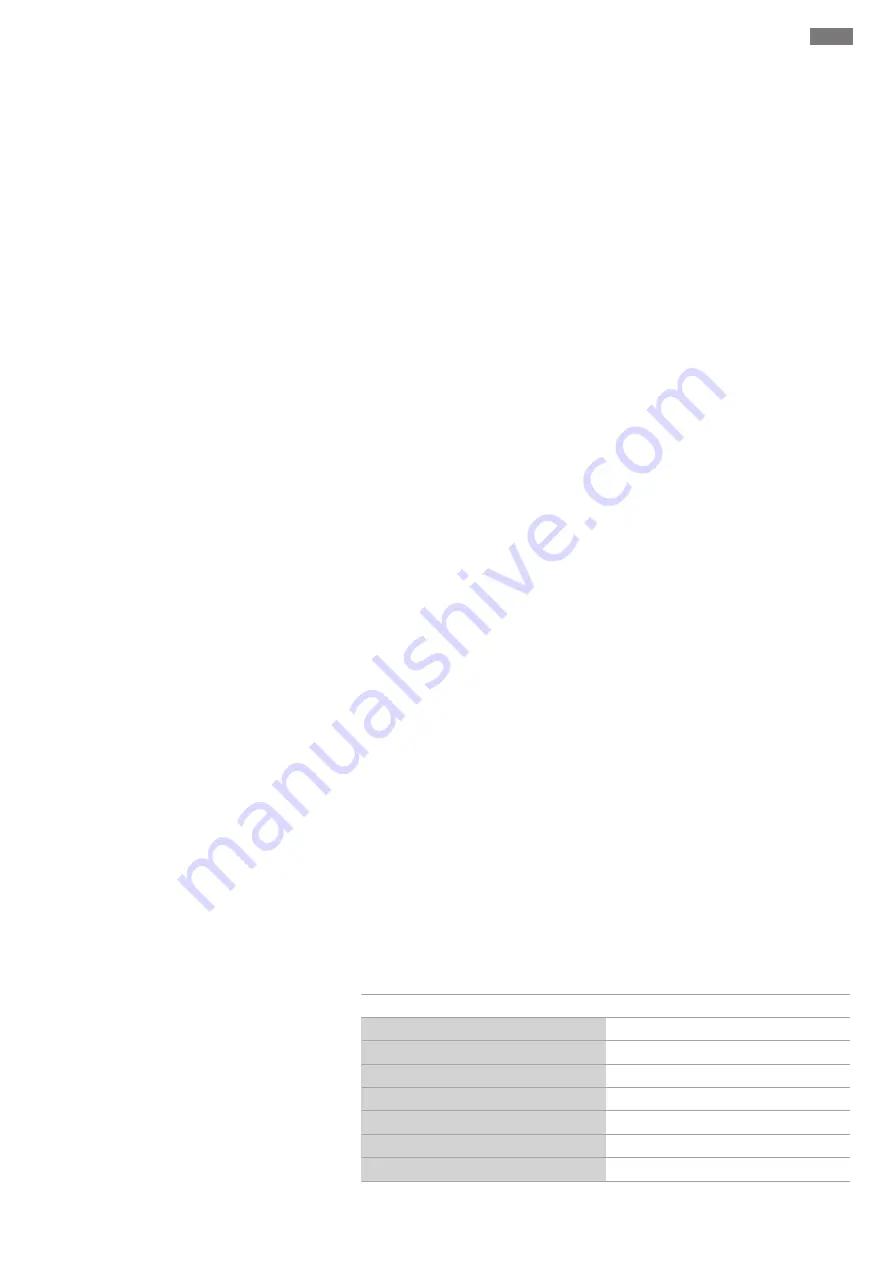
Product description
en
Installation and operating instructions Wilo-Padus PRO
11
4.1.2
Motor
The surface-cooled IE3 motor is available in alternating current or three-phase current
versions. Cooling is provided using sheath flow cooling. Waste heat is transferred dir-
ectly to the fluid via the motor housing. The motor can be used for continuous duty
both immersed and non-immersed.
On AC motors, the start capacitor and operating capacitor is installed in a separate
switchgear. The switchgear is integrated in the connection cable. The connection cable
is available in the following versions:
ƒ
Bare cable end
ƒ
With plug and fitted float switch
4.1.3
Seal
The seal for the fluid and the motor compartment is made via two mechanical seals. The
sealing chamber between the mechanical seals is filled with medical white oil.
4.1.4
Material
ƒ
Pump housing: EN-AC-Al NBR-70
ƒ
Impeller: 1.4470
ƒ
Suction strainer: 1.4301
ƒ
Cooling shroud: 1.4301
ƒ
Motor housing: EN-AC-AlSi10Mg
ƒ
Shaft: 1.4404
ƒ
Seal on the motor side: SiC/SiC
ƒ
Seal on the fluid side: SiC/SiC
ƒ
Static seal: NBR
4.1.5
Fitted accessories
Version “A” of the pump is equipped with a plug and float switch. Depending on the fill
level, it is possible to switch the pump on and off automatically using the float switch.
The plug is designed for use in commercially available shock-proof or CEE sockets and
is
not
overflow-proof.
4.2
Monitoring devices
The thermal motor monitoring protects the motor winding from overheating. A tem-
perature limiter with a bimetallic strip is fitted as standard. The motor monitoring is de-
signed as follows:
ƒ
Version with bare cable end: The thermal motor monitoring is self-switching. This
means that the motor is switched off if it overheats and will be automatically
switched on again when it has cooled down.
ƒ
Version “A”: The thermal motor monitoring is fitted to the plug on the motor protec-
tion relay.
4.3
Operating modes
Operating mode S1: Continuous duty
The pump can operate continuously at the rated load without exceeding the permiss-
ible temperature.
“Slurping operation” operating mode
Slurping operation facilitates the pumping of very small amounts of fluid.
CAU-
TION! Never allow the machine to dry run! Non-compliance can lead to irreparable
damage!
4.4
Operation with frequency con-
verter
Operation on the frequency converter is not permitted.
4.5
Operation in an explosive atmo-
sphere
Operation in an explosive atmosphere is not permitted.
4.6
Technical data
General
Date of manufacture [MFY]
See rating plate
Mains connection [U/f]
See rating plate
Power consumption [P
1
]
See rating plate
Rated power [P
2
]
See rating plate
Max. delivery head [H]
See rating plate
Max. volume flow [Q]
See rating plate
Activation type [AT]
See rating plate
Summary of Contents for Padus PRO
Page 2: ......