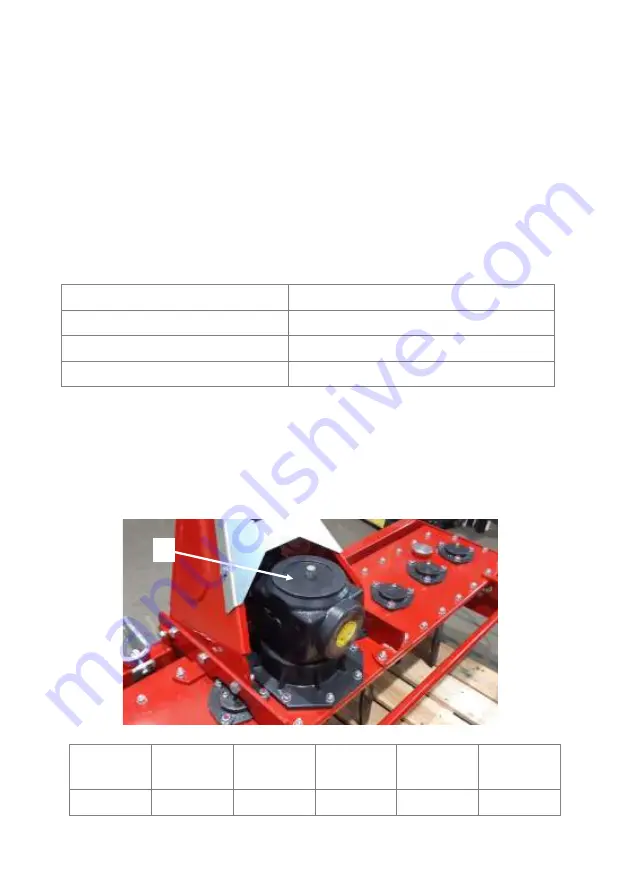
10
Gearbox Oil Change & Check
Before installation/maintenance, ensure both tractor and attachment
are stationary, with the hydraulic lift system in a neutral position and
the ignition key removed.
Do not mix old and new oils together, or mix different oil types. Always
dispose of oils correctly and safely. After use, the attachment should be left
to cool down for 15 minutes before checking oil levels. Ensure the gearbox is
flat/level when checking oil levels. Always follow manufacturer’s instructions
for oils and lubricants.
Gear Oil Grade
80w90 gear oil (or equivalent)
Gearbox Oil Level
Approx. 1.5 litres to level plug
First Oil Change
120 hours use
Oil Change Frequency
250 hours/yearly (whichever is first)
Check gear oil by unscrewing and removing filler plug/breather (1). Use a
dipstick or similar to check the oil level and ideally this should be half full.
The gearbox can be topped up using the filler plug on the top of the unit.
Then replace filler plug/breather (1).
Use an oil pump to remove old oil and any debris when changing oil.
Oil Change
#1
Oil Change
#2
Oil Change
#3
Oil Change
#4
Oil Change
#5
Oil Change
#6
/ /
/ /
/ /
/ /
/ /
/ /
1
Summary of Contents for WPH Series
Page 14: ...14 Parts Diagram 1 ...
Page 18: ...18 Parts Diagram 2 ...
Page 23: ...23 Notes ...
Page 24: ...Published August 2021 ...