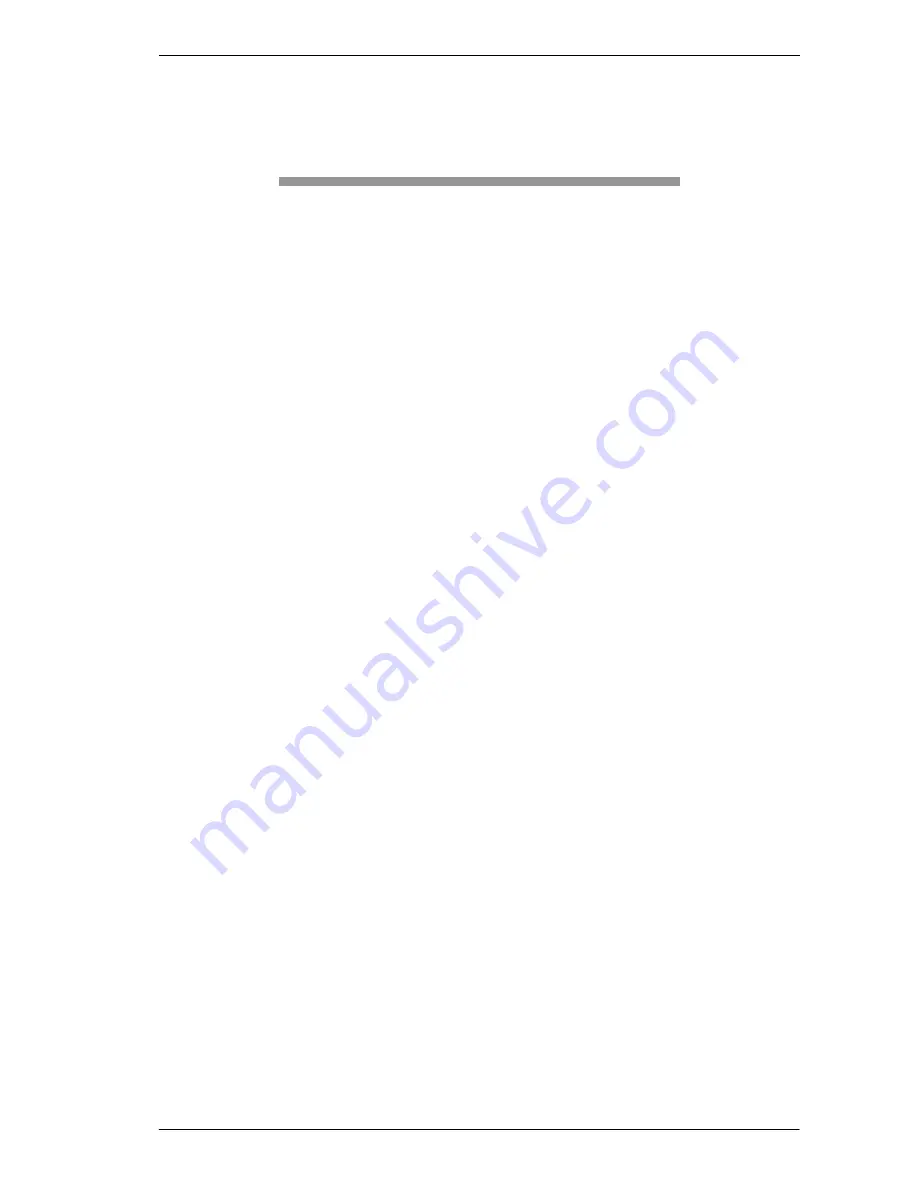
Manual 26004
721DSC for Marine Propulsion Application
Woodward
9
Chapter 4
Description of Operation
General
This section provides an overview of the features and operation of the 721 Digital Speed
Control. In the last part of this manual, the control block diagram and the plant wiring
diagram are shown for reference in the following descriptions.
The 721 Digital Speed Control uses a 16
-
bit microprocessor for all control functions. All
control adjustments are made with a hand
-
held terminal/display (i.e. the hand
-
held
programmer) that communicates with the control via a serial port. The terminal/display is
disconnected from the control when not in service, to provide security against tampering.
The speed sensors contain a special tracking filter designed for reciprocating engines, which
minimizes the effects of flexible coupling torsionals. This provides exceptionally smooth
steady
-
state control and allows the control dynamics to be matched to the engine rather than
detuned to compensate for coupling torsionals. The speed signal itself is usually provided by
a magnetic pickup supplying from 1 to 30 Vrms to the control.
The control also provides 4 to 20 mA terminals for tachometer output, speed reference
output, and rack position output. Relay outputs provide a major alarm, a minor alarm, and
the load transferring indication.
Control Dynamics
The control algorithms used in the 721 control are designed specifically for reciprocating
engine applications.
To provide better transient performance, the control can be operated automatically with two
gain settings depending on engine speed error (speed error is the difference between the
speed setting and the actual engine speed). During steady
-
state operation with a constant
load, the control uses the base gain setting. The control automatically increases gain by an
adjustable ratio when a speed error exceeding an adjustable window occurs so that speed
error is minimized. Operation with base gain is restored once the control senses the return to
steady
-
state speed.
The control can also compensate for non-linear fuel systems and changes in engine dynamics
with load. The control dynamics are mapped as a function of actuator current (actuator
current is proportional to engine load). This provides optimal dynamics and smooth steady
-
state operation for all conditions from no load to full engine load.
The control also provides two complete sets of dynamic adjustments which are selected
depending on the status of the Main Shaft Clutch On input. The two sets of dynamics are
provided for use where engine operating conditions change (e.g., when the engine drives both
the propeller shaft and the generator or when the engine drives only the generator).
Summary of Contents for 721
Page 6: ...721DSC for Marine PropulsionApplication Manual 26004 Woodward 2 ...
Page 8: ...721DSC for Marine PropulsionApplication Manual 26004 Woodward 4 ...
Page 12: ...721DSC for Marine PropulsionApplication Manual 26004 Woodward 8 ...
Page 16: ...721DSC for Marine PropulsionApplication Manual 26004 Woodward 12 ...
Page 38: ...721DSC for Marine PropulsionApplication Manual 26004 Woodward 34 ...
Page 40: ...721DSC for Marine PropulsionApplication Manual 26004 Woodward 36 ...
Page 45: ...Appendix P1 ...
Page 46: ...Appendix P2 ...
Page 47: ...Appendix P3 ...
Page 48: ...Appendix P4 ...
Page 49: ...Appendix P5 ...
Page 50: ...Appendix P6 ...