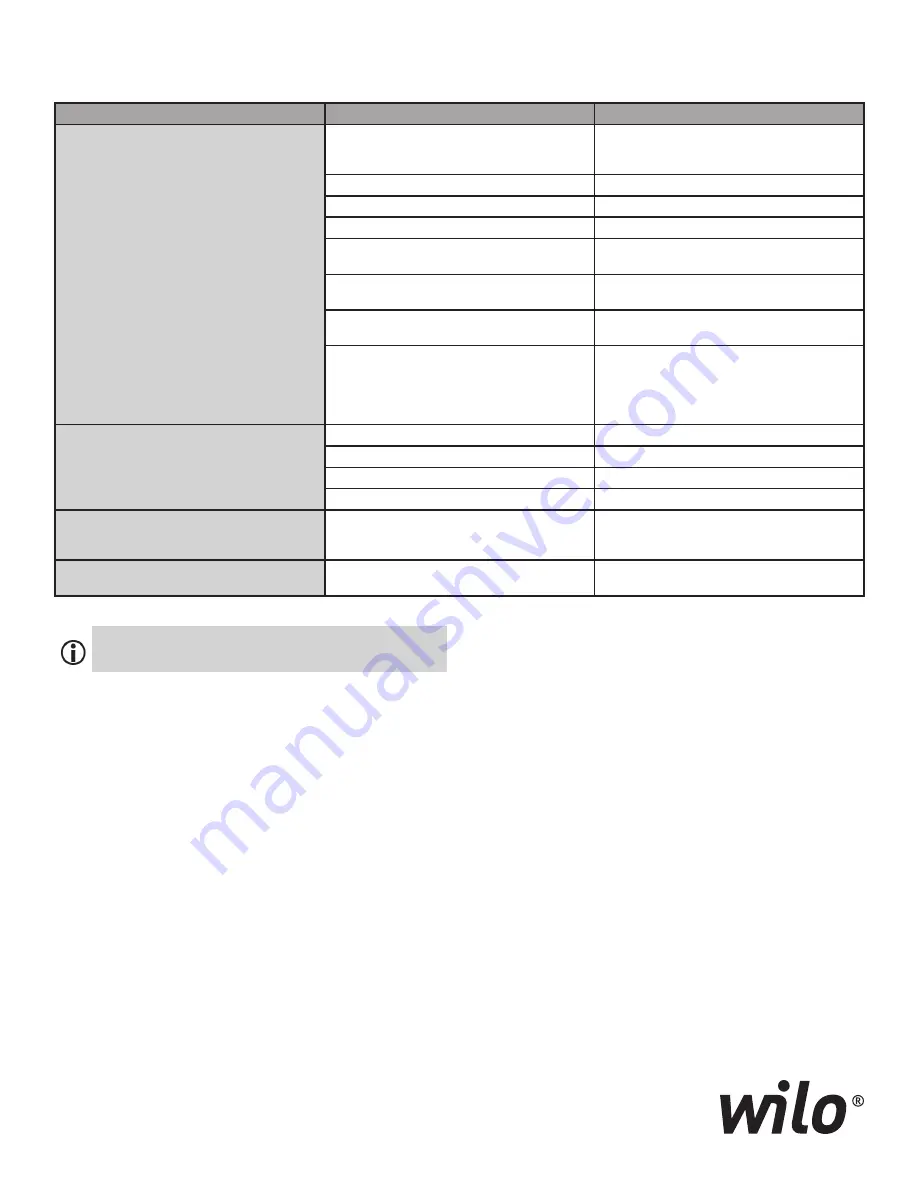
WILO USA LLC
+1 888-945-6872
www.wilo-usa.com
Wilo Canada Inc.
+1 866-945-6236
www.wilo-canada.com
Wilo Mexico
+52 442 167 00 32
www.wilo-mexico.com
Faults
Possible Cause
Remedy
Pump does not start or fails to run
Pump Seized
Switch off power supply, take off pump head,
remove obstruction; if motor blocked, overhaul/
exchange motor/ pump head
Loose Terminals
Tighten all terminals
Blown fuses/breakers
Check fuses, replace/reset as necessary
Faulty motor
Call service
Tripped overload relay (excessive amp draw)
Throttle hydraulic flow rate down to nominal on
discharge side of pump
Incorrectly set trip relay (heaters)
Reset thermal overloads to full load current value
specified on name plate
Thermal overload is influenced by excessive ambi
-
ent temperature
Prevent overloads caused by high ambient tem-
peratures
Tripped PTC relay
Check motor and fan cover for dirt/dust accu-
mulation and clean if necessary; Check ambient
temperature and if necessary, ensure an ambient
temperature
£ 105 °F [40 °C] by forced ventilation.
Pump runs at reduced capacity
Incorrect rotation
Check direction of rotation, reverse if necessary
Discharge valve throttled too far
Slowly open isolating valve
Speed too low
Adjust incorrect terminal bridging (Y in lieu D)
Air in suction pipe
Check and correct all possible suction leaks
Insufficient inlet pressure
Raise inlet pressure, ensure minimum required inlet
pressure at suction port, check and if necessary
clean suction-side isolating valve and strainer
Pump makes noise
Faulty motor bearings
Arrange for pump to be inspected and, if necessary,
to be repaired by Wilo or other authorized service.
12.
Troubleshooting Guide
Note:
If you cannot fix the problem, contact service
engineer or a Wilo branch office.