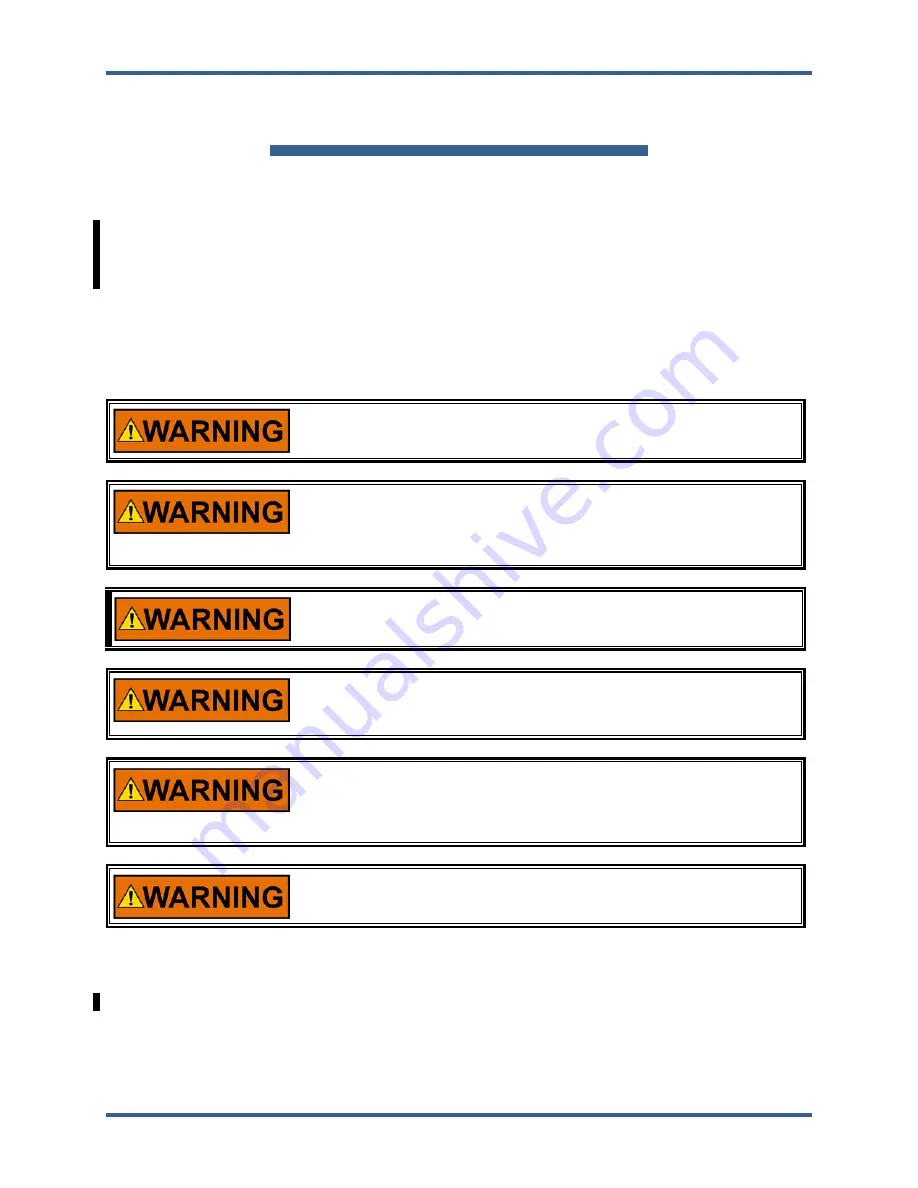
Manual 35076
LESV II
Woodward
46
Chapter 4.
Maintenance and Hardware Replacement
Maintenance
The only maintenance required for the Large Electric Sonic Valve is lubricating the ball screw and bearing
and inspecting the fuel overboard vent port every 12 months. For 2” LESV II, refer to Manual 35134. For
the 3”, 4”, and 6” LESV II, refer to Manual 35103.
With the exception of the SIL2 Flow Sensor, the LESV II is not designed with field-replaceable
components. Contact the turbine manufacturer (primary contact) or Woodward (secondary contact) for
assistance in the event there is a problem requiring service or replacement.
Hardware Replacement
EXPLOSION HAZARD—Substitution of components may impair
suitability for Class I, Division 2, or Zone 2.
To prevent possible serious personal injury, or damage to equipment,
be sure all electric power, hydraulic pressure, and gas pressure have
been removed from the valve and actuator before beginning any
maintenance or repairs.
Lift or handle the valve only by using the eyebolts (See Lifting
Procedures in Chapter 3).
Due to typical noise levels in turbine environments, hearing
protection should be worn when working on or around the Large
Electric Sonic Valve. Noise levels of greater than 90 dB are possible.
The surface of this product can become hot enough or cold enough
to be a hazard. Use protective gear for product handling in these
circumstances. Temperature ratings are included in the specification
section of this manual.
The LESV II contains a mechanical spring under load. Do not
disassemble, as this spring can cause bodily harm.
SIL2 Flow Sensor Replacement
For SIL2 Flow Sensor Replacement for the 2”, 3”, 4”, and 6” LESV II, refer to CMM-03010.
Released
Summary of Contents for Large Electric Sonic Valve II
Page 17: ...Manual 35076 LESV II Woodward 15 Figure 1 3a Outline Drawing 3 Inch LESV II Class 600 Released...
Page 18: ...Manual 35076 LESV II Woodward 16 Figure 1 3b Outline Drawing 3 Inch LESV II Class 600 Released...
Page 19: ...Manual 35076 LESV II Woodward 17 Figure 1 4a Outline Drawing 4 Inch LESV II Class 600 Released...
Page 20: ...Manual 35076 LESV II Woodward 18 Figure 1 4b Outline Drawing 4 Inch LESV II Class 600 Released...
Page 21: ...Manual 35076 LESV II Woodward 19 Figure 1 5a Outline Drawing 6 Inch LESV II Class 600 Released...
Page 22: ...Manual 35076 LESV II Woodward 20 Figure 1 5b Outline Drawing 6 Inch LESV II Class 600 Released...
Page 40: ...Manual 35076 LESV II Woodward 38 Figure 3 11 Cable Motor Resolver 1 Feedback Signal Released...
Page 42: ...Manual 35076 LESV II Woodward 40 Figure 3 13 Cable Motor Resolver 2 Feedback Signal Released...
Page 63: ...Manual 35076 LESV II Woodward 61 Declarations Released...
Page 64: ...Manual 35076 LESV II Woodward 62 Released...