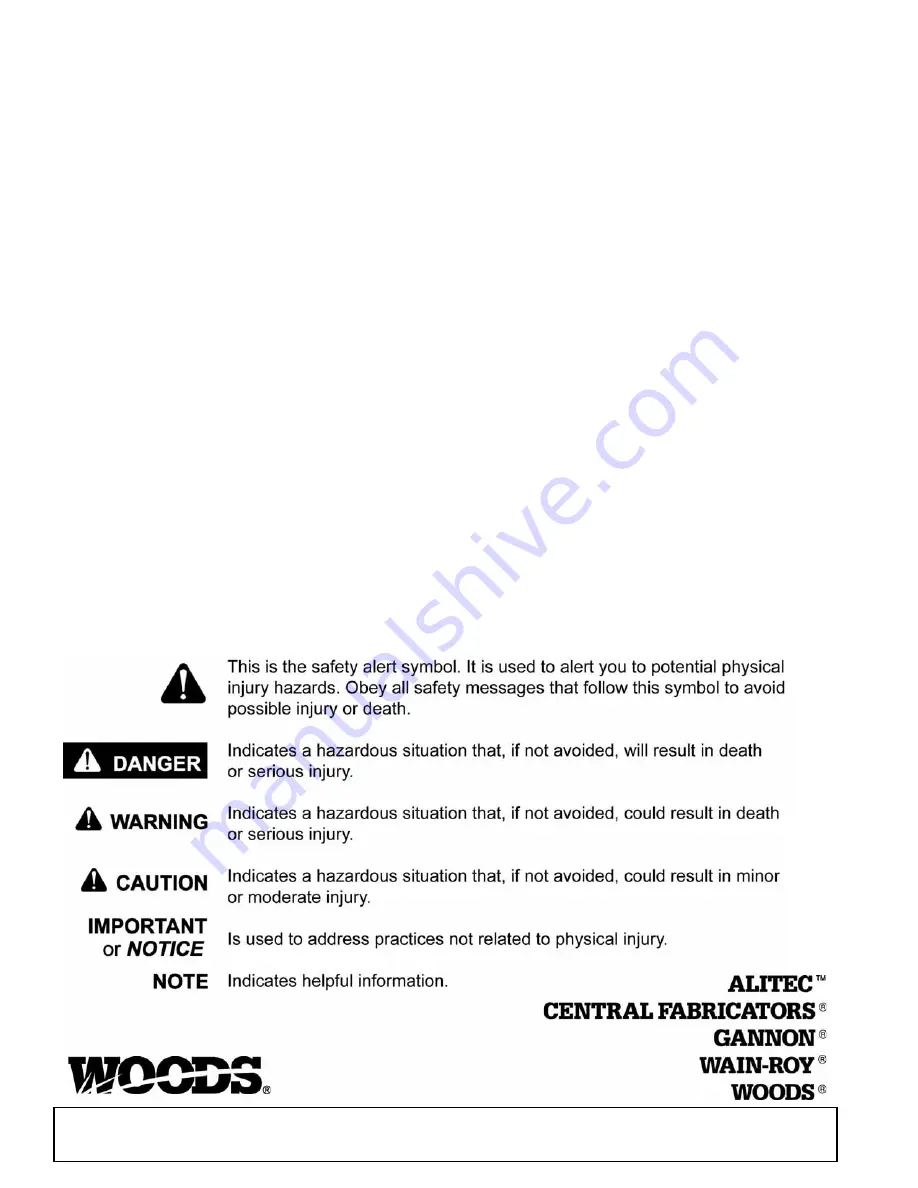
2
Introduction
Gen’l (Rev. 2/25/2016)
TO THE DEALER:
Assembly and proper installation of this product is the responsibility of the Woods
®
dealer. Read manual instructions
and safety rules. Make sure all items on the Dealer’s Pre-Delivery and Delivery Check Lists in the Operator’s Manual
are completed before releasing equipment to the owner.
The dealer must complete the online Product Registration form at the Woods Dealer Website
which certifies that
all Dealer Check List items have been completed. Dealers can register all Woods product at
dealer.WoodsEquipment.com under Product Registration.
Failure to register the product does not diminish customer’s warranty rights.
TO THE OWNER:
Read this manual before operating your Woods equipment. The information presented will prepare you to do a better and
safer job. Keep this manual handy for ready reference. Require all operators to read this manual carefully and become
acquainted with all adjustment and operating procedures before attempting to operate. Replacement manuals can be
obtained from your dealer. To locate your nearest dealer, check the Dealer Locator at www.WoodsEquipment.com, or in
the United States and Canada call 1-800-319-6637.
The equipment you have purchased has been carefully engineered and manufactured to provide dependable and
satisfactory use. Like all mechanical products, it will require cleaning and upkeep. Lubricate the unit as specified.
Observe all safety information in this manual and safety decals on the equipment.
For service, your authorized Woods dealer has trained mechanics, genuine Woods service parts, and the necessary
tools and equipment to handle all your needs.
Use only genuine Woods service parts. Substitute parts will void the warranty and may not meet standards required for
safe and satisfactory operation. Record the model number and serial number of your equipment in the spaces
provided:
Model:
_______________________________
Date of Purchase:
_____________________
Serial Number:
(see Safety Decal section for location) ____________________________________
Provide this information to your dealer to obtain correct repair parts.
Throughout this manual, the term
NOTICE
is used to indicate that failure to observe can cause damage to equipment.
The terms
CAUTION, WARNING,
and
DANGER
are used in conjunction with the Safety-Alert Symbol (a triangle with
an exclamation mark) to indicate the degree of hazard for items of personal safety.
Summary of Contents for BATWING BW13.70
Page 55: ...Common Components 55 MAN1281 4 15 2019 NOTES...
Page 56: ...56 50 Series Parts MAN1281 4 15 2019 CENTER FRAME ASSEMBLY BW20 50 BW20 50Q...
Page 60: ...60 50 Series Parts MAN1281 4 15 2019 WING CENTER GEARBOX ASSEMBLY BW20 50 BW20 50Q...
Page 65: ...50 Series Parts 65 MAN1281 4 15 2019 NOTES...
Page 66: ...66 60 Series Parts MAN1281 4 15 2019 CENTER FRAME ASSEMBLY BW20 60 BW20 60Q...
Page 70: ...70 60 Series Parts MAN1281 4 15 2019 WING CENTER GEARBOX ASSEMBLY BW20 60 BW20 60Q...