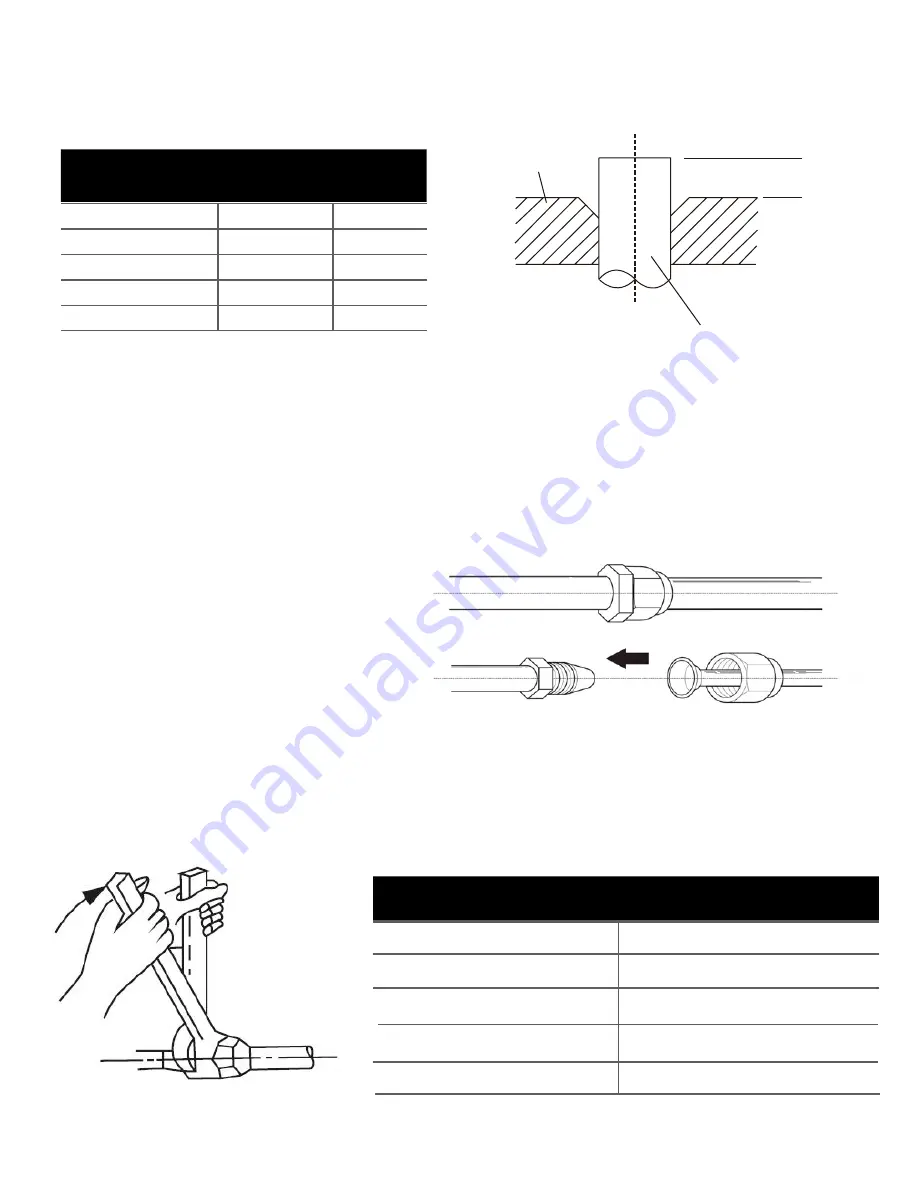
°
F
°
F
°
F
e. Place flaring tool onto form
f. Turn the handle of the flaring tool clockwise until the pipe is fully flared
g. Remove the flaring tool and flare form, then inspect the ends for any cracks and make sure the flaring is even.
4.
Connect pipes
When connecting refrigerant pipes, be careful not to use any excessive torque or to deform the piping in any way. You
should first connect the low-pressure pipe, then the high pressure pipe.
It is recommended to use a CFC and HCFC
compatible thread sealant on all threaded pipe connections.
a.
Align the center of the two pipes that will be connected. To prevent gas leakage, apply refrigeration oil only to
the inner surface of the flare. Use torque wrenches when tightening the flare nuts to prevent damage to the
flare nuts and gas leakage
b.
Tighten the flare nut as tight as possible by hand
c.
Using a spanner, grip the nut on the unit tubing
PIPING EXTENSION BEYOND FLARE FORM
Outer Diameter of
Pipe (
in
)
A (
in.
)
Min.
Max.
Ø
1/4”
0.0275”
0.05”
Ø
3/8”
0.04”
0.063”
0.04”
0.07”
0.078”
0.086”
0.078”
0.094"
Flare form
Pipe
A
CONNECTING THE LINESET
, CONTINUED
Ø
1/2”
Ø
5/8”
Ø
3/4”
TORQUE REQUIREMENTS
Outer Diameter of Pipe (
in.
)
Tightening Torque (
lb
•
ft
)
Ø
1/4”
11lb•ft
18.4lb•ft
25.8lb•ft
33.19lb•ft
47.94lb•ft
d. While firmly gripping the nut on the unit tubing, use a torque wrench to tighten the flare nut according to the
torque values in the Torque Requirements table below. Loosen the flaring nut slightly , then tighten again.
Prior to applying recommended torque to brass flare nut, it is highly recommended a small amount of
refrigeration oil be applied to the flare threads, flare sealing surface, and copper tubing flared surface to
prevent galling of sealing surfaces and aid in providing a refrigerant tight seal (Use refrigeration oil for R134a).
Be careful not to overtighten the connection as this may damage the flare or fitting.
Ø
3/8”
Ø
1/2”
Ø
3/4”
Ø
5/8”
Page 16