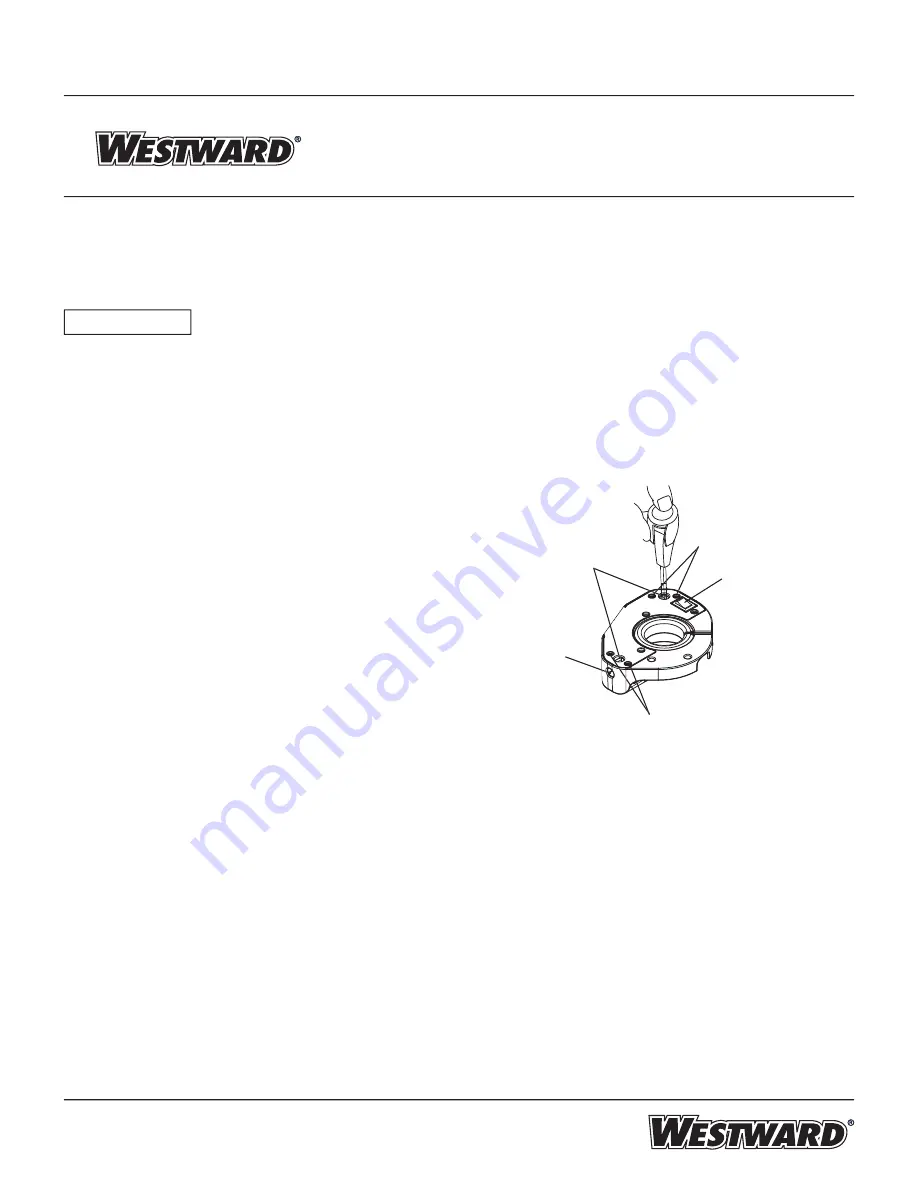
13
Westward Operating Instructions and Parts Manual 1KEN3, 1KEN4
10”,12” Drill Presses
B. Alinging the laser-beam (Figure 22)
To adjust the laser lines:
1. Turn on the laser by pressing the rocker switch.
2. Lower the drill press quill and loosen one turn each the
four screws (4).
3. To adjust the laser beam left/right, turn the adjustment
screw (1) no more than 1/8 turn in either direction. To
adjust the laser beam front to back, turn the adjusting
screw (2) no more than 1/8 turn in either direction.
4. Once adjustments are completed, retighten the four
screws (4).
Figure 22
The laser guide
Your tool is equipped with the Laser guide, a battery powered
device using Class II laser beams. The laser beams will enable
you to preview the drill bit path on the workpiece to be drilled
before you begin your operation.
Avoid direct eye contact
A Laser light is radiated when the laser guide is turned
on. Avoid direct eye contact. Always un-plug the
drill press from the power source before making any
adjustments.
• A laser pointer is not a toy and should not come into
hands of children. Misuse of this appliance can lead
to irreparable eye injuries.
• Any adjustment to increase the laser power is
forbidden.
• When using the laser pointer, do not point the laser
beam towards people and /or refl ecting surfaces.
Even a laser beam of lower intensity may cause eye
damage. Therefore, do not look directly into the laser
beam.
• If the laser pointer is stored for more than three
months without use, please remove the batteries to
avoid damage from possibly leaking batteries.
• The laser pointer includes no servicable components.
Never open the housing for repair or adjustments.
• On units equipped with the laser attachment, repairs
shall only be carried out by an authorized agent.
• Laser Warning label: Max output <1mW DIODE
LASER:630-670nm, Complies with 21CFR 1040.10
and 1040. 11.
Adjusting the laser lines (Figure 22)
A. Check the laser-beam alignment
1. Adjust the table height so it is 5 in. below the bottom of the
chuck.
2. Scribe a round circle (approx. 1/8 in.) on a piece of scrap
wood.
3. Insert a drill bit approx 1/8 in. diameter into the chuck and
tighten.
4. Lower the quill and align the scribed circle with the drill bit
and fasten the wood to the table.
5. Turn on the laser and verify the laser lines (x) are centered
onto the scribed circle.
2
4
4
1
3
WARNING
!