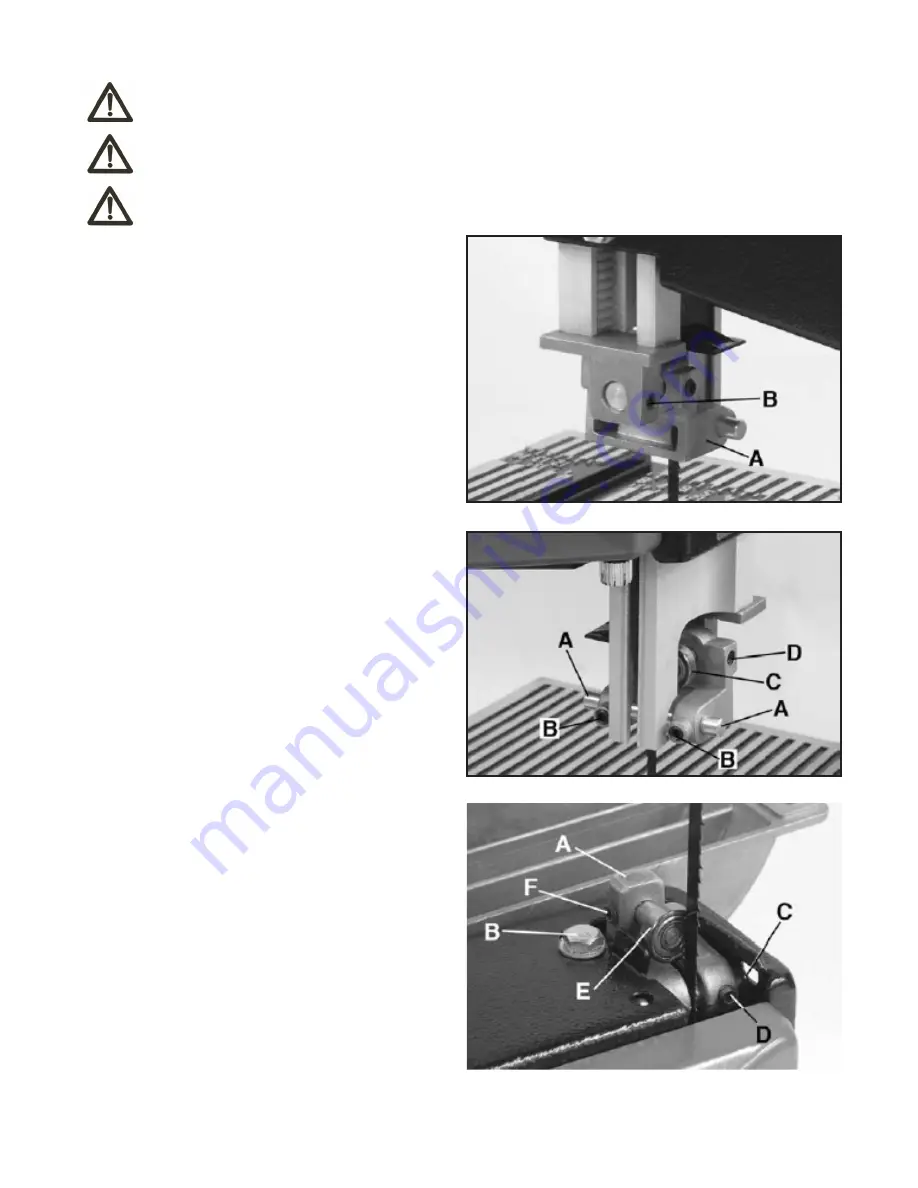
5.7 ADJUSTING UPPER AND LOWER BLADE GUIDES AND BACK-UP BEARINGS
WARNING
WARNING
WARNING
The upper and lower blade guides and back-up bearings support the bandsaw blade during cutting
operations. The adjustment of the guides and bearings should be checked whenever a different blade is
installed.
Allowing the blade teeth to hit the blade guides while the saw is in use will ruin the blade and may
damage the sharpened edge of the teeth. Proper adjustment of the upper and lower blade guide
assemblies will help prevent this from occurring.
The back-up bearing is intended to support the back edge of the blade while cutting. The blade should not
contact the bearings when cutting is stopped.
- Adjust the position of the upper blade guide support (A)
Fig.5.7.1first. Loosen set screw (B) using a hex. key.
- Slide the blade guide support until the front edge of the blade
guides (A) Fig.
5.7.2
are about 1/32” behind the gullet of the
blade (behind the blade teeth). Tighten the set screw.
- Repeat for the lower blade guide support. Adjust the position
of the lower blade guide support (A) Fig.
5.7.3
. Loosen hex. nut
and bolt (B).
- Slide the blade guide support until the front edge of the blade
guides (C) Fig.
5.7.3
are about 1/32” behind the gullet of the
blade (behind the blade teeth). Tighten the hex. nut and bolt.
- Adjust the upper blade guide pins (A) Fig.
5.7.2
. Loosen
the two set screws (B) and press the two guide pins evenly
against the sides of the blade. Make sure that you don’t pinch
the blade. Release the guide pins and rotate the upper wheel,
moving the blade downward. Make sure that one guide pin is
not further away from the blade than the other. Tighten both set
screws (B).
- Repeat on the lower blade guide pins (C) Fig.
5.7.3
using set
screws (D).
- Adjust the upper back-up bearing. Loosen the upper bearing
set screw (D) Fig.
5.7.2
using a hex. key.
- Move the back-up bearing within 1/32” of the blade. Tighten
the upper bearing set screw.
- Repeat on the lower back-up bearing (E) Fig.
5.7.3
using set
screw (F).
FIG.5.7.1
FIG.5.7.2
FIG.5.7.3
-12-