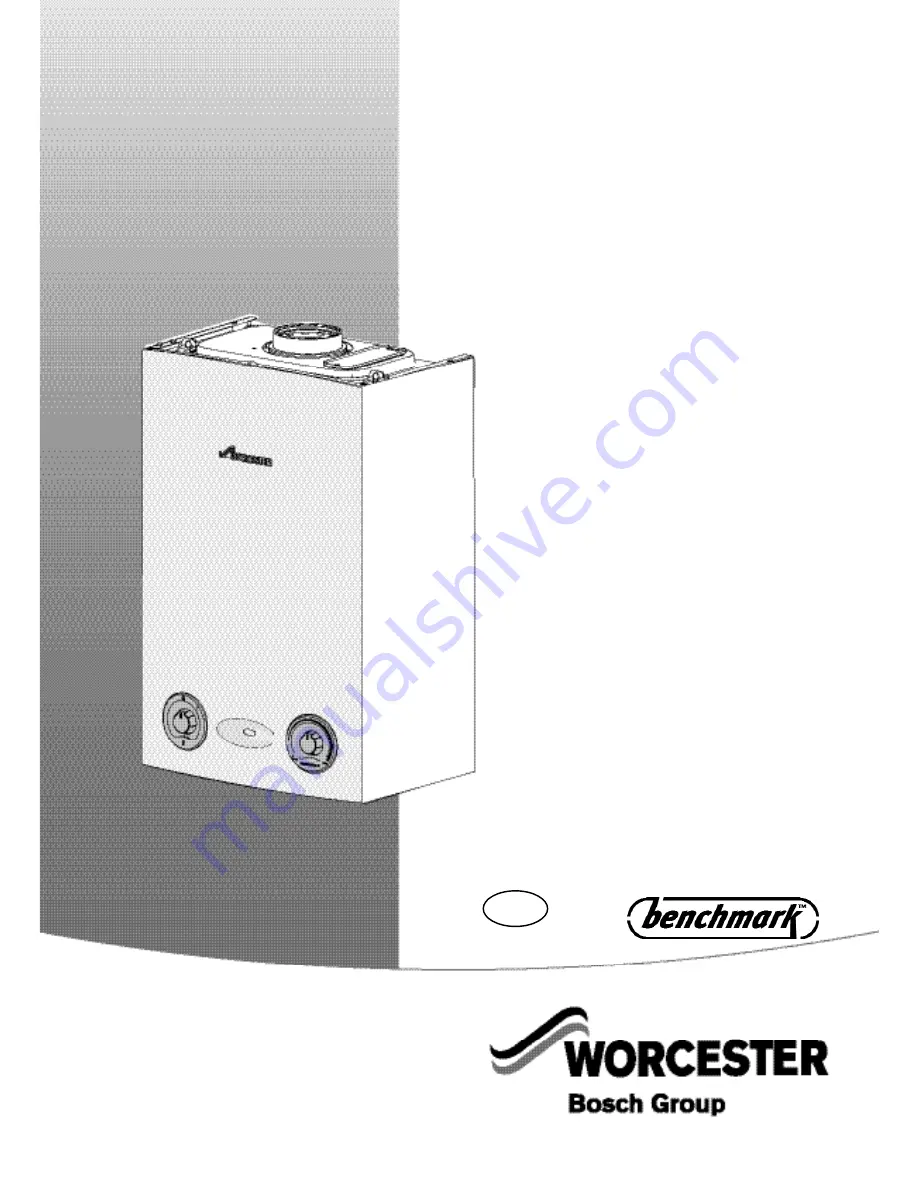
UK/IE
INSTRUCTION MANUAL
INSTALLATION, COMMISSIONING & SERVICING
WALL HUNG RSF GAS FIRED CONDENSING BOILER
FOR OPEN VENTED AND SEALED CENTRAL HEATING SYSTEMS AND
INDIRECT MAINS FED DOMESTIC HOT WATER
THIS BOILER IS USED WITH
NATURAL GAS OR LPG (Cat II 2H3P TYPE C13, C33 & C53)
NATURAL GAS
12 Ri GC NUMBER: 41 311 63
15 Ri GC NUMBER: 41 311 75
18 Ri GC NUMBER: 41 311 77
24 Ri GC NUMBER: 41 311 65
LIQUID PETROLEUM GAS
12 Ri GC NUMBER: 41 311 64
15 Ri GC NUMBER: 41 311 76
18 Ri GC NUMBER: 41 311 78
24 Ri GC NUMBER: 41 311 66
GREENSTAR 12Ri, 15Ri, 18Ri & 24Ri