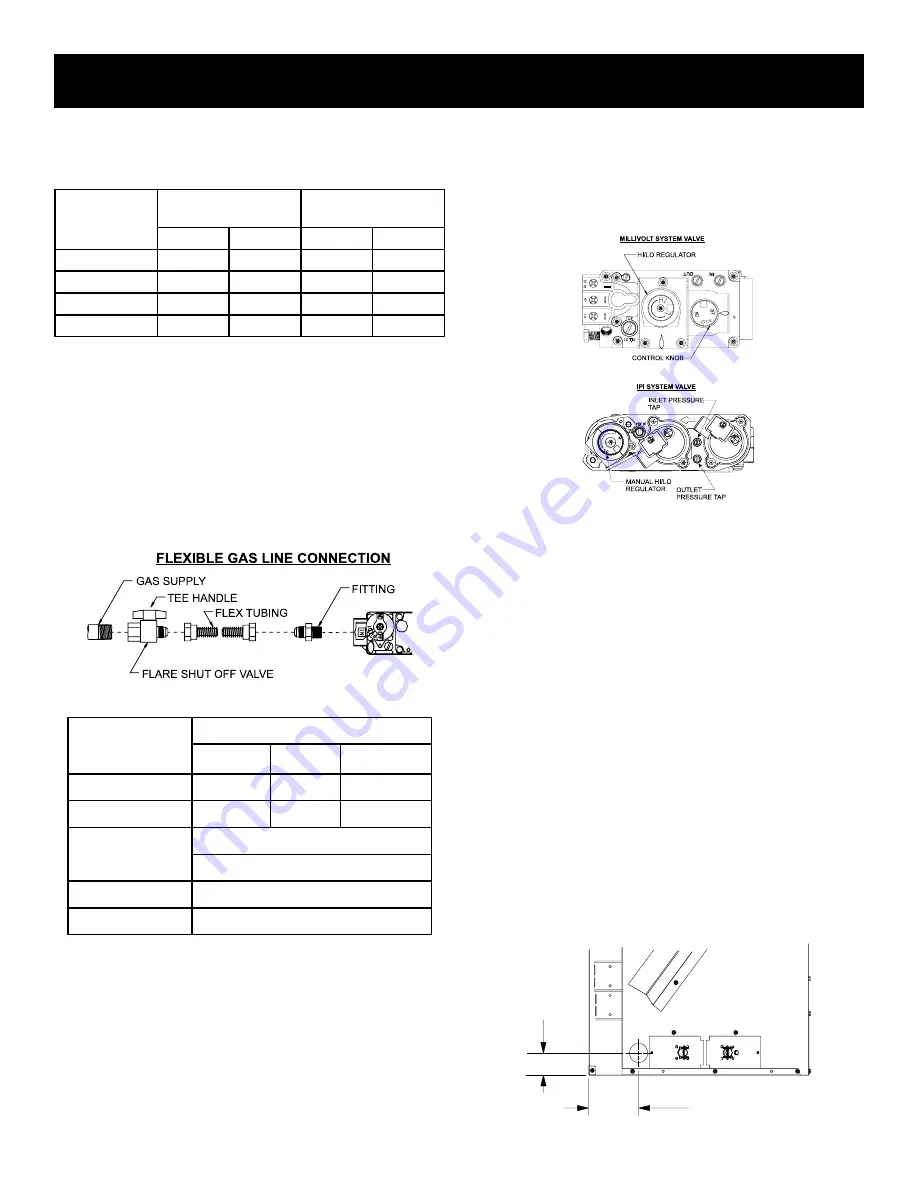
35009-2-1015
Page 13
GAS SUPPLY
The gas pipeline can be brought in through the right or left side of
the appliance. Consult the current National Fuel Gas Code, ANSI
Z223.1 CAN/CGA-B149 (.1 or .2) installation code.
Recommended Gas Pipe Diameter
Pipe Length
Schedule 40 Pipe
Inside Diameter
Tubing, Type L
Outside Diameter
Nat.
L.P.
Nat.
L.P.
0-10 feet
1/2”
3/8”
1/2”
3/8”
10-40 feet
1/2”
1/2”
5/8”
1/2”
40-100 feet
1/2”
1/2”
3/4”
1/2”
100-150 feet
3/4”
1/2”
7/8”
3/4”
Note:
Never use plastic pipe. Check to confirm whether your
local codes allow copper tubing or galvanized.
Note:
Since some municipalities have additional local codes, it is
always best to consult your local authority and installation code.
The use of the following gas connectors is recommended:
— ANS Z21.24 Appliance Connectors of Corrugated Metal Tubing
and Fittings.
— ANS Z21.45 Assembled Flexible Appliance Connectors of Other
Than All-Metal Construction
The above connectors may be used if acceptable by the authority
having jurisdiction. The state of Massachusetts requires that a
flexible appliance connector cannot exceed three feet in length.
Figure 9
Gas Supply Pressure (inches w.c.)
Minimum
Normal
Maximum
Natural Gas
4.5"
7.0"
14.0"
LP (Propane)
11”
11.0"
14.0"
Manifold Pressure (inches w.c.)
Normal (HI)
Natural Gas
3.5"
LP (Propane)
10.0"
Installing a New Main Gas Cock (Check Local Code)
Each appliance should have its own manual gas cock.
A manual main gas cock should be located in the vicinity of the unit.
Where none exists, or where its size or location is not adequate,
contact your local authorized installer for installation or relocation.
Compounds used on threaded joints of gas piping shall be resistant
to the action of liquefied petroleum gases. The gas lines must be
checked for leaks by the installer. This should be done with a soap
solution watching for bubbles on all exposed connections, and if
unexposed, a pressure test should be made.
Never use an exposed flame to check for leaks. Appliance must
be disconnected from piping at inlet of control valve and pipe
capped or plugged for pressure test. Never pressure test with
appliance connected; control valve will sustain damage!
NOTE:
The millivolt gas controls are equipped with a captured screw
type pressure test point, therefore it is not necessary to provide a
1/8 inch test point up stream of the control.
Figure 10
On direct ignition valves, hex plugs may be replaced with hose fittings
for pressure checks, then reinstalled before operating fireplace.
When using copper or flex connector use only approved fittings.
The appliance and its individual shut off valve must be disconnected
from supply piping system during any pressure testing of that system
at test pressures in excess of 1/2 psig (3.5 kPa).
The appliance must be isolated from the gas supply piping system
by closing its individual manual shut off valve during any pressure
testing of the gas supply piping system at test pressures equal to
or less than 1/2 psig (3.5 kPa).
Attention!
If one of the procedures results in pressures in excess
of 1/2 psig (14” w.c.) (3.5 kPa) on the fireplace gas valve, it will
result in a hazardous condition.
Checking Manifold Pressures
Both Propane and Natural gas valves have a built-in pressure
regulator in the gas valve. Natural gas models will have a manifold
pressure of approximately 3.5 inch w.c. (.871 kPa) at the valve
outlet with the inlet pressure to the valve from a minimum of 4.5 inch
w.c. (1.120 kPa) for the purpose of input adjustment to a maximum
of 14.0 inch w.c. (3.484 kPa). Propane gas models will have a
manifold pressure approximately 10.0 inch w.c. (2.49 kPa) at the
valve outlet with the inlet pressure to the valve from a minimum of
10.8 inch w.c. (2.68 kPa) for the purpose of input adjustment to a
maximum of 14.0 inch w.c. (3.484 kPa).
2”
4 1/2”
Figure 11