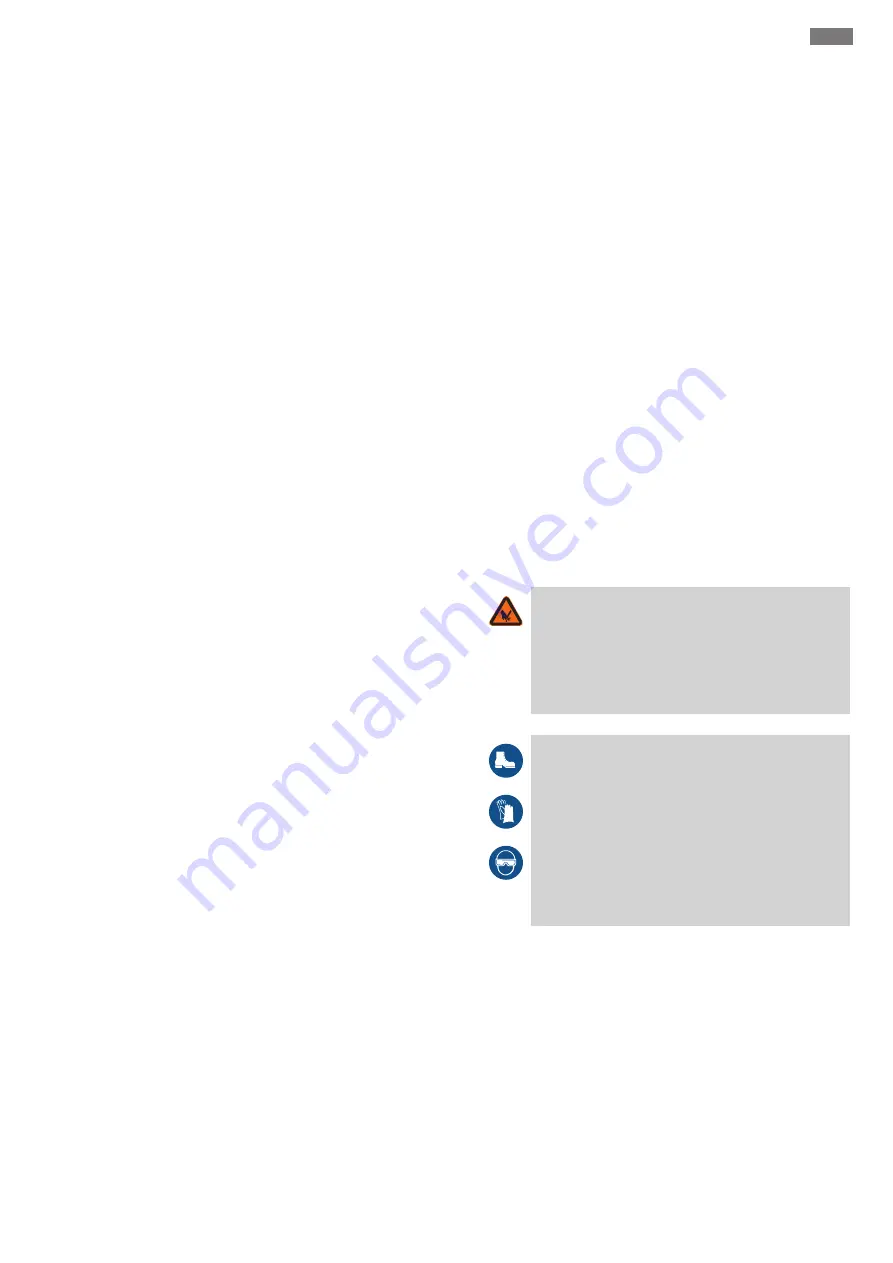
Maintenance and repair
en
Installation and operating instructions Wilo-Rexa UNI
23
ƒ
Maintenance tasks: The technician must be familiar with the
use of operating fluids and their disposal. In addition, the tech-
nician must have basic knowledge of mechanical engineering.
9.2
Operator responsibilities
ƒ
Provide the necessary protective equipment and make sure
that the personnel wears it.
ƒ
Collect operating fluids in suitable tanks and dispose of prop-
erly.
ƒ
Dispose of protective clothing used in accordance with regula-
tions.
ƒ
Use only original parts of the manufacturer. Use of parts other
than the original parts releases the manufacturer from any li-
ability.
ƒ
Collect any leakage of fluid and operating fluid immediately
and dispose of it according to the locally applicable guidelines.
ƒ
Provide the tools required.
ƒ
If flammable solvents and cleaning agents are used, open
flames, naked lights and smoking are prohibited.
9.3
Operating fluid
9.3.1
Oil types
Medicinal white oil is filled into the sealing chamber ex-factory.
The following oil types are recommended when changing the oil:
ƒ
Aral Autin PL*
ƒ
Shell ONDINA 919
ƒ
Esso MARCOL 52* or 82*
ƒ
BP WHITEMORE WOM 14*
ƒ
Texaco Pharmaceutical 30* or 40*
All oil types marked with “*” are approved for use with foods in
accordance with “USDA-H1”.
9.3.2
Filling quantities
The filling quantities depend on the pump type:
ƒ
Rexa UNI V05...: 600 ml (20 US.fl.oz.)
ƒ
Rexa UNI V06...: 1000 ml (34 US.fl.oz.)
9.4
Maintenance intervals
To ensure reliable operation, maintenance tasks must be carried
out regularly. Depending on the real ambient temperatures, main-
tenance intervals different from those mentioned in the contract
can be defined! If strong vibrations occur during operation, the
pump and the installation must be checked regardless of the
defined maintenance intervals.
9.4.1
Maintenance intervals for normal conditions
5 years or 1500 operating hours
ƒ
Visual inspection of the power supply cable
ƒ
Visual inspection of accessories
ƒ
Visual inspection of the housing for wear
ƒ
Function test of monitoring devices
ƒ
Oil change
10 years or 5000 operating hours
ƒ
General overhaul
9.4.2
Maintenance intervals for use in sewage lifting units
When the pump is used in sewage lifting units inside buildings or
on plots of land, carry out maintenance intervals and measures in
accordance with
DIN EN 12056‑4
!
9.4.3
Maintenance intervals for harsh conditions
Under harsh operating conditions, specified maintenance intervals
must be shortened if required. Harsh operating conditions include:
ƒ
Fluids with long-fibre components
ƒ
Turbulent inlet (e.g. due to air intake, cavitation)
ƒ
Strongly corroding or abrasive fluids
ƒ
Heavily gas generating fluids
ƒ
Operation at an unfavourable duty point
ƒ
Pressure surges
When using pumps under hard conditions, it is recommended to
sign a maintenance contract. Contact customer service.
9.5
Maintenance measures
WARNING
Sharp edges on the impeller and suction port!
Sharp edges can form on the impeller and suction
port. There is danger of limbs being severed! Protect-
ive gloves must be worn to protect from cuts.
WARNING
Hand, foot or eye injuries due to the absence
of protective equipment!
Danger of (serious) injuries during work. Wear the fol-
lowing protective equipment:
• Safety gloves for protection against cuts
• Safety shoes
• Closed safety goggles
The following pre-requisites must be fulfilled prior to starting
maintenance measures:
ƒ
Pump cooled down to the ambient temperature.
ƒ
Pump cleaned thoroughly and disinfected (if required).
9.5.1
Recommended maintenance measures
Regular inspection of power consumption and the operating
voltage in all three phases is recommended for smooth operation.
In normal operation, these values remain constant. Slight fluctu-
ations depend on the characteristics of the fluid. Power consump-
tion can provide an early indication of damage or malfunctions in