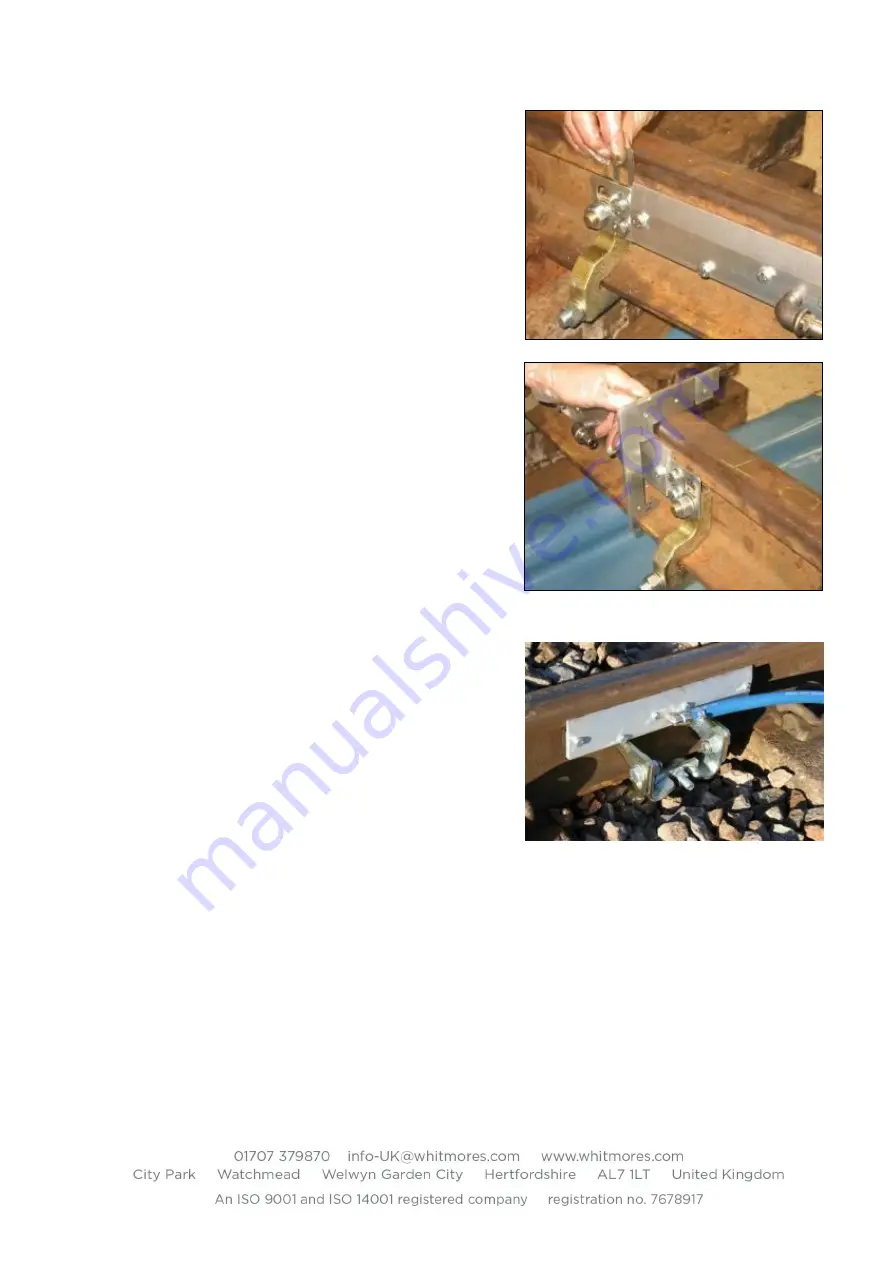
15
plate and over the threads of the M10 bolts
between the bracket and the Blade
backplate.
8.3.3
Repeat for the other end of the Blade if
necessary.
8.3.4
Set the Blade to the required height below
the railhead using a suitable gauge /
measuring device minimum distance is
18mm. The precise dimension is subject to
rail profile and anticipated wheel wear,
which must be carefully considered. If
required a suitable gauge is available from
Whitmore Rail (Part No. or LCS104-06),
showing setting with QHi/Whitmore Rail
gauge).
8.3.5
Repeat from 8.3.1 for the remaining blades.
8.4
Application Variation for Other Rail Types
8.4.1
The fitting process is the same for the Bull
Head and UIC60 style Blades; only the Blade
bracket is different.
8.5
Installing EasiBlades (single central rail clamp)
8.5.1
EasiBlades are supplied as complete single
units. From the 4’ / Gage and midway
between Sleepers / Ties slide the base (W
bracket) over the rail foot as shown. Locate
the hook bolt around the opposite side of the
foot and tighten the single Nyloc nut. Fully
bed the base onto the rail using a hammer on
the vertical faces of the ‘W’ bracket.
Retighten the Nyloc nut.
8.5.2
The blades are provided in left and right hand forms; the difference being the direction the
hose tail points, the correct layout is shown in the adjacent picture, outer pairs with hose
tails pointing towards each other.
8.5.3
Tilt the blade up so that the blade tip is towards the rail head and as high as possible,
lightly tighten the two pivot bolts.