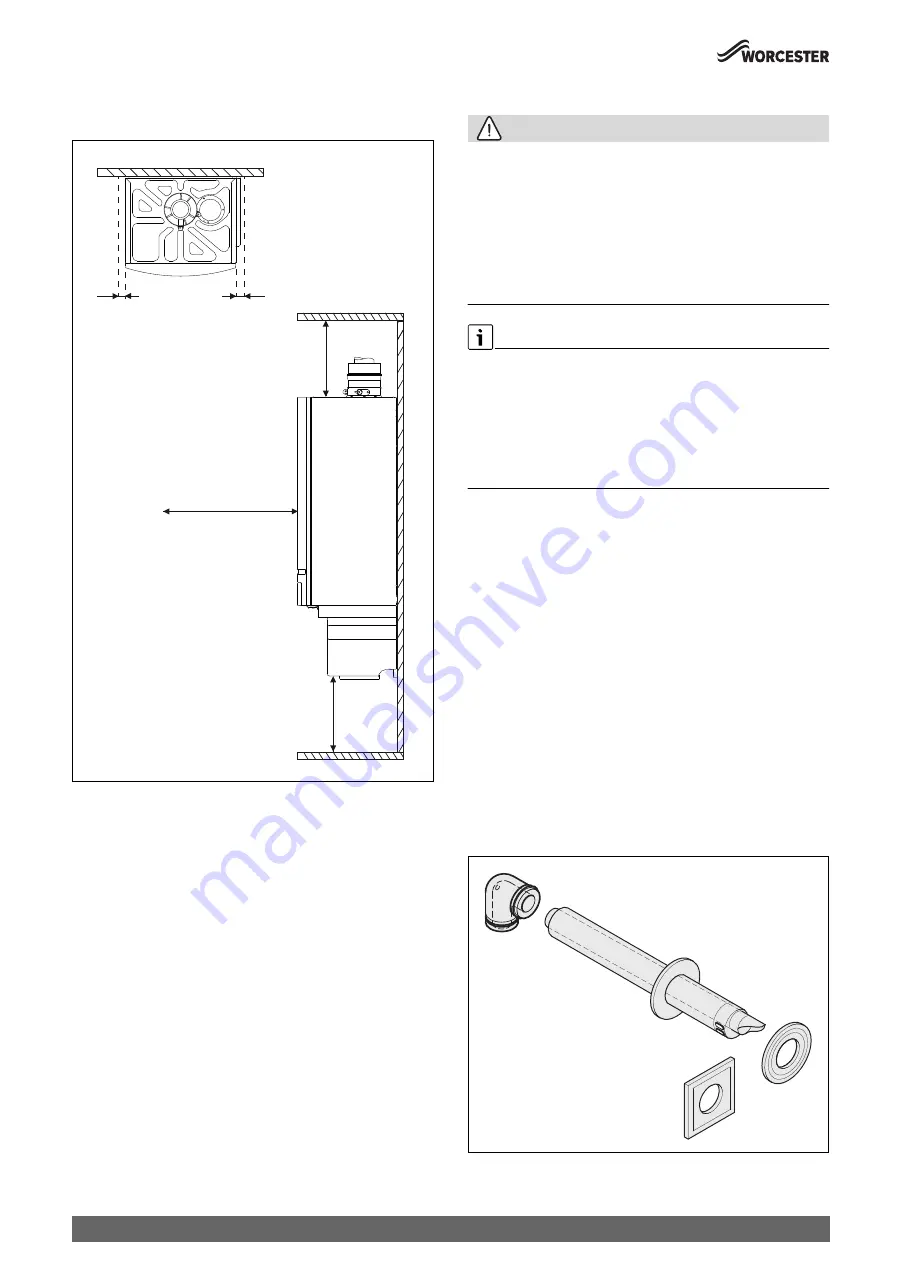
Pre-Installation
Worcester Commercial Boiler Series – 6720814332 (2019/04)
18
3.7
Boiler location and clearances
3.7.1
Installation and servicing clearances
Fig. 21 Clearances [mm]
3.7.2
Compartments
Follow the requirements of BS6798 and BS5440 Part 2 and note:
• Minimum clearances must be maintained.
• If fitting the appliance into an airing cupboard use a non-combustible
material to separate the appliance from the airing space. The material
can be perforated up to a maximum hole size of 13mm.
• An access door is required to install, service and maintain the
appliance and any ancillary equipment.
3.7.3
Bathrooms
If the boiler is fitted in bathrooms, additional RCD (Residual Current
Device) protection may be required.
Consult the latest version of BS7671 (IEE wiring regulations).
3.8
Flue options
CAUTION:
in domestic installations
▶ Where a flue system is not going to be accessible, provision must be
made for service and inspection.
▶ Voids containing concealed flues must have at least one inspection
hatch no less than 300mm square.
▶ Flue joints within the void must not be more than 1.5metres from the
edge of the inspection hatch.
▶ Inspection hatches should be located at changes of direction.
▶ If this is not possible, bends should be viewable from both directions.
Groups of appliances with net input in excess of 333kW must comply
with the Clean Air Act by application to the Local Building control
department for flue termination approval. Horizontal terminations above
333kW net input are not permitted (
IGE/UP/10 latest edition for full
guidance.)
Horizontal terminations above 70kW net input must comply with the risk
assessment appendix 9 of IGE/UP/10 as well as the general
requirements of IGE/UP/10.
3.8.1
Air supply and flue gas exhaust in a room sealed installation
A ventilation cover is integrated into the boilers. This cover houses a
number of components, such as the burner and the heat exchanger.
Since this ventilation cover is part of the air supply system, it is vital that
it is always installed correctly.
To ensure optimal operation, the appliances should be connected to a
Worcester horizontal or vertical flue terminal. These terminals have been
developed specifically for Worcester condensing gas boilers and have
been comprehensively tested for trouble free operation when correctly
installed. These boilers are also compatible with third party flues if
required.
Standard horizontal flue pack (
fig. 22) for 50-V2 and 65-V2:
• 1: Flue turret 80/125;
• 2: Horizontal flue terminal 80/125;
• 3: Flue finishing kit.
Standard horizontal flue pack (
fig. 22) for 85-V2 and 100-V2:
• 1: Flue turret 100/150;
• 2: Horizontal flue terminal 100/150;
• 3: Flue finishing kit.
Fig. 22 Standard horizontal flue pack
0010025993-001
300
300
600
25
25
0010025994-001