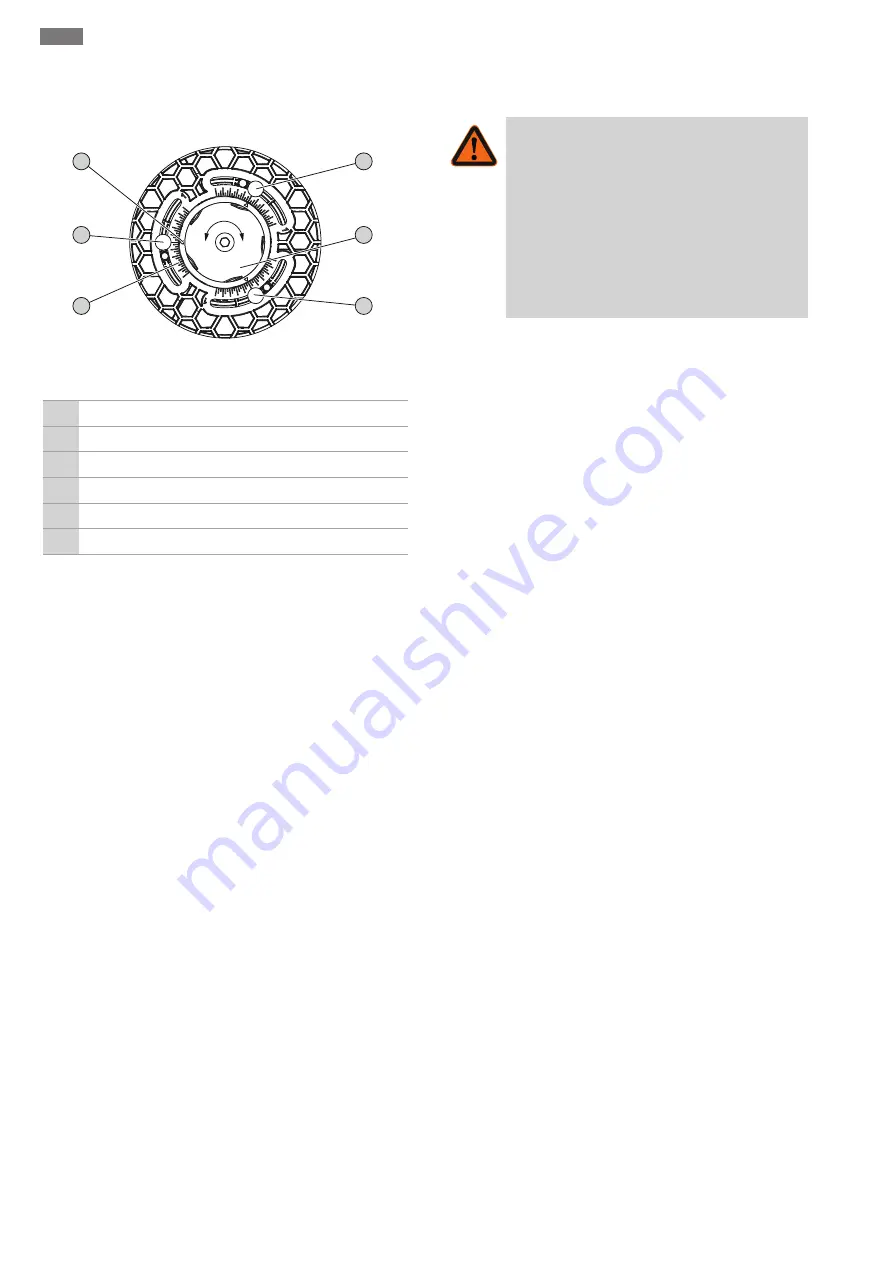
en
Faults, causes and remedies
40
WILO SE 2021-07
the impeller and suction port can be adjusted to compensate for
impeller wear.
+
-
1
4
2
1
1
3
Fig. 8:
Adjusting the impeller clearance (strainer removed)
1
Safety screws for fixing the clearance adjustment
2
Clearance adjustment
3
Dial
4
Pointer (▲)
+
Increase clearance
-
Decrease clearance
‡
Strainer removed. See “Cleaning the strainer [
}
37]”
‡
Baseplate cleaned. The dial and pointer are discernible.
1. Loosen the safety screws until the clearance adjustment
can be turned.
NOTICE! Do not completely unscrew
the screws!
2. Turn the clearance adjustment anti-clockwise (-) until
the counterplate rests against the impeller.
3. Increase the clearance by 3 division marks: Turn the
clearance adjustment clockwise (+). Observe the pointer
when setting!
4. Tighten the safety screws.
Max. tightening torque:
4 Nm (3 ft·lb)!
▶ Impeller clearance corrected. Refit the strainer.
9.5.7
General overhaul
During the general overhaul, the motor bearings, shaft sealings,
O-rings and connection cables are checked for wear and damage.
Damaged components are replaced with original parts. This en-
sures correct operation.
The general overhaul is performed by the manufacturer or an au-
thorised service centre.
10
Faults, causes and remedies
WARNING
Risk of injury from rotating components!
No persons are allowed to be present in the work-
ing area of the pump. There is a risk of injury!
• Demarcate and cordon off the working area.
• If there are no persons in the working area, ac-
tivate the pump.
• If persons enter the working area, switch off
the pump immediately.
Fault: Pump does not start
1. Electricity supply interrupted or short-circuit/earth fault
in the cable or motor winding.
⇒ Have the connection and motor checked by a quali-
fied electrician and replace if necessary.
2. Tripping of fuses, of the motor protection switch or the
monitoring equipment
⇒ Have the connection and the monitoring equip-
ment checked by a qualified electrician and change
it if necessary.
⇒ Have the motor protection switches and fuses in-
stalled and adjusted according to the technical spe-
cifications by a qualified electrician and reset mon-
itoring equipment.
⇒ Check the impeller to make sure that it runs
smoothly, clean the hydraulics if necessary.
Fault: Pump starts up, motor protection trips after short
period
1. Motor protection switch set incorrectly.
⇒ Have the adjustment of the trigger checked and
corrected by a qualified electrician.
2. Increased power consumption due to major voltage
drop.
⇒ Have the voltage of individual phases checked by a
qualified electrician. Contact the electricity distri-
bution network.
3. There are only two phases at the connection.
⇒ Have the connection checked and corrected by a
qualified electrician.
4. Excessive differences in voltage between the phases.
⇒ Have the voltage of individual phases checked by a
qualified electrician. Contact the electricity distri-
bution network.
5. Incorrect direction of rotation.
⇒ Have the connection corrected by a qualified elec-
trician.