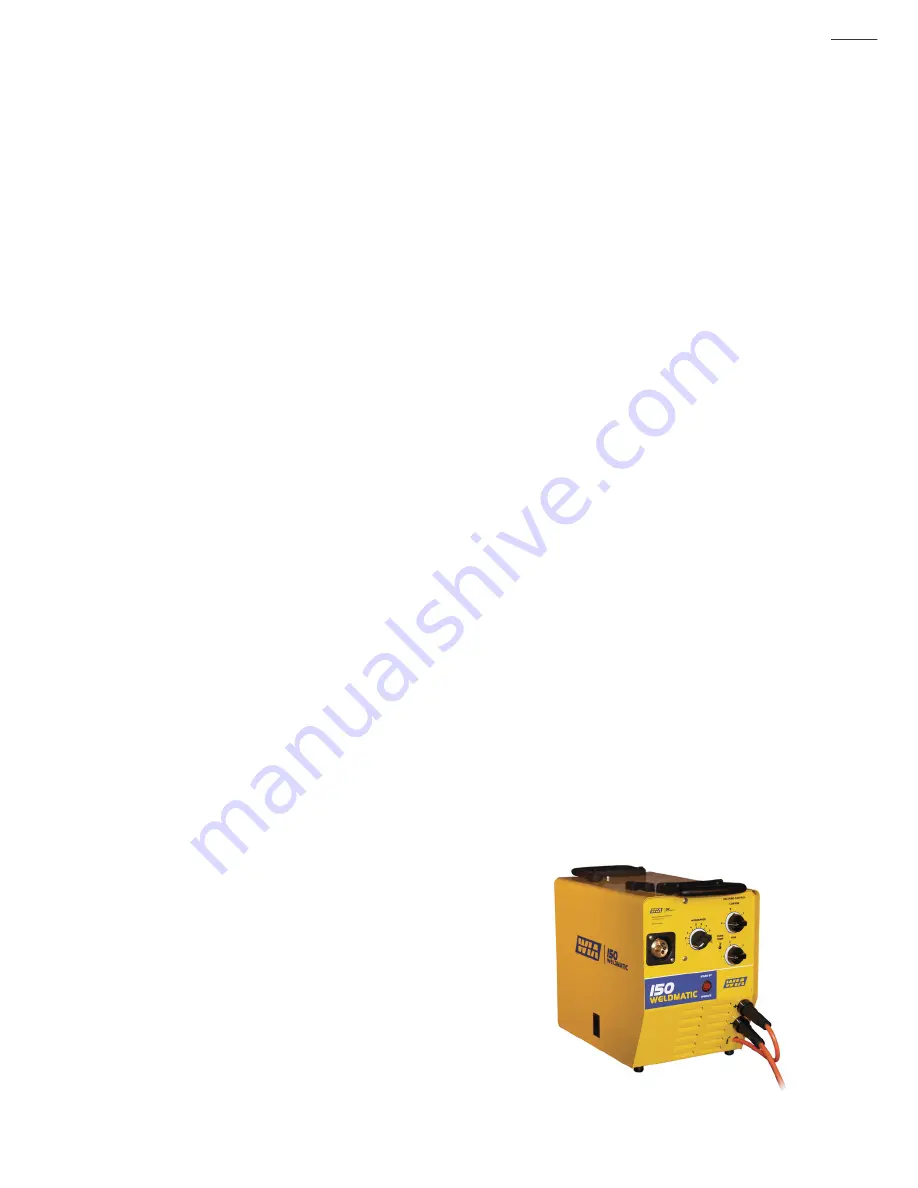
Weldmatic 150
Model No CP121, Iss B 07/08
1
Quality
•
Reliability
•
Performance
Contents
Section General Information
Page
Safe Practices
2
1
Introduction
5
2
Receiving
5
3
Specifications
6
4
Controls
7
5
Installation
8
6
Normal Welding Sequence
10
7
Basic Welding Information
10
8
General Maintenance
15
9
External Trouble Shooting
16
10
Service Information
18
10.1 PWA-006 Control Board 18
10.2 Circuit Diagram
19
11
Assembly and Parts Lists
11.1 Power Source
20
11.2 Wirefeed assembly
22
11.3 Gun and Cable Assembly 23
12
Warranty information
25