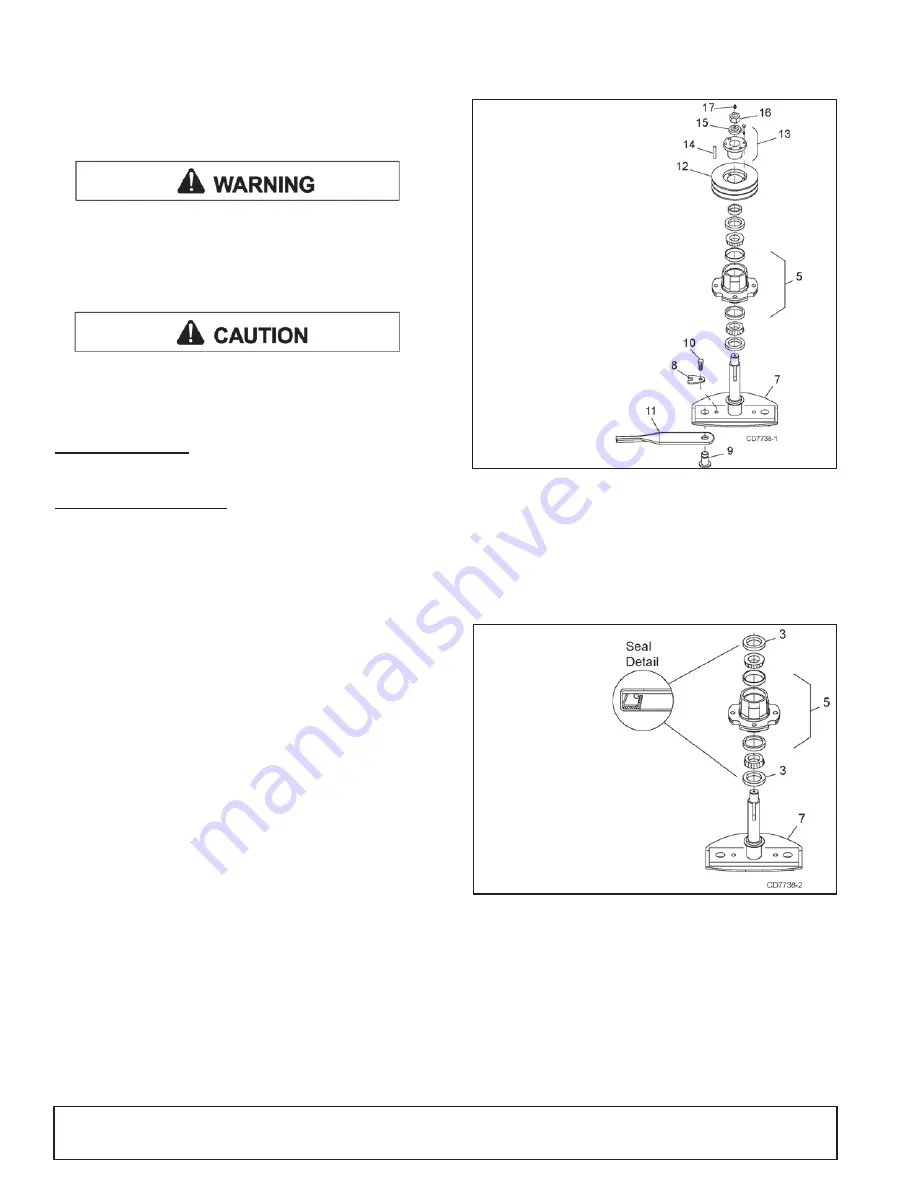
16
Dealer Service
MAN1261 (4/11/2018)
DEALER SERVICE
The information in this section is written for dealer service personnel. The
repair described here requires special skills and tools. If your shop is not prop
-
erly equipped or your mechanics are not properly trained in this type of repair,
you may be time and money ahead to replace complete assemblies.
Before working underneath, read manual instructions, securely
block up, and check stability. Secure blocking prevents equipment from
dropping due to hydraulic leak down, hydraulic system failure, or
mechanical component failure.
Keep all persons away from operator control area while performing
adjustments, service, or maintenance.
Always wear relatively tight and belted clothing to avoid getting
caught in moving parts. Wear sturdy, rough-soled work shoes and pro
-
tective equipment for eyes, hair, hands, hearing, and head; and respirator
or filter mask where appropriate.
BLOCKING METHOD
See "Blocking Method" instructions on page 12.
BLADE SPINDLE SERVICE
Spindle repair requires special skills and tools. If your shop is not properly
equipped or your mechanics are not trained in this type of repair, you may be
time and money ahead to use a new spindle assembly.
For reference, the grease fitting is in the top of the spindle shaft.
Permatex
®
3D Aviation Form-A-Gasket or equivalent is recommended as a
sealant.
Spindle Removal
1.
Remove blade (11) from spindle (7).
2.
Remove belt from pulleys.
3.
Remove jam nut (16) and washer (15) from top of spindle shaft, Figure
15.
4.
Disassemble split taper bushing (13) (located on top of pulley) by
removing the two bolts and key (14).
5.
Insert bolts into the threaded holes of bushing flange.
6.
Tighten bolts alternately to remove split taper bushing.
7.
Remove pulley (12).
8.
Remove bolts that attach spindle to mower frame and remove spindle.
9.
Remove grease fitting (17) from top of shaft.
Figure 15
.
Sheave and Blade Assembly
Spindle Disassembly
1.
Place spindle assembly in press and press shaft down through housing.
2.
Remove seals from housing.
3.
Remove bearing cups from housing by placing a punch in the slots
provided and driving them out. Alternate punch positions from side to
side. Take care to prevent housing damage.
Figure 16
.
Spindle Disassembly
Spindle Assembly
Refer to Figure 17.
Bearing cones and cups are designed to work together. It is important to posi
-
tion them so bearing cone taper mates with cup taper.
1.
Lubricate new cups (6) with a light oil. Place them in spindle housing (5)
so they will mate with bearing cones (4). Cups (6) and cones (4) are a
press fit to minimize wear.
Seat cups (6) securely with a press or place a large drift in the flat lip and
drive them into housing (5) until cup seats against machined shoulder of
housing.
5. Spindle Housing
7. Spindle Shaft and Crossbar
8. Blade Lock
9. Blade Pin
10. 1/2NC x 3/4 Nylock HHCS
11. Blade
12. Sheave
13. Bushing
14. Key
15. 1" Lock Washer
16. 1NC Jam Nut
17. Grease Fitting
3. Seal
5. Spindle Housing
7. Spindle Shaft and Crossbar