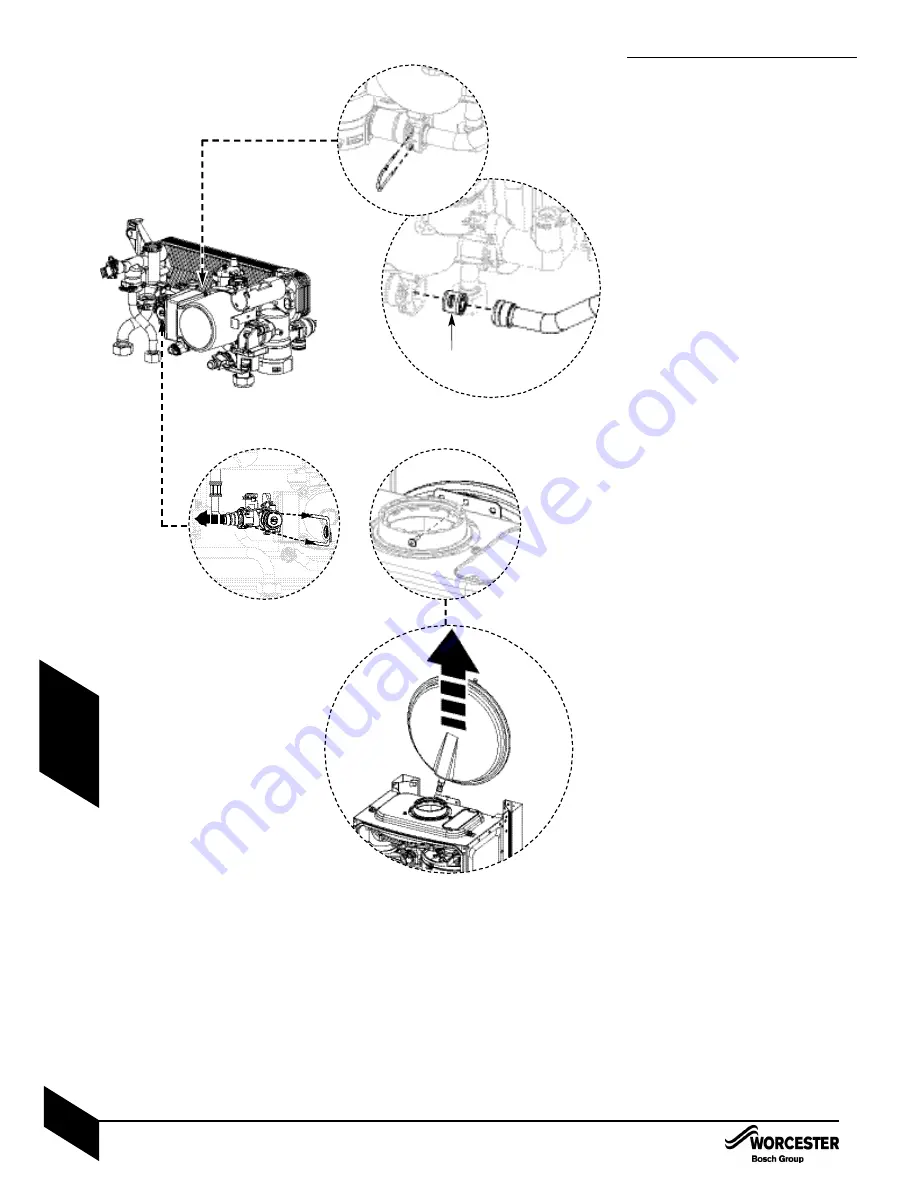
REPLACEMENT OF PARTS
31. Bypass valve
Remove the Hydraulic block from the boiler
(See Removing the Hydraulic Block).
31.1
Remove the two spring clips at either end of
the copper bypass pipe.
Undo the screw securing the left hand
plastic housing to the heat exchanger
Move the housing to the left to free up the
one end of the pipe.
Remove the pipe from the right hand housing
to reveal the bypass valve
31.2
Using a pair of pliers, pull out the bypass
valve (A) from the housing
To refit, follow the above in reverse. Ensure
any seals that have been disturbed are
renewed.
32. Expansion vessel
The expansion vessel can be replaced with the
boiler in position if there is a side exit flue fitted
and there is a minimum clearance of 340mm
above the boiler casing. If vertical flue is fitted
then a similar clearance to one side and the flue
is required.
If clearance is not available, the boiler will need to
be removed from the mounting frame to gain
access to the expansion vessel.
Alternatively a second vessel of at least the
capacity of 7lts can be fitted to the return from
the heating system as close as possible to the
boiler.
Expansion vessel replacement
(Boiler in place)
Isolate mains power from the boiler.
Place the controls in service position.
Isolate the boiler from the heating system
(and cylinder return if internal diverter valve is
fitted) using service valves.
Drain boiler.
32.1
Remove clip from expansion vessel
connection.
32.2
Remove screw retaining the vessel to the top
of the boiler casing.
32.3
Pull the vessel up and out over the flue
system or to one side if fitted with a vertical
flue.
Remove the flexible hose from the expansion
vessel and fit to the replacement vessel
using a new seal. Ensure that the connection
to the boiler will be pointing to the right hand
side of the appliance when fitted.
Reassemble expansion vessel into boiler and
connect flexible pipe to boiler.
Removing boiler
Isolate electrical supply.
Isolate system and gas connections at the
service valves.
Drain boiler.
Disconnect electrical supply and any external
controls.
Disconnect flue connection from the boiler.
Undo connection to boiler at the service valves.
Remove clip from expansion vessel
connection to the boiler.
Gently raise the boiler off the mounting frame.
Replace expansion vessel and refit the boiler
to the mounting frame.
Follow the commissioning procedure in this
manual.
31.2
A
31.1
32.3
32.1
32.2
REPLACEMENT OF PARTS
INSTALLATION & SERVICING INSTRUCTIONS FOR WORCESTER GREENSTAR 25Si/30Si
8 716 107 337b (11/05)
51
SER
V
IC
IN
G
&
SP
A
RES