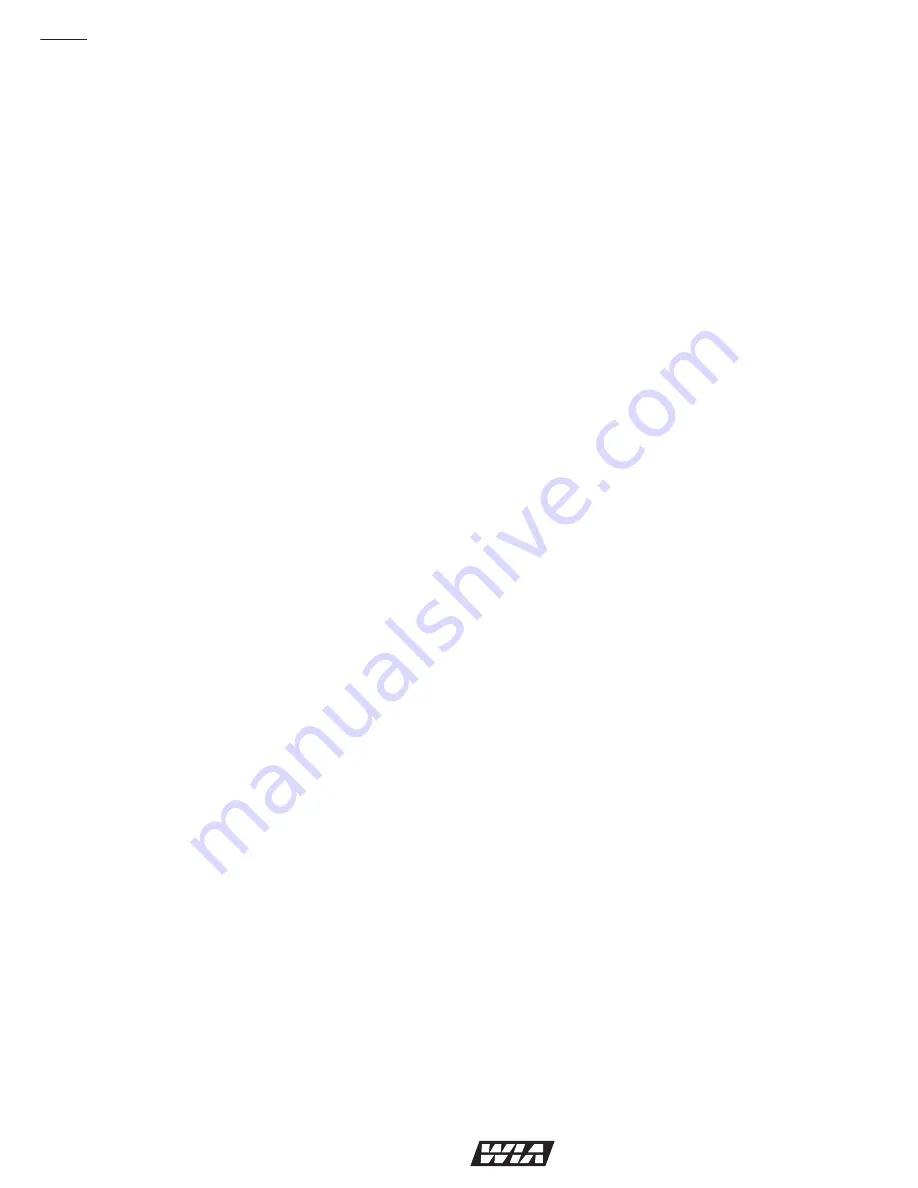
10
Operators Manual
Quality
•
Reliability
•
Performance
6 Normal Welding Sequence
Weld Start
Closing the welding gun switch initiates this
sequence of events:
• The gas valve is energised and gas flow
commences and continues for any pre-gas
time set
• The power source contactor function
is initiated. Welding voltage is applied
between the work piece and the
consumable wire
• The wire drive motor is energised
• The wire touches the work piece, and the
arc is established.
Weld End
Releasing the gun switch initiates this
sequence of events:
• The wire drive motor is de-energised, and
is dynamically braked to a stop
• After a short pre-set period, known as
the ‘burn-back’ time, the power source
contactor function is released. This period
ensures that the consumable wire does
not ‘freeze’ in the weld pool
• At the completion of any post-gas time
set, the gas valve is de-energised and the
flow of shielding gas ceases.
7 Basic Welding Information
Choice of Shielding Gas
The choice of shielding gas is largely
determined by the consumable wire to
be used. Many proprietary shielding gas
mixtures are available.
The recommended shielding gases for use
with the Weldmatic 396 are:
• Mild Steel
Argon +
5 to 25% Carbon Dioxide;
100% CO
2
• Aluminium Argon;
• Stainless Steel Argon + 1 to 2% Oxygen.
Consult your gas supplier if more specific
information is required.
Shielding Gas Flow Rate
In G.M.A. welding, one function of the
shielding gas is to protect the molten weld
pool from the effects of oxygen in the
atmosphere. Without this protection the
weld deposit becomes ‘honeycombed’ in
appearance, an effect which is described as
weld porosity.
In draft-free conditions the gas flow rate
required to give adequate protection is
typically 10-12 litres/min. In situations
where drafts cannot be avoided, it may
be necessary to increase this rate up to
20 litres/min, and/or to provide screening of
the work area.
Weld porosity can also be caused by air
entering the gas stream through a damaged
hose, loose gas connection, or from
restriction in the nozzle, such as from excess
build-up of spatter.
When welding aluminium, particular care
must be taken with all aspects of shielding
gas delivery and workpiece preparation in
order to avoid weld porosity.