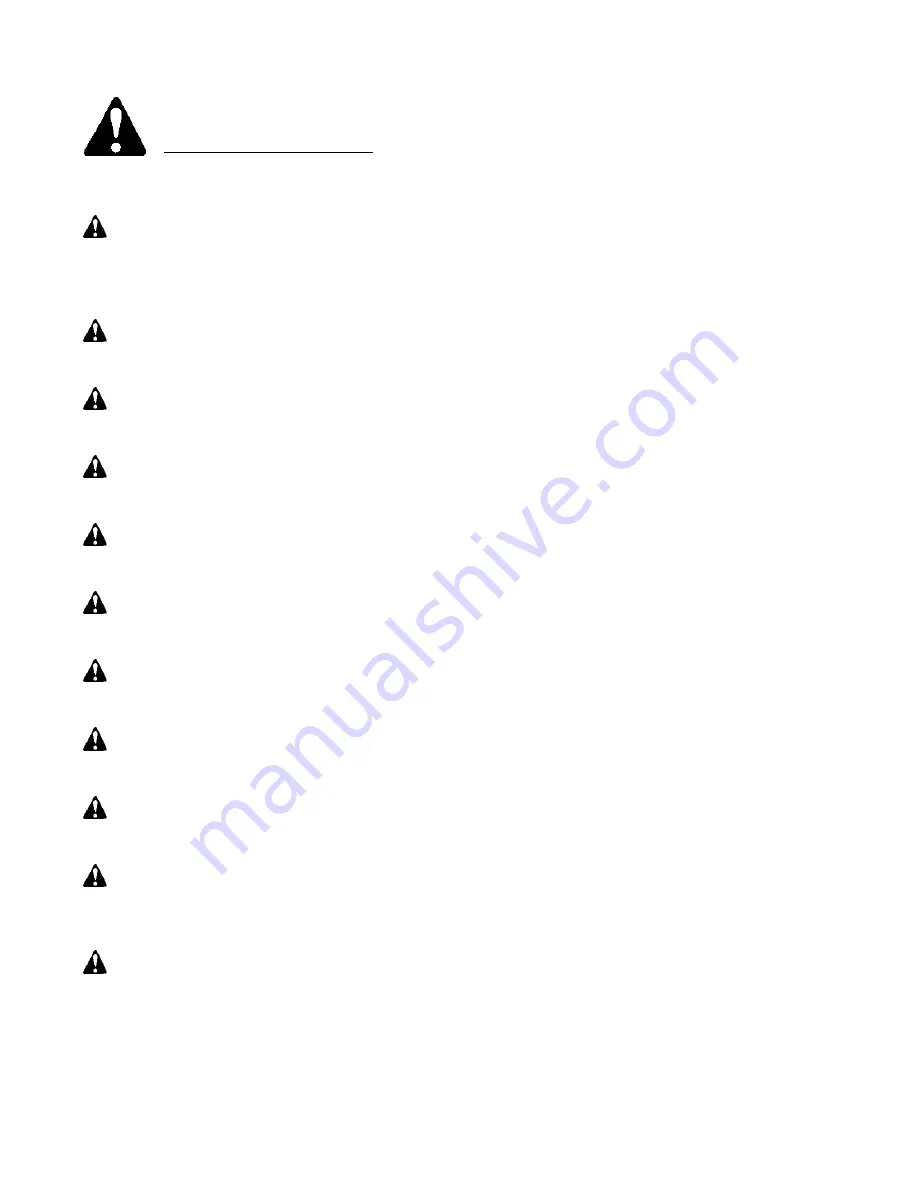
12
SAFETY INSTRUCTIONS
(continued)
MAINTENANCE SAFETY
Good maintenance is your responsibility. Poor maintenance is an invitation to trouble.
Before working on this machine, drive to a level area, disengage the PTO, lower implement (or if working
underneath, raise and block securely), shut off the engine, set the brakes, and remove the ignition keys.
Remove hydraulic pressure prior to doing any maintenance. Operate the remote hydraulic control lever in and
out several times to relieve hydraulic pressure.
Be certain all moving parts on attachments have come to a complete stop before attempting to perform
maintenance.
Never work under equipment unless it is blocked securely. Never depend on hydraulic system to keep imple-
ment in raised position.
Always use personal protection devices such as eye, hand and hearing protectors, when performing any
service or maintenance.
Keep all persons away from operator control area while performing adjustments, service, or maintenance.
Periodically tighten all bolts, nuts and screws and check that all cotter pins are properly installed to ensure unit
is in a safe condition.
When completing a maintenance or service function, make sure all safety shields and devices are installed
before placing unit in service.
Never use your hands to locate a hydraulic leak on attachments. Use a small piece of cardboard or wood.
Hydraulic fluid escaping under pressure can penetrate the skin.
Openings in the skin and minor cuts are susceptible to infection from hydraulic fluid. If injured by escaping
hydraulic fluid, see a doctor at once. Gangrene and death can result. Without immediate medical treatment,
serious infection and reactions can occur.
Check to ensure all safety signs are installed and in good condition.
Where replacement parts are necessary for periodic maintenance and servicing, genuine factory replacement parts
must be used to restore your equipment to original specifications. The manufacturer will not claim responsibility for use
of unapproved parts and/or accessories and other damages as a result of their use.
If equipment has been altered in any way from original design, the manufacturer does not accept any liability for injury
or warranty.
Frequently check carbide tipped cutting teeth. They should be sharp, free of nicks and cracks and securely fas-
tened. Rotate teeth for even wear – outer teeth wear faster.
Summary of Contents for SG-26A
Page 33: ...32 SG 26A SG 36A STUMP GRINDER HYDRAULIC DIAGRAM PARTS LIST...
Page 34: ...33 SG 26A STUMP GRINDER PARTS DRAWING...
Page 36: ...35 SG 36A STUMP GRINDER PARTS DRAWING...
Page 38: ...37 SG 26A GEARBOX PARTS DRAWING LIST...
Page 39: ...38 SG 36A GEARBOX PARTS DRAWING LIST...
Page 40: ...39 SG 26A PTO SHAFT PARTS DRAWING LIST...