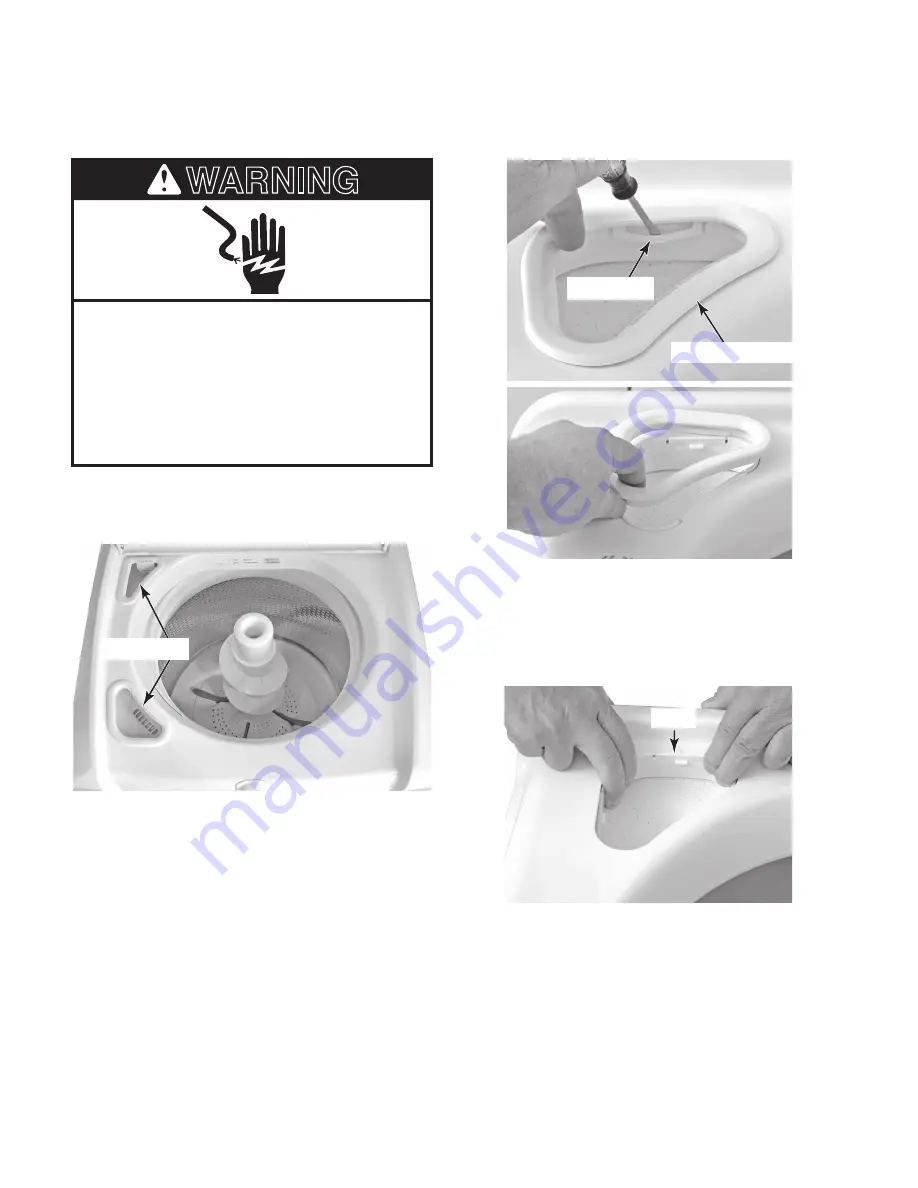
4-6
REMOVING A DISPENSER, THE
FRESH FILL INLET VALVE, AND THE LID LOCK
Electrical Shock Hazard
Disconnect power before servicing.
Replace all parts and panels before
operating.
Failure to do so can result in death or
electrical shock.
1. Unplug washer or disconnect power.
2. Raise the washer lid.
WARNING
NOTE:
The removal procedure for the dis-
pensers is the same so only one will be shown
removed.
3.
To remove a dispenser:
a) Use a small screwdriver and pry out
on the dispenser cover tabs while you
lift the cover off the dispenser (see the
top right photo).
Dispenser Cover
Pry Out Tab
b) Squeeze the bottom of the dispenser,
and release the hooked segments at
the top of the dispenser from the cabi-
net, then push the dispenser out of its
cutout.
Hook
Dispensers
Summary of Contents for Cabrio WTW6200S
Page 4: ... iv NOTES ...
Page 20: ...2 10 NOTES ...
Page 40: ...3 20 NOTES ...
Page 60: ...4 20 NOTES ...
Page 82: ...7 2 NOTES ...
Page 84: ......