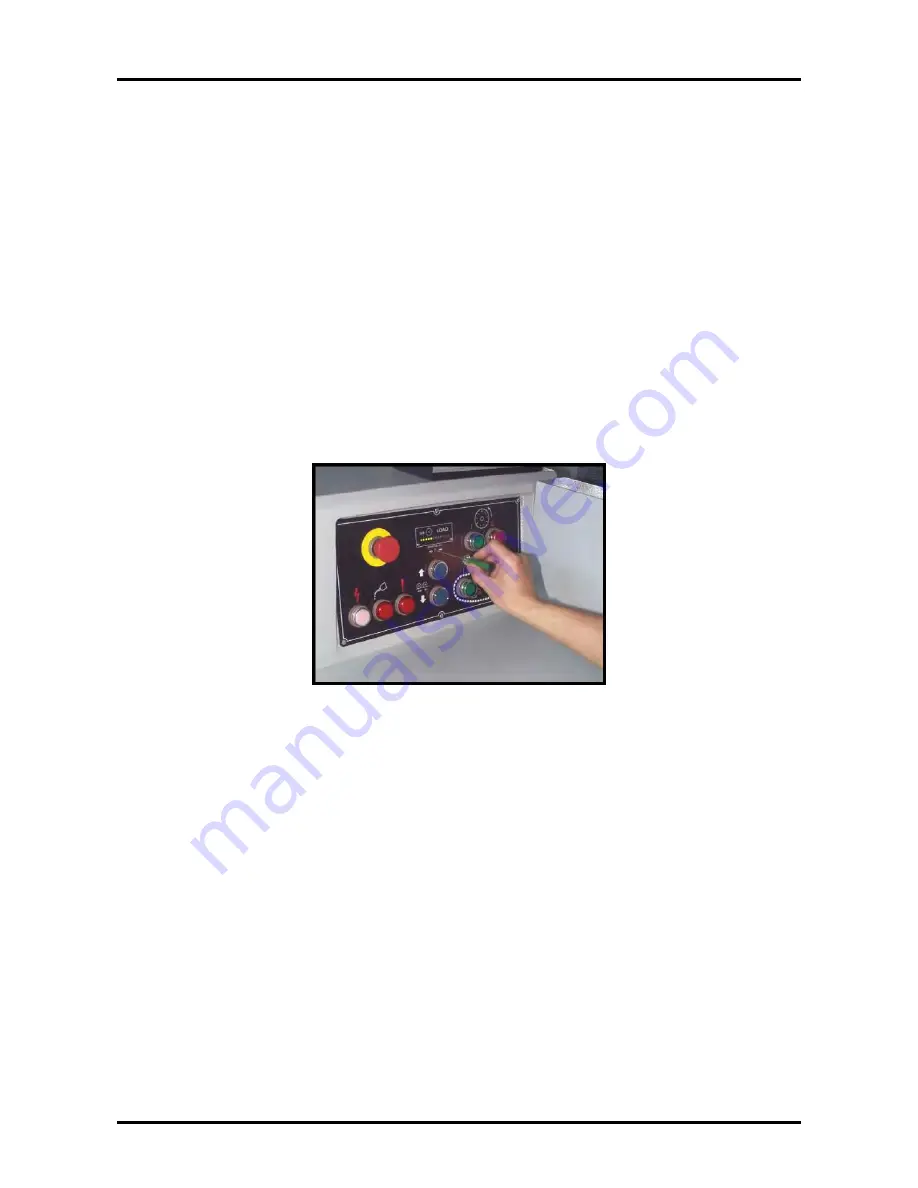
M
ULTIMAX 300
Chapter 3: OPERATION
26
◎
According to the quantity and the sharpness of saw blades, feed speed and the
smooth demand on the ripping surface, the operator can adjust the sensitivity
micro-adjustment button of motor-load to a proper position (to increase the
sensitivity by turning it in a clockwise direction; to reduce the sensitivity by
turning it in a counter-clockwise direction; the range of mirco-adjustment from the
direction of eight clock to four clock). If the sensitivity is adjusted to be too sharp,
the feed chain will often stop easily; if it is adjusted to be too dull, this device can
not perform the protection function of the feed chain auto-slowdown. After used
the machine for a period of time, if the indication lamp is often in the postion of
close to yellow lamp or red lamp, it means the workload is overloaded. There are 3
ways to solve:
1.
The saw blades are worn, must replace with new saw blades.
2.
Slow down the feed speed.
3.
Reduce the quantity of saw blades.
Summary of Contents for MULTIMAX 300
Page 2: ......
Page 6: ......
Page 18: ...MULTIMAX 300 Chapter 1 INTRODUCTION 12 Machine size ...
Page 52: ......
Page 53: ...A A 4 8 3 2 16 1 14 12 10 5 7 10 13 17 18 15 9 11 2 2 4 2 PAGE BM31 03 0 ...
Page 54: ...PAGE BM31 05 0 BM31 05 0 BM31 05 0 BM31 05 0 2 10 9 4 8 2 6 5 11 1 3 2 4 3 3 7 12 2 ...
Page 55: ...8 4 1 7 5 6 3 12 10 9 11 2 2 2 2 2 3 4 3 PAGE BM31 10 0 ...
Page 56: ...PAGE AM31 010 0 52 212 106 106 4 3 1 2 5 ...
Page 57: ...4 3 7 11 6 10 5 1 2 8 9 3 2 PAGE AM31 020 0 ...
Page 58: ...5 12 20 3 4 1 2 17 15 14 9 6 7 8 13 19 16 10 11 21 18 2 2 4 7 4 2 3 2 PAGE AM30C 121 0 ...
Page 60: ...PAGE AM31 100 0 1 6 7 8 9 10 2 3 4 5 13 12 11 5 5 5 5 2 4 4 4 4 ...
Page 61: ...PAGE AM31 121 0 16 6 15 13 10 7 1 20 17 3 2 9 8 4 19 5 11 18 12 14 3 4 4 4 4 3 2 3 2 ...
Page 62: ...PAGE AM12 100 0 1 2 3 4 5 2 2 2 ...
Page 64: ...PAGE BM30C 231 0 BM30C 231 0 BM30C 231 0 BM30C 231 0 2 4 1 2 3 3 ...
Page 66: ...8 7 4 3 5 6 1 4 7 3 3 2 PAGE BM31 26 0 ...
Page 73: ...PAGE AM30C 261 0 4 2 1 8 3 10 6 7 4 4 5 9 5 4 11 2 ...