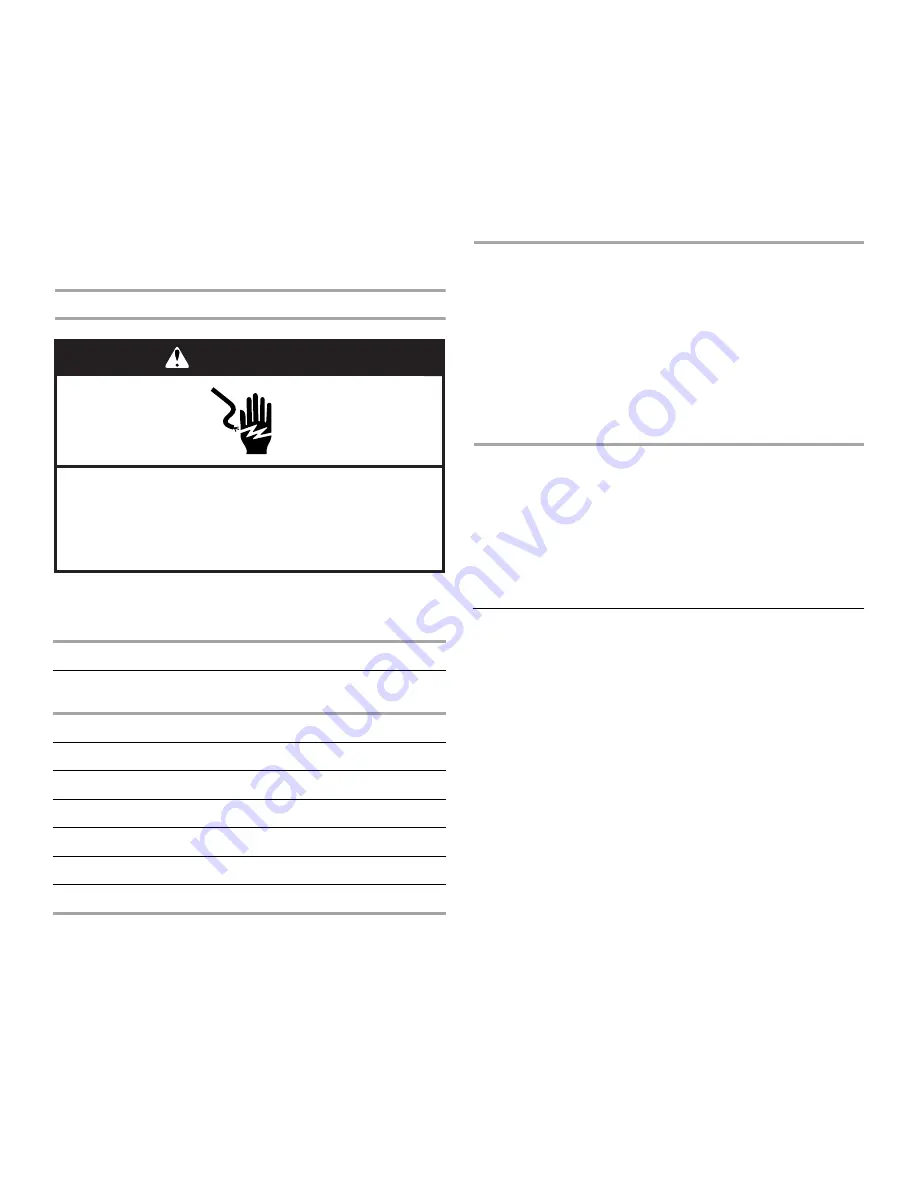
9
3. Adjust the time period between defrost cycles by placing the
defrost time plug in the proper position. See “Defrost Control
Board.”
■
For 30-minute intervals between defrost cycles, move the
Defrost Time Setting Plug to the pins corresponding
to 30.
■
For 60-minute intervals between defrost cycles, move the
Defrost Time Setting Plug to the pins corresponding to
60 (this setting is the factory preset setting).
■
For 90-minute intervals between defrost cycles, move the
Defrost Time Setting Plug to the pins corresponding
to 90.
4. Replace the control box cover.
5. Reconnect power.
Troubleshoot the Defrost System
Diagnostic LEDs
The defrost board uses 2 LEDs for diagnostics. The LEDs flash a
specific sequence according to the condition.
1. Disconnect power.
2. Remove control box cover.
3. Reconnect power and set thermostat for heating operation.
4. Observe LEDs and compare to Defrost Control Board
Diagnostic LEDs chart.
5. If a system failure is indicated, take appropriate action to
correct.
6. Turn off thermostat and disconnect power.
7. Replace control box cover.
8. Reconnect power.
SYSTEM MAINTENANCE
■
Leaves and other large obstructions should be carefully
removed from the heat pump surfaces without damaging the
fin surface of the coil.
■
Routinely clean or change the indoor air filter. Should the
indoor coil become dirty, thus restricting airflow, call a
qualified service person to carefully clean the coil surface.
■
An annual inspection by a qualified person should be
performed to ensure continued quality performance.
ASSISTANCE OR SERVICE
If you need further assistance, you can write to the below
address with any questions or concerns:
Whirlpool
®
Home Cooling and Heating
14610 Breakers Drive
Jacksonville, FL 32258
Please include a daytime phone number in your correspondence.
Accessories
To order accessories contact your Whirlpool
®
Home Cooling and
Heating dealer.
Defrost Control Board Diagnostic LED
Mode
Green
LED (DS2)
Red LED
(DS1)
No power to board
Off
Off
Normal operation/power to board
Simultaneous slow flash
Anti-short cycle lockout
Alternating slow flash
Low pressure switch fault
Off
Slow flash
Low pressure switch lockout
Off
On
High pressure switch fault
Slow flash
Off
High pressure switch lockout
On
Off
WARNING
Electrical Shock Hazard
Disconnect power before servicing.
Replace all parts and panels before operating.
Failure to do so can result in death or electrical shock.
Summary of Contents for W2GH3
Page 10: ...10 Notes ...
Page 11: ...11 ...