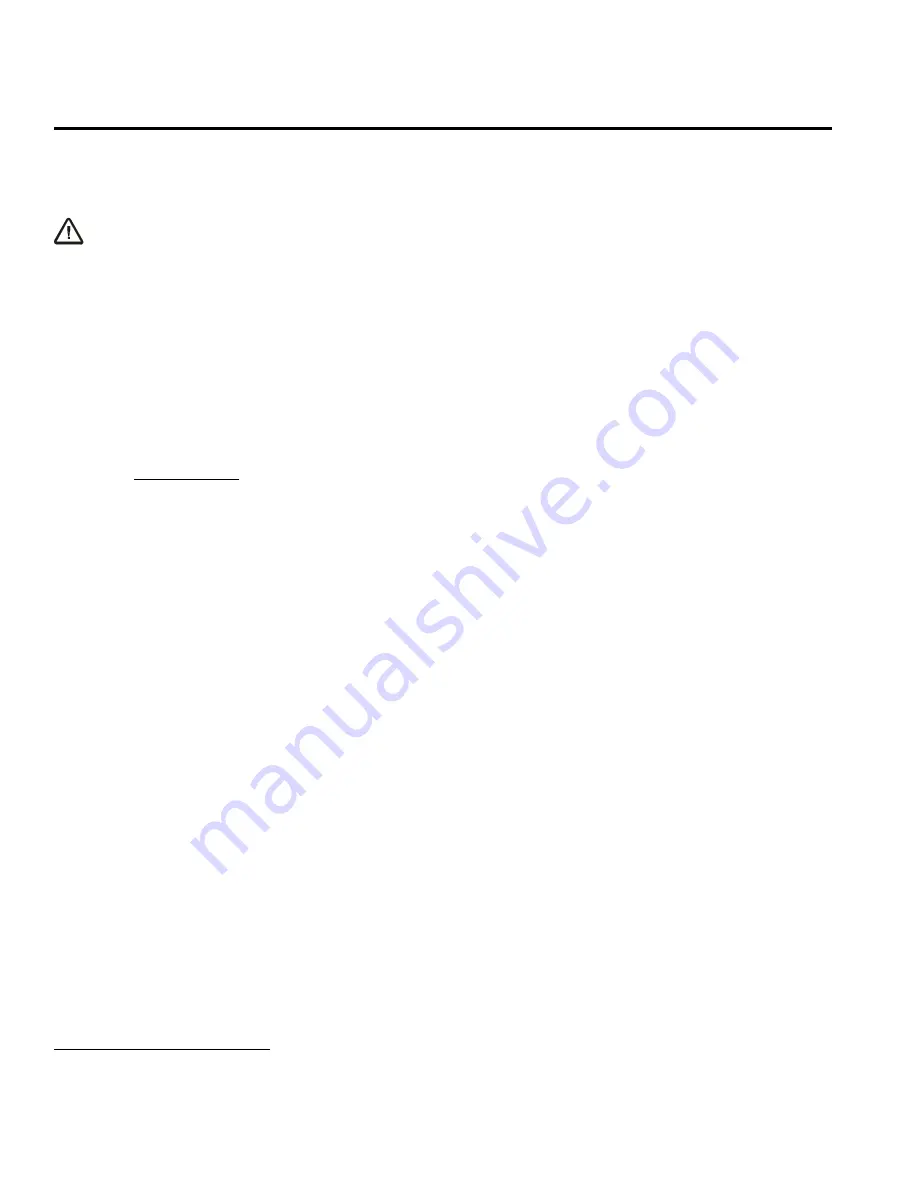
Rev 0.0/7-12
8
MR1611LDCO/DVS: #35048
INTENDED USE
L
OAD
C
HARACTERISTICS
WARNING: This lifter is NOT intended for lifting hazardous materials, such as
explosives or radioactive substances.
The operator must verify that the lifter is intended to handle each load, in accordance with the
following requirements:
• The load must not exceed the maximum allowable weight specified under Load Capacity (see
SPECIFICATIONS).
• The load must be a single piece of nonporous or semiporous material with a flat and relatively
smooth contact surface.
3
To determine whether the load is too porous or rough, perform the
test under Vacuum Level on Other Surfaces (see OPERATION: T
O
A
PPLY THE
P
ADS TO A
L
OAD
).
• The load's contact surface must be suitable for obtaining a friction coefficient of 1 with the
lifter's vacuum pads (see MAINTENANCE: V
ACUUM
P
AD
M
AINTENANCE
: Friction Coefficient), as
verified by a friction test. If necessary, contact Wood's Powr-Grip for help in conducting a
friction test.
• In order to avoid damaging the vacuum pads, the load's surface temperature must not exceed
the allowable Operating Temperatures (see SPECIFICATIONS). However, if such an
application cannot be avoided, Wood's Powr-Grip does offer a heat-resistant rubber
compound and other solutions which may enable you to lift loads with higher surface
temperatures. Contact Wood’s Powr-Grip or an authorized dealer for more information.
• While the
minimum length and width of the load are determined by the Pad Spread (see
SPECIFICATIONS), the
maximum length and width are determined by the allowable
overhang, or the amount of load material that can extend sideways beyond the vacuum pads
without breaking or otherwise being damaged.
The allowable overhang depends on the kind of load material being lifted, the thickness of the
material, and the angle at which it is handled (if any). Since materials such as glass, stone or
sheet metal each have different physical properties, the allowable overhang must be
evaluated separately for each type of load. If necessary, contact Wood’s Powr-Grip or an
authorized dealer for help in determining the recommended overhang in a specific situation.
• 1" [2.5 cm] is the maximum allowable thickness of loads at the maximum weight (see
SPECIFICATIONS: Load Capacity). However, allowable thickness increases as load weight
decreases. If necessary, contact Wood’s Powr-Grip for help in determining the maximum
thickness permitted when handling any specific load.
Note: Vacuum pads can stain or deform load surfaces with light colors or soft coatings. The
operator should test such surfaces for detrimental effects before using the lifter on them.
3
Lifters that feature concave vacuum pads can also attach to some kinds of curved loads. Since curvature affects the lifting
capacity, contact Wood’s Powr-Grip for help in determining the Load Capacity for a particular curved load.
Summary of Contents for MANUAL ROTATOR 2800
Page 2: ......