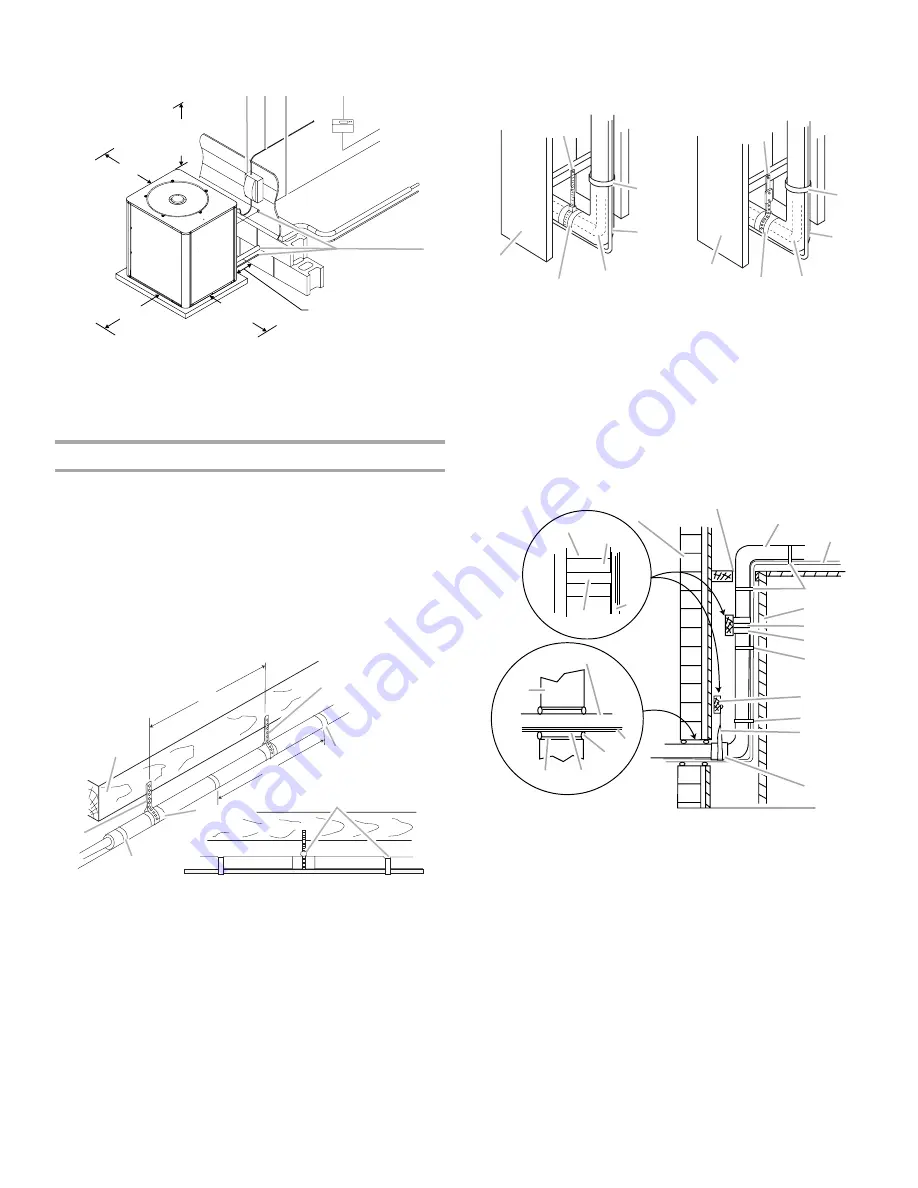
3
Minimum Clearances
Line Set Isolation
The following illustrations demonstrate procedures which ensure
proper refrigerant line set isolation.
Installing Horizontal Runs
This shows how to install line sets on horizontal runs.
NOTES:
■
To hang line set from joist or rafter, use either metal strapping
material or anchored heavy nylon wire ties.
■
Strap the vapor line to the floor joist or roof rafter at 8 ft
(2.4 m) intervals, then strap the liquid line to the vapor line.
Transition from Horizontal to Vertical
This shows how to make a transition from horizontal to vertical.
Installing Vertical Runs (new construction shown)
This shows how to install line sets on vertical runs.
NOTE: Similar installation practices should be used if line set is
to be installed on exterior of outside wall.
IMPORTANT: Refrigerant lines must not contact structure.
A. Weatherproof disconnect switch
B. NEC class 1 wiring
C. NEC class 2 wiring
D. To power supply
E. House thermostat
F. To indoor unit
G. To indoor coil
H. Seal openings
A. Metal strapping material (around
vapor line only)
B. Floor joist or roof rafter
C. Tape or heavy nylon wire tie
D. Metal strapping material (around
vapor line only) and tape or
heavy nylon wire tie (around
vapor and liquid lines)
E. Metal sleeve
48" (121.9 cm)
Overhead Clearance
(Discharge Air)
D
F
G
30" (76.2 cm) Service
Access Clearance
36" (91.4 cm)
Clearance (Inlet Air)
12" (30.5 cm) Clearance
Between Unit and Building
12" (30.5 cm)
Clearance (Inlet Air)
A B
C
E
H
B
A
C
E
C
A
D
8'
8'
A. Style 1—anchored heavy nylon wire tie
B. Tape or heavy nylon wire tie holding liquid
line to vapor line.
C. Liquid line
D. Vapor line—wrapped in armaflex
E. Metal sleeve
F. Wall stud
G. Style 2—automotive
muffler-type hanger
A. Outside wall
B. Space between wall
and refrigerant line
C. Vapor line wrapped
in armaflex
D. Liquid line
E. Anchored heavy nylon wire tie
F. Inside wall
G. Metal strapping material
H. Metal sleeve
I. Wood block between studs
J. Caulk
K. Fiberglass
insulation
L. PVC pipe
A
F
E
D
C
B
G
F
E
D
C
B
Style 1
Style 2
A
B
C
D
E
F
G
H
E
I
E
G
H
C
A
D
J
K
L
C
D
G
H