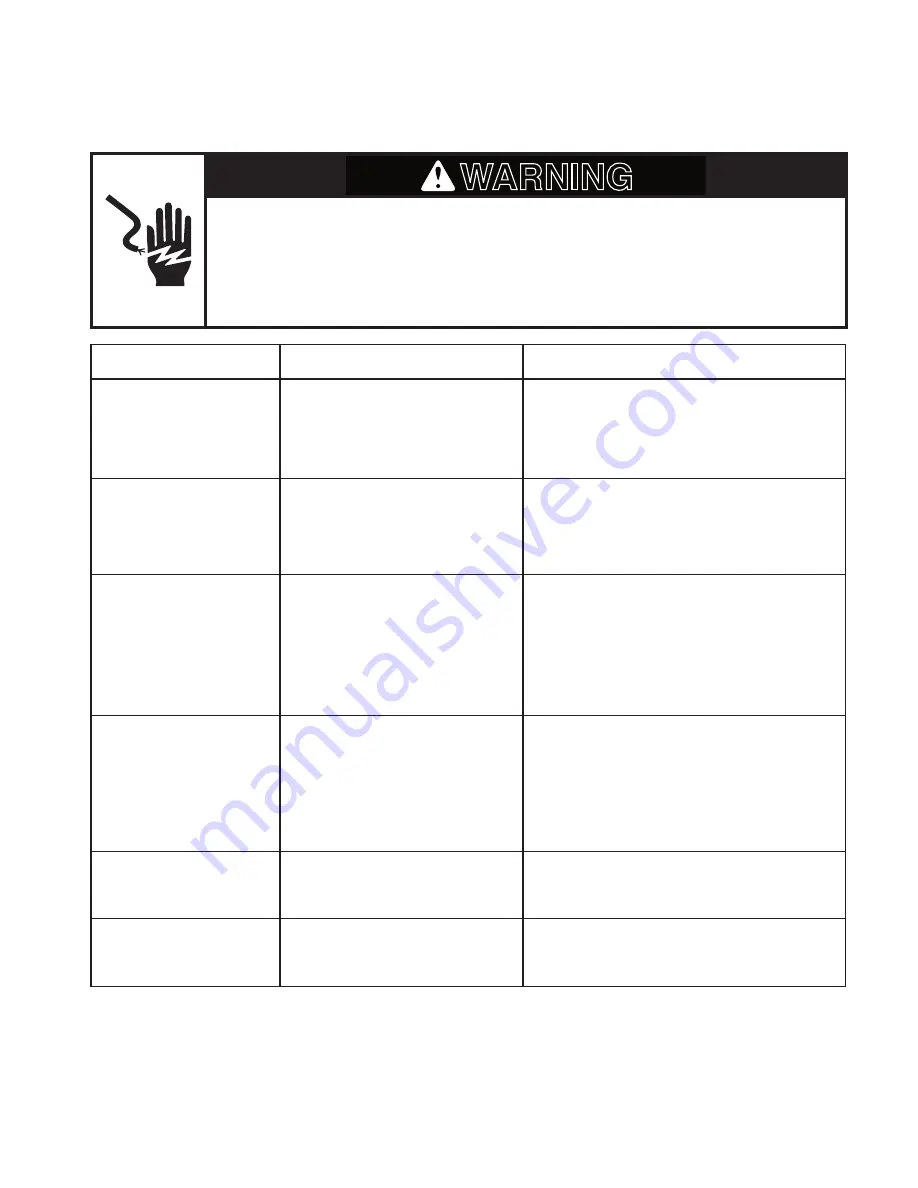
6-5
No water when dispenser
lever is pressed.
Microswitch or water valve failure.
Verify proper wire connections to microswitch
at main board pins 6/3 & 16/9. Verify water
valve connections at main board pins 6/2 and
6/5.
Refer to “Component Testing” section & “Strip
Circuits.”
Replace the control board.
No ice dispensed when
dispenser lever is
pressed .
Microswitch or ice motor failure.
Verify proper wire connections to microswitch
at user interface board pins 3/3 & 5/3. Verify
ice motor connections at user interface board
pins 5/4 and 5/5.
Refer to “Component Testing” section & “Strip
Circuits.”
Replace the user interface.
Refrigerator compartment
light does not switch on
when door is opened.
Burned out lamp.
Loose wiring connections.
Door switch failure.
Verify if the lamp is good.
Verify proper operation of refrigerator com-
partment door switch and connections.
Freezer compartment
light does not switch on
when door is opened.
Burned out lamp.
Loose wiring connections.
Door switch failure.
Verify if the lamp is good.
Verify proper operation of freezer compart-
ment door switch and connections.
TROUBLESHOOTING CHART
The following table shows the various types of appliance faults:
PROBLEM
POSSIBLE CAUSE
TEST PROCEDURE—ACTION
No indicators or functions
on user interface.
No power supply.
Verify circuits RX and TX. Verify proper wire
connections from main board pins 12/11 &
12/12, to user interface pins 3/1 & 3/2.
Refer to wiring diagram.
Replace the user interface.
Indicators for set temper-
atures display correctly,
but dispenser light is dim
when turned on, and ice
will not dispense.
Open neutral circuit to user
interface.
Check for proper wiring and connections of
neutral circuit from control board (pin 12/10)
to user interface (pin 5/1).
Electrical Shock Hazard
Disconnect power before servicing.
Replace all parts and panels before operating.
Failure to do so can result in death or electrical shock.
WARNING
Continued on the next page.
Summary of Contents for JOB AID GC1SHAXM
Page 8: ...1 4 NOTES ...
Page 22: ...3 8 NOTES ...
Page 46: ...6 10 NOTES ...
Page 52: ...7 6 NOTES ...
Page 56: ......