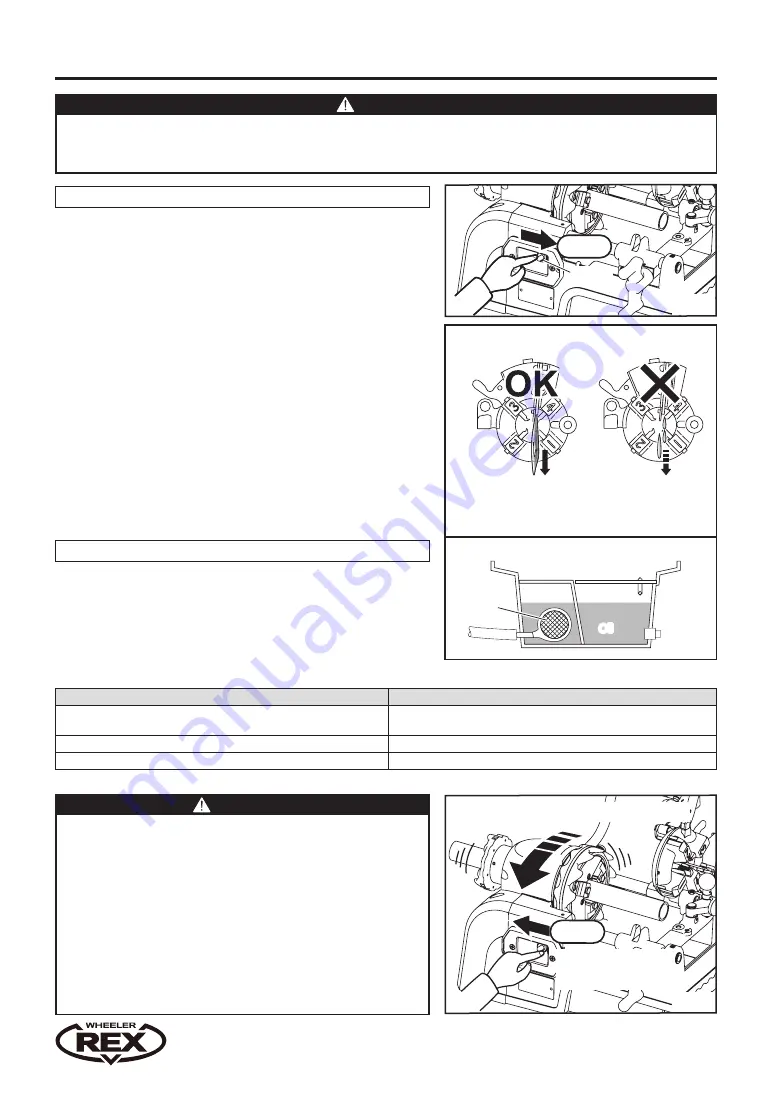
ON
11
OFF
Fig. 21-1
Fig. 22
GETTING READY / OPERATION GUIDE
Problem
Remedy
The carbon brushes are worn out.
Replace with new ones according to the procedures on
Pg. 17, Fig. 40.
When the motor becomes overheated from continuous use
Wait for the motor to cool down and start again.
When an oxide fi lm is generated in the motor
Allow the motor to rotate for about 10 minutes with no load.
Table 3
Fig. 21-2
Motor with built-in braking system
WARNING
Carry out the following checks before starting to cut or thread pipes.
Should any problems arise, refer to "Troubleshooting" at the end of this manual and follow the appropriate instructions.
Continuing to use the machine when a problem has arisen can lead to accident or injury.
9. Checks before starting
(1) Turn on the machine to set the main shaft in motion. (Fig. 20)
- Check there are no abnormal sounds or odours coming from the motor.
- Check the pipe you installed does not vibrate abnormally. If it
does, install it again.
(2) Check that cutting oil fl ows as it should from the die head. (Fig. 21-1)
Confi rm that there is at least 1 liter of cutting oil in the tank. (tank
capacity:1.5 L)
When the volume of oil emitted from the die head is reduced, check
that the amount of cutting oil in the tank is at least suffi cient to cover
and hide the strainer. (Fig. 21-2) Replenish the oil as required.
* If the volume of oil fl owing from the die head remains low even
after the oil has been added, please contact your distributor or
WHEELER-REX.
(3) Allow the machine to rotate without any load for several minutes.
- Check the motor does not become abnormally hot, etc.
(4) Turn the machine off and allow it to stop rotating.
- Check there are no abnormal sounds or odours coming from
the motor. The unit uses a motor equipped with a built-in braking
system for improved safety. Make sure you read and understand
the points below relating to the use and performance of the system.
10. Motor with braking system
(Fig. 22)
The braking system in the motor is designed to minimise idling
after turning the machine off, and to prevent unexpected accidents
and injuries. The motor can stop within fewer rotations than
conventional ones. However, under certain conditions the braking
system may not engage correctly or it may become ineffective.
Read the following cautions carefully to ensure correct use.
Please note that the effectiveness of the brake will be diminished in the following cases.
If the brake does not work even under such circumstances, contact your distributor or WHEELER-REX.
WARNING
1. Make sure the braking system is working before using the machine.
- Although this machine is equipped with both a braking system
and a safety switch, the brake may not work or it may become
ineffective depending on conditions. Check the effectiveness
of the brake before use, and wait till the motor comes to a
complete stop before moving on to the next operation.
2. Be sure to use REX carbon brushes.
- Using other brushes may damage the motor or the machine itself,
or the brake may not be applied.
3. Do not use the machine in rain, humid or damp places, or places
where moisture can easily get into the machine.
- If stored for long periods in a humid place, an oxide fi lm may form
on the motor, and the brake may not be engaged. Store in a place
with low humidity.
brake is effective
as OFF position
Oil
Strainer
Checking the amount of thread cutting oil /Oil tank
Con
fi
rming the amount of thread cutting oil
/ Die head
Appropriate amount of oil
flows smoothly without
interruption
Small volumes of oil
containing air bubbles
produced intermittently
come out
Fig. 20
Switch