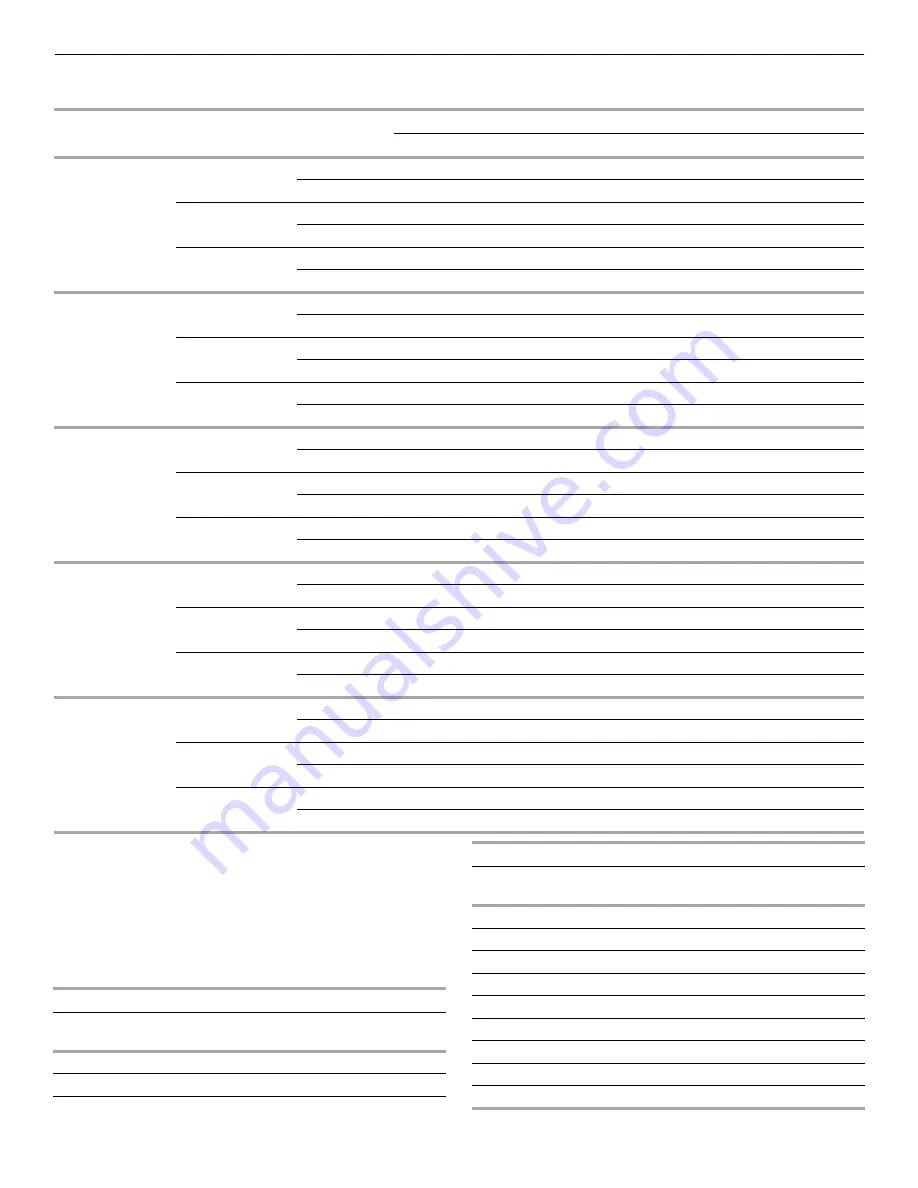
12
Blower Performance Data
NOTES:
■
Data shown is dry coil. Wet coil pressure drop is
approximately 0.2" H
2
0, for 3-row indoor coil; and 0.3" H
2
0,
for 4-row indoor coil.
■
Data shown does not include filter pressure drop,
approximately 0.08" H
2
O.
■
All models should run no less than 350 CFM/Ton.
■
Reduce airflow by 2% for 208-volt operation.
*At 0.1 to 0.5 ESP
E.S.P. (In. of H
2
O)
Model
Speed
Volts—230
0.1
0.2
0.3
0.4
0.5
0.6
0.7
0.8
WPC4524AM
T1 (G)
CFM
882
808
727
649
545
-
-
-
Watts
82
86
92
102
108
-
-
-
T2/T3
CFM
933
873
810
733
637
584
-
-
Watts
93
103
109
120
126
135
-
-
T4/T5
CFM
1,058
1,012
945
896
816
723
672
-
Watts
124
136
142
153
168
172
179
-
WPC4530AM
T1 (G)
CFM
893
824
752
665
575
-
-
-
Watts
87
95
101
111
115
-
-
-
T2/T3
CFM
1,132
1,070
1,011
959
889
827
733
669
Watts
153
162
168
179
184
195
206
208
T4/T5
CFM
1,287
1,236
1,165
1,123
1,066
1,012
958
857
Watts
211
217
228
239
244
255
265
272
WPC4536AM
T1 (G)
CFM
852
764
711
592
545
-
-
-
Watts
80
82
86
95
99
-
-
-
T2/T3
CFM
1,232
1,190
1,131
1,082
1,023
996
889
819
Watts
202
214
221
229
235
246
258
264
T4/T5
CFM
1,267
1,213
1,162
1,120
1,058
1,009
932
841
Watts
218
226
236
245
247
260
272
275
WPC4542AM
T1
CFM
1,123
1,070
1,025
984
942
894
839
774
Watts
162
170
182
193
204
216
229
242
T2/T3
CFM
1,437
1,390
1,354
1,318
1,281
1,243
1,204
1,165
Watts
310
317
331
342
355
366
377
389
T4/T5
CFM
1,528
1,490
1,450
1,410
1,383
1,348
1,312
1,267
Watts
372
379
391
403
416
427
439
451
WPC4548AM
T1
CFM
1,199
1,138
1,085
1,017
957
889
820
755
Watts
162
173
185
193
211
219
232
245
T2/T3
CFM
1,799
1,745
1,698
1,658
1,610
1,560
1,522
1,450
Watts
480
493
508
521
531
545
550
547
T4/T5
CFM
1,921
1,865
1,818
1,780
1,719
1,667
1,579
1,183
Watts
582
585
602
625
627
621
595
569
WGPH4524AM
Cooling/HP
Speed
Adjust
Tap
CFM*
Electric
Heat
Adjust
Tap
CFM*
D
Minus
630
D
Minus
630
D
Normal 700
D
Normal 700
D
Plus
770
D
Plus
770
C
Minus
743
C
Minus
743
C
Normal 825
C
Normal 825
C
Plus
908
C
Plus
908
B
Minus
855
B
Minus
855
B
Normal 950
B
Normal 950
B
Plus
1,045
B
Plus
1,045
A
Minus
945
A
Minus
945
A
Normal 1,050
A
Normal 1,050
A
Plus
1,155
A
Plus
1,155
WGPH4524AM
Cooling/HP
Speed
Adjust
Tap
CFM*
Electric
Heat
Adjust
Tap
CFM*