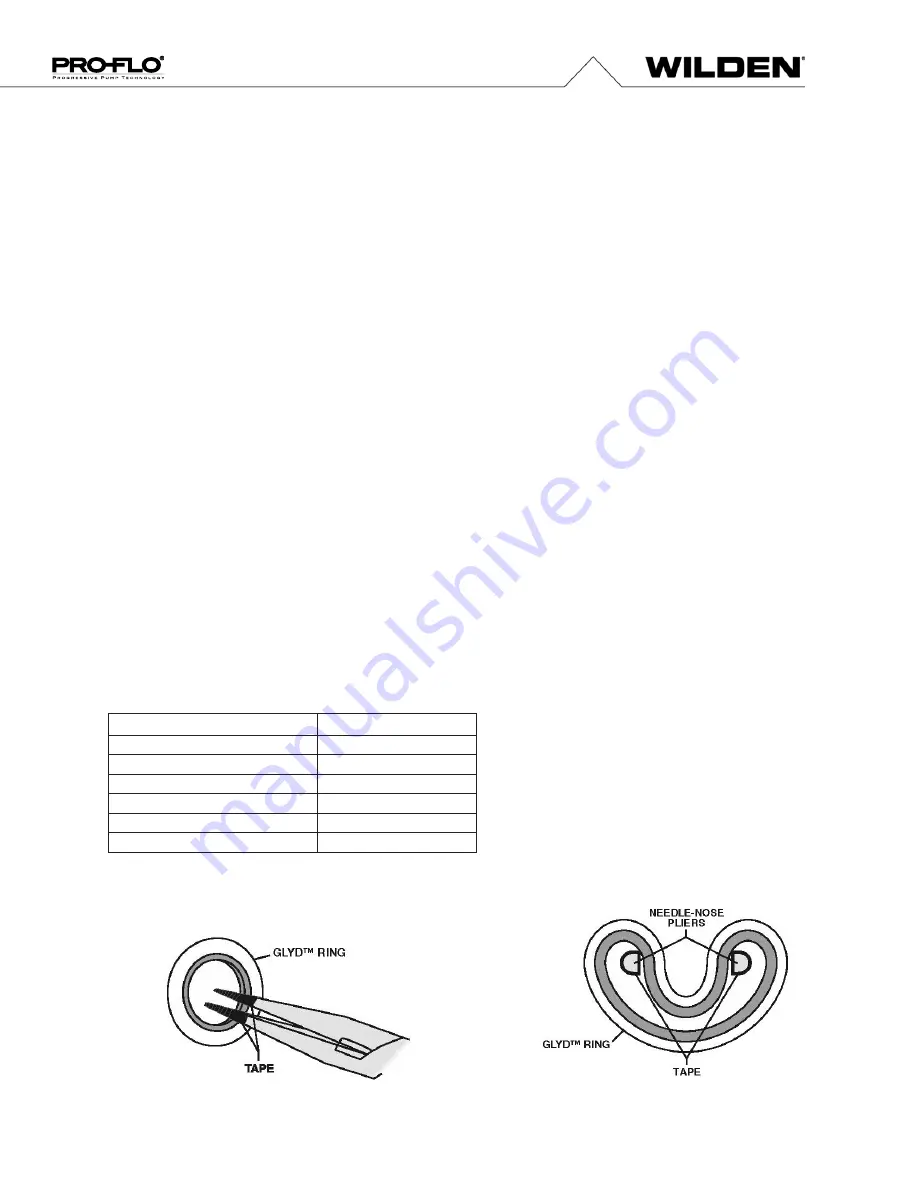
WIL-11160-E-09
Wilden
®
18
Disassembly / Reassembly
Reassembly Hints & Tips
Upon performing applicable maintenance to the air distribution
system, the pump can now be reassembled. Please refer to the
disassembly instructions for photos and parts placement. To
reassemble the pump, follow the disassembly instructions in
reverse order. The air distribution system needs to be assembled
first, then the diaphragms and finally the wetted path. Please find
the applicable torque specifications on this page.
The following tips will assist in the assembly process.
•
Lubricate air valve bore, center section shaft and pilot spool
bore with NLGI grade 2 white EP grease or equivalent.
•
Clean the inside of the center section shaft bushing to ensure
no damage is done to new glyd ring seals.
•
A small amount of NLGI grade 2 white EP grease can be
applied to the muffler and air valve gaskets to locate gaskets
during assembly.
•
Make sure that the exhaust port on the muffler plate is centered
between the two exhaust ports on the center section.
•
Stainless bolts should be lubed to reduce the possibility of
seizing during tightening.
GLYD™ RING INSTALLATION:
PRE-INSTALLATION
•
Once all of the old seals have been removed, the inside of the
bushing should be cleaned to ensure no debris is left that may
cause premature damage to the new seals.
PRO-FLO
®
MAXIMUM TORQUE SPECIFICATIONS
Description of Part
Torque
Air Valve
8.5 N•m (75 in
-lb))
Outer Piston
136 N•m (100 ft
-lb)
Air Chamber/Center Block
4.6 N•m (55 ft
-lb))
Tee Section/Elbow
3.4 N•m (32 ft
-lb)
Elbow/Liquid Chamber
3.4 N•m
(32 ft-lb)
Liquid Chamber/Air Chamber
3.4 N•m (32 ft
-lb)
Figure A
NSTALLATION
The following tools can be used to aid in the installation of the
new seals:
•
Needle-Nose Pliers
•
Phillips Screwdriver
•
Electrical Tape
•
Wrap electrical tape around each leg of the needle-nose
pliers (heat shrink tubing may also be used). This is done to
prevent damaging the inside surface of the new seal.
•
With a new seal in hand, place the two legs of the needle-
nose pliers inside the seal ring. (See Figure A.)
•
Open the pliers as wide as the seal diameter will allow, then
with two fingers pull down on the top portion of the seal to
form a kidney bean shape. (See Figure B.)
•
Lightly clamp the pliers together to hold the seal into the
kidney shape. Be sure to pull the seal into as tight of a
kidney shape as possible, this will allow the seal to travel
down the bushing bore easier.
•
With the seal clamped in the pliers, insert the seal into the
bushing bore and position the bottom of the seal into the
correct groove. Once the bottom of the seal is seated in the
groove, release the clamp pressure on the pliers. This will
allow the seal to partially snap back to its original shape.
•
After the pliers are removed, you will notice a slight bump in
the seal shape. Before the seal can be properly resized, the
bump in the seal should be removed as much as possible.
This can be done with either the Phillips screwdriver or your
finger. With either the side of the screwdriver or your finger,
apply light pressure to the peak of the bump. This pressure
will cause the bump to be almost completely eliminated.
•
Lubricate the edge of the shaft with NLGI grade 2 white
EP grease.
•
Slowly insert the center shaft with a rotating motion. This will
complete the resizing of the seal.
•
Perform these steps for the remaining seal.
Figure B
Summary of Contents for PRO-FLO P1500
Page 23: ...WIL 11160 E 09 Wilden 23 Notes...