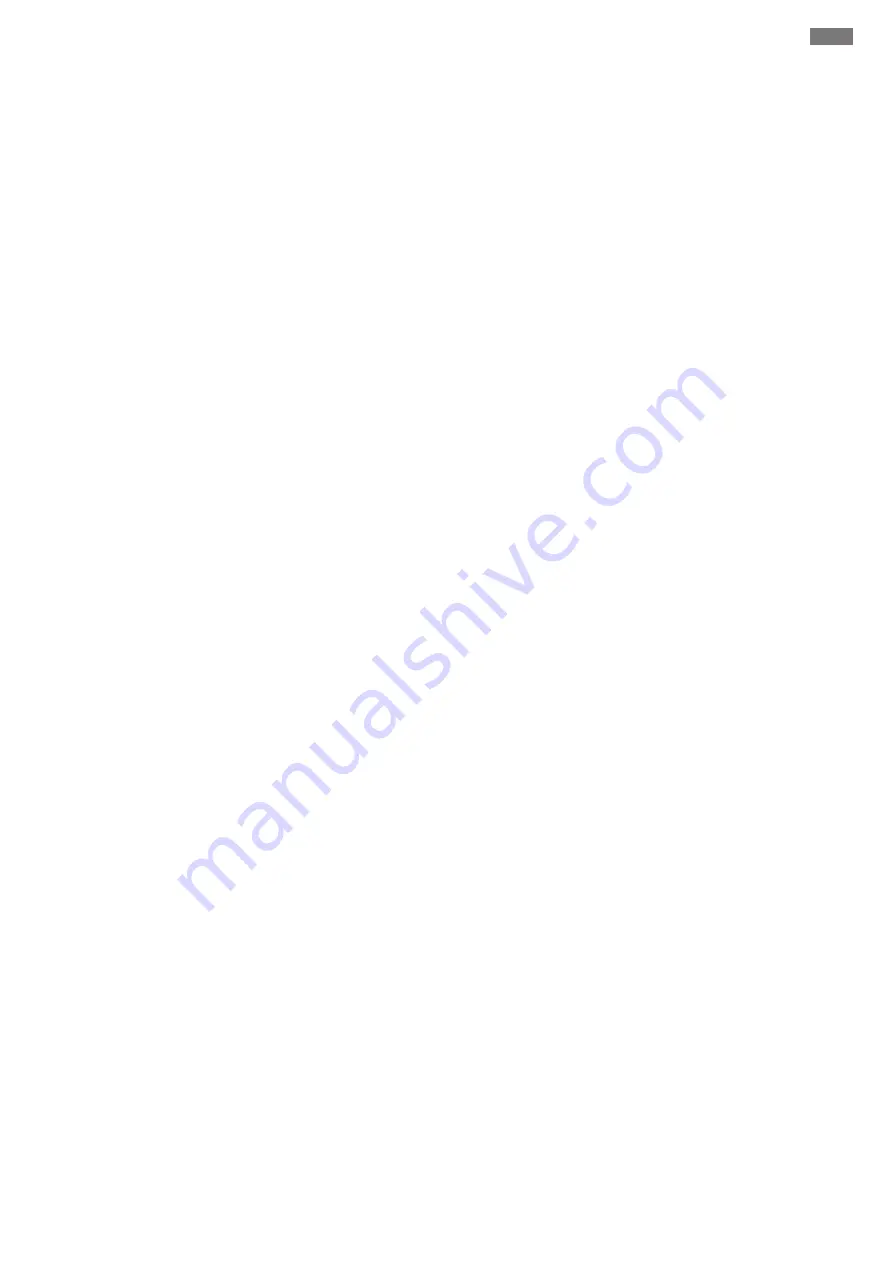
Safety
en
Installation and operating instructions Wilo-Vardo WEEDLESS-F
9
ƒ
Clean and disinfect the product thoroughly.
ƒ
Make sure that there is no risk of explosion when carrying out any work with elec-
trical devices.
ƒ
Only use properly functioning hoisting gear.
ƒ
Keep away from the hoisting gear’s swivel range when hoisting the product.
ƒ
Toxic or asphyxiating gases may build up when working in closed rooms or buildings.
Ensure there is sufficient ventilation and observe protective measures according to
work regulations (examples):
–
Measure the gas concentration before entering.
–
Carry a gas detector with you.
–
etc.
2.9
During operation
ƒ
The work area in which the device is used is not a recreational area. No persons are
allowed in the work area during operation.
ƒ
Wear protective equipment in accordance with the work regulations notice.
ƒ
The operator must immediately report any faults or irregularities to their line man-
ager.
ƒ
If hazardous defects occur, the operator must immediately deactivate the device.
Hazardous defects include:
–
Malfunction of safety and monitoring devices
–
Damage to housing parts
–
Damage to electrical equipment
ƒ
The propeller must not bump into fixtures or walls in the operating space. Observe
defined clearances to fixtures and basin walls in accordance with consulting docu-
ments.
ƒ
If the water level fluctuates significantly, ensure the required water immersion using
level monitoring.
ƒ
Under normal operating conditions, the sound-pressure level of the product is below
85 dB(A). However, the actual sound-pressure level depends on several factors:
–
Installation type
–
Utilisation
–
Immersion depth
2.10
Maintenance tasks
ƒ
Risk of injury through crushing and hot operating fluid. Wear the following protect-
ive equipment:
–
Sealed safety goggles
–
Protective gloves
–
Safety shoes
ƒ
Only carry out the maintenance tasks described in these installation and operating
instructions.
ƒ
Carry out maintenance tasks in accordance with the manufacturer’s instructions.
ƒ
Use only original parts from the manufacturer for maintenance and repairs. Use of
parts other than original parts releases the manufacturer from any liability.
ƒ
Do not carry out maintenance on the product during operation. Disconnect the
device from the mains and secure it against being switched on again without au-
thorisation.
ƒ
Collect any drips of fluid and operating fluid immediately and dispose of them ac-
cording to locally applicable guidelines.
Changing gear oil in the drive unit
The oil change procedure uses compressed air. Observe the following points:
ƒ
Allow the gear to cool down before opening the gear oil chamber.
ƒ
Only insert compressed air in the gear’s fill hole.
ƒ
To avoid inhaling oil mist, limit the compressed air to 0.8 bar (11.5 psi).
2.11
Operating fluid
The drive unit’s gear is filled with gear oil at the factory. Consult the manufacturer’s in-
structions for information on change intervals and disposal of operating fluid.
The interior of the hub is covered with water-resistant grease. Dispose of operating
fluid in accordance with local guidelines.
2.12
Operator responsibilities
ƒ
Provide installation and operating instructions in a language which the personnel can
understand.
ƒ
Make sure that the personnel is relevantly trained for the specified work.
ƒ
Provide the necessary protective equipment and make sure that personnel wear it.
ƒ
Safety and information signs mounted on the device must always be legible.
ƒ
Train the personnel on how the system operates.