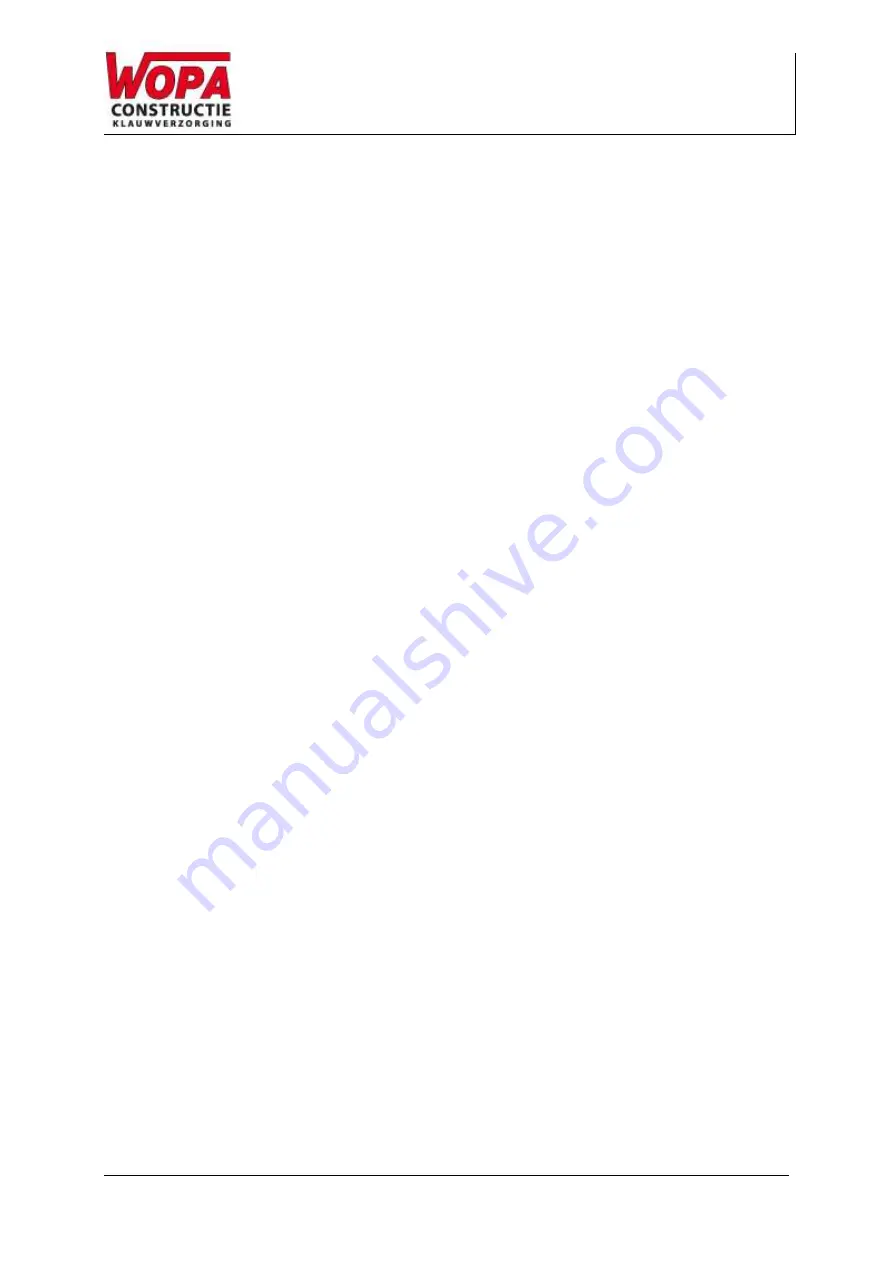
User manual
Treatment crush: SA0042
Version: 10 February 2021 08:02:46
Page 4 of 34
Warranty
The warranty is subject to the following limitations. The warranty period for products supplied by
Wopa is 12 months from the date on the purchase document. This warranty is limited to
manufacturing and material defects and therefore does not cover failures due to any part of the
product being subject to any form of wear. Normal wear that can be expected from the use of this
product is therefore excluded.
1. Wopa’s responsibility is limited to the replacement of defective parts; we do not accept claims
for any other damages or costs.
2. The warranty is voided automatically in case of overdue or poorly performed maintenance.
3. If there is any doubt about maintenance work or if the machine is not working correctly, the
supplier should always be contacted.
4. The warranty does not apply if the defect is the result of improper or negligent use, or of
maintenance performed contrary to the instructions provided in this manual.
5. The warranty is voided if repairs or modifications are made to the product by third parties.
6. Defects arising from damage or accidents caused by external factors are excluded from the
warranty.
7. If we replace parts in accordance with the obligations of this warranty, the replaced parts then
become our property.