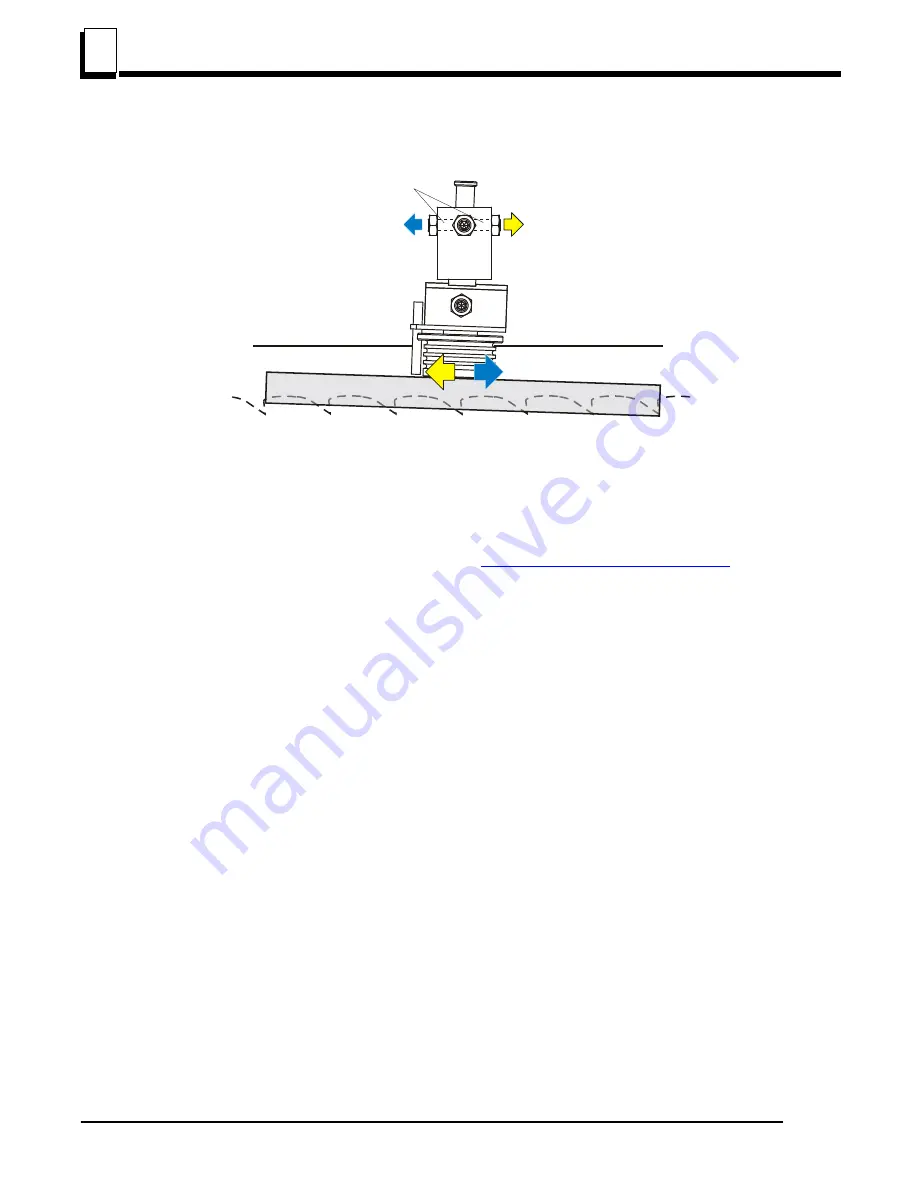
Sawmill Alignment
Blade Guide Flange Spacing
8
8-20
doc072619
Sawmill Alignment
See Figure 8-24.
Loosen the jam nuts on the horizontal tilt adjustment screws. To tilt the roller
left, loosen the right screw and tighten left screw. To tilt the roller right, loosen the left screw and
tighten the right screw. Tighten the jam nuts and recheck the tilt of the blade.
5.
Repeat the above steps for the inner blade guide roller assembly.
NOTE:
Once the blade guides have been adjusted, any cutting variances are
most likely caused by the blade.
See Blade Handbook, Form #600.
Blade Guide Flange Spacing
Each blade guide must be adjusted so the roller flange is the correct distance from the back edge
of the blade. If the flange is too close to or too far from the blade, the sawmill will not cut accu-
rately.
HINT:
When adjusting blade guide spacing, loosen the top set screw and one
side set screw only. This will ensure horizontal and vertical tilt adjustments are
maintained when the adjustment screws are retightened.
FIG. 8-24
3H0802-9
Adjust screws right
to tilt roller left; Adjust
screws left to tilt roller
right
Horizontal Tilt
Adjustment Screws