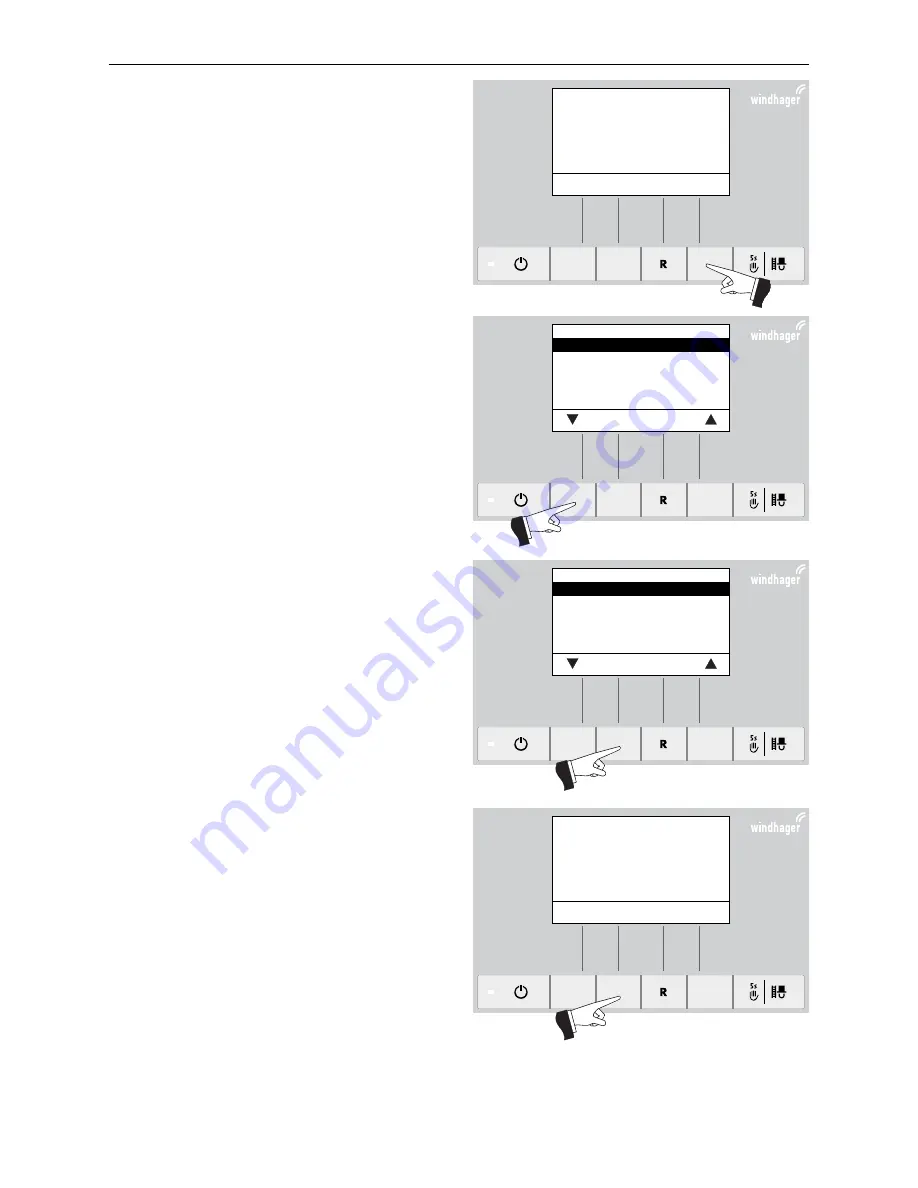
37
4.
For the Service Technician
Service level
Pressing the
Menu
button (Fig. 96) shows the „Opera-
tor level“, „Service level“, „Information level“ and „MES
Module
1
“ in the display – Fig. 97.
Use the
arrow
buttons to select the “Service level” sub-
menu – Fig. 97.
Press and hold the
Choose
button for 5 seconds (Fig. 98).
The display shows „Service level only for trained service
personnel“ – Fig. 99.
1 only displayed when an MESplus control is present and this has been adjusted by a trained service technician in the basic settings
Press for 5
seconds
Press for 5
seconds
Fig. 96
Boiler temperature
(Operating phases)
Info
Menu
42
°C
Fig. 97
Operator level
Service level
Information level
MES Module
1
Choose
Back
Fig. 98
Operator level
Service level
Information level
MES Module
1
Choose
Back
Fig. 99
Service level only
for trained service personnel
5s