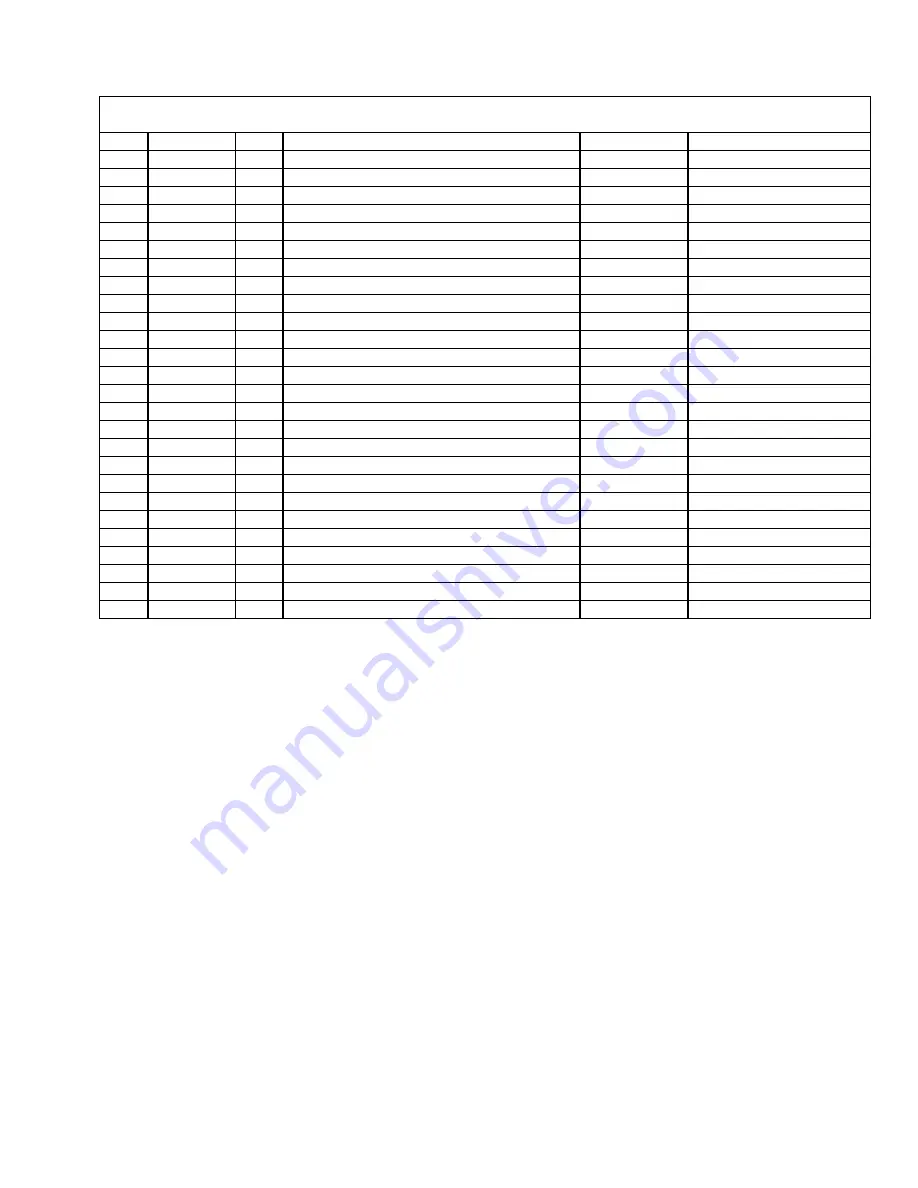
HANDLE GROUP
LB1500 980101 03/08/03
5-8
REF
PART NO.
QTY
DESCRIPTION
SERIAL NO.
FROM
NOTES:
1
70686
2
SCR, M6 X 45 SHCS BLK
2
51326
1
LOCK, SAFETY HANDLE
3
73990
2
SPRING, EXT. .5OD X 3.5L
4
78437
1
TUBE, GRIP HANDLE
5
36196
2
GRIP, POLISHER HANDLE
6
51327
2
LEVER, SWITCH
7
57274
4
NUT, M6 X 1
8
500194
1
LABEL, WARNING
9
41363
1
HOUSING, POLISHER HANDLE FRONT
10
70689
2
SCR, M4.8 X 10 HHTF TYPE B
11
57275
3
NUT, M10 X 1.5 HEX NYLOCK PLTD
12
87086
3
WASHER, M10 X 30 PLTD
13
78544
1
TUBE ASM, HANDLE EXTND
14
67430
1
ROD, HANDLE ADJUSTMENT
15
87202
1
WASHER, BEARING (HANDLE ADJ)
16
66334
1
PIN, PIVOT HANDLE ADJUSTMENT
17
14344
1
BAR, HANDLE ADJUSTMENT
18
140393
1
BLOCK, HANDLE MOUNT
19
14434
2
BUMPER, BURNISHER HANDLE
20
70692
1
SCR, MID X 75 HHCS PLTD
21
41366
1
HOUSING, POLISHER HANDLE FRONT
22
70687
2
SCR, M6 X 50 SHCS BLK
23
38316
1
HANDLE, BRNSHR EXTND
24
730021
1
SPACER, POLISHER HANDLE
25
23206
1
CORDSET, 14/3 X 52” SJT BLK
26
730012
1
STRAIN RELIEF, 14/3 STRAIGHT
27
70701
1
SCR, M10 X 1.5 X 90 HHCS PLTD
Summary of Contents for LB1500
Page 14: ...MOTOR GROUP LB1500 980101 03 08 03 5 1 2 1 3 ...
Page 16: ...FRAME GROUP LB1500 980101 03 08 03 5 3 1 13 7 8 10 15 12 11 6 9 5 4 14 7 3 2 ...
Page 18: ...DRIVE PAD LOCK GROUP LB1500 980101 03 08 03 5 5 ...
Page 22: ...WIRING GROUP LB1500 980101 11 15 03 5 9 11 8 9 6 2 1 3 4 10 9 8 5 7 12 PRIOR TO SN ...