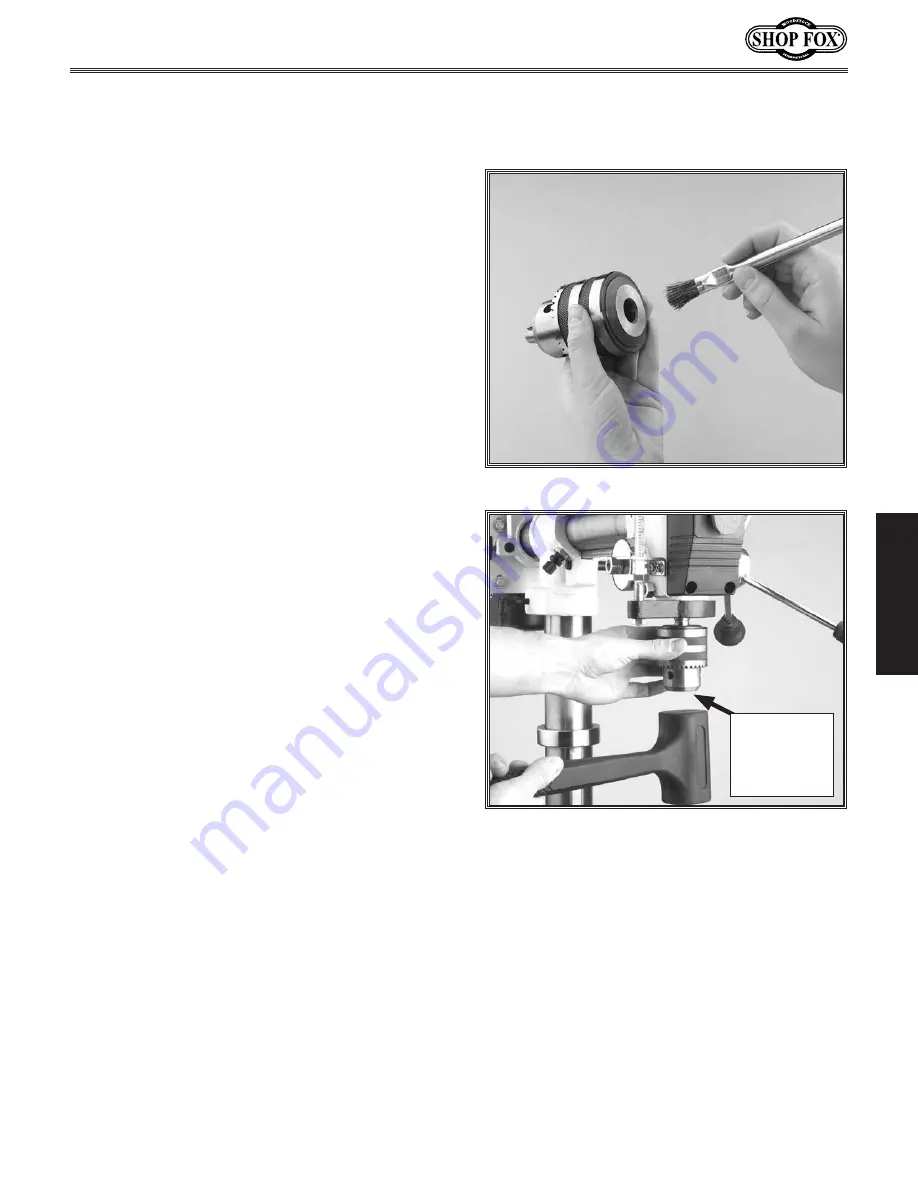
-13-
Drill.Chuck.and.
Spindle
Your keyed drill chuck attaches to the drill
spindle. When properly joined, the JT-33
tapers on the spindle and inside the chuck cre-
ate an almost permanent connection.
To.install.the.drill.chuck,.do.these.steps:
1...
Clean the drill chuck and spindle with min-
eral spirits and follow all safety warnings
on the container (see
Figure.17
).
Note
: Failure to clean the tapered mating
surfaces of the spindle and drill chuck may
result in a loose or wobbly chuck.
2.
Use the provided chuck key to adjust the
jaws of the chuck until they are inside of
the drill chuck body (see
Figure.18
).
3.
Place the drill chuck on the spindle and tap
the chuck onto the spindle with a block of
wood or a dead-blow hammer (see
Figure.
18
).
DO.NOT.
use a metal hammer to seat
the drill chuck onto the spindle!
Figure.18..
Seating chuck into spindle.
Figure.17..
Clean the chuck before installation.
Chuck Jaws
Recessed and
Protected
Inside of
Chuck
ASSEMBLY
Summary of Contents for Shop Fox W1669
Page 25: ...Drill Cutter and Hole Saw Suggested RPM Chart 23 OPERATIONS...
Page 26: ...24 OPERATIONS...
Page 38: ...36 Notes...
Page 39: ...Notes 37...
Page 43: ......
Page 44: ......