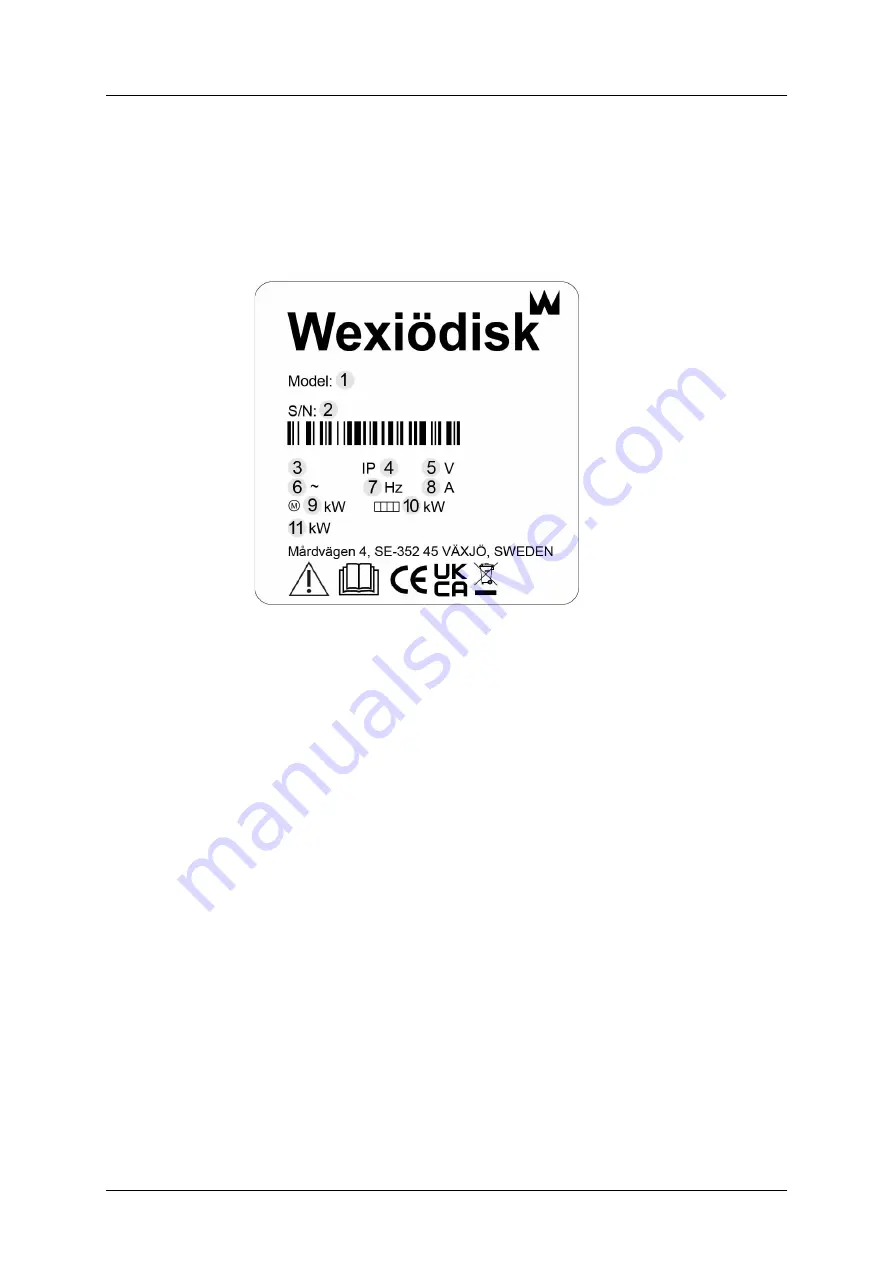
WD-18CW
Rev. (202211)
General instructions
3
1.2
Machine rating
The machine has two rating plates, one of which is placed at the bottom of one
side of the machine and the other in the electrical cabinet. The technical
information on the plates is also included on the machine’s wiring diagram. The
various rating fields show:
1.
Machine type
2.
Machine serial number
3.
Year of manufacture
4.
Enclosure protection class
5.
Voltage
6.
Number of phases with or without neutral
7.
Frequency
8.
Main fuse
9.
Motor output
10.
Electrical heating output
11.
Max. output
1.3
Checking that the machine and manual correspond
Check that the type description on the rating plate corresponds with the type
description on manual cover page. If manuals are missing, it is possible to order
new ones from the manufacturer or the local distributor. When ordering new
manuals, it is important to quote the machine number found on the rating plate.
Summary of Contents for WD-18CW
Page 2: ......