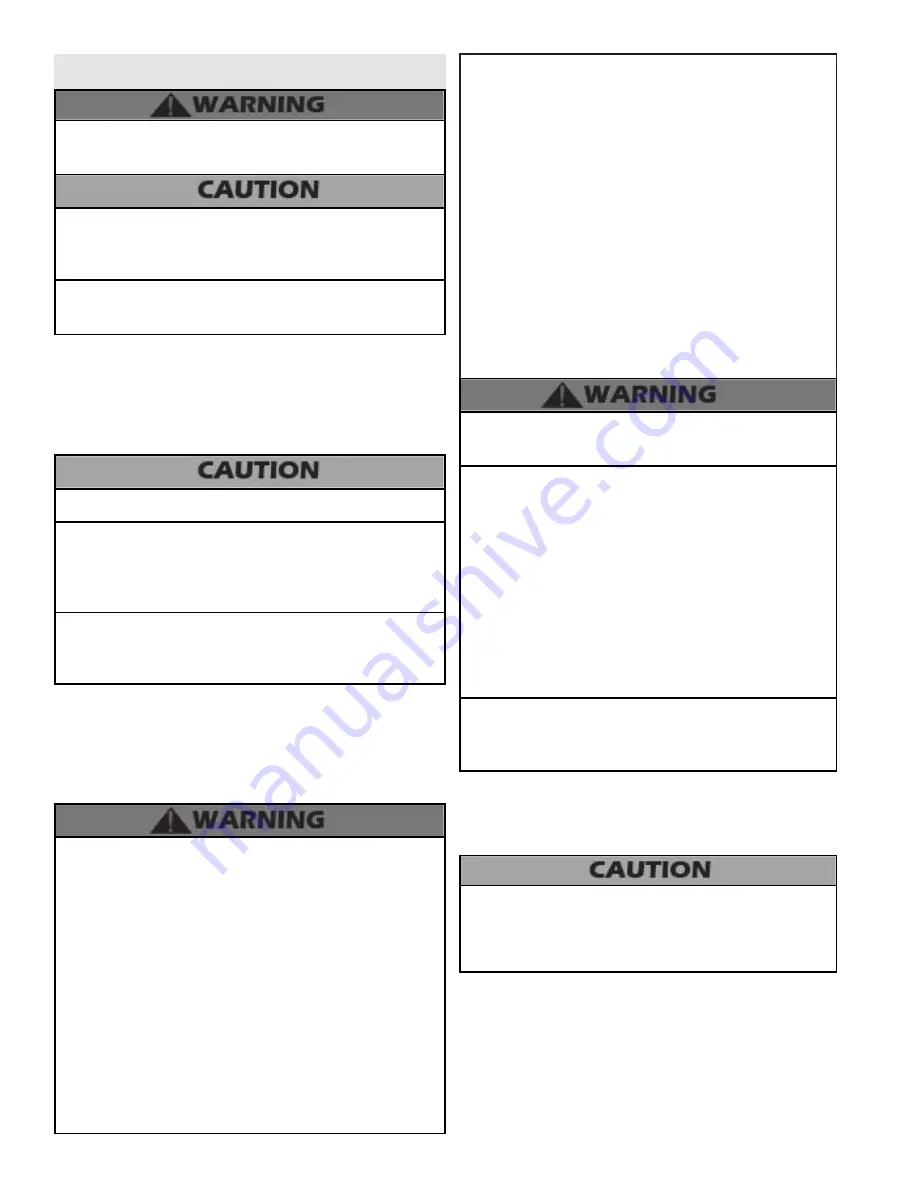
WHL-033 Rev. 1.29.16
14
Part 4 - Piping
Failure to follow the instructions in this section WILL VOID the
warranty and may result in property damage, severe personal
injury, or death.
Dielectric unions or galvanized steel fittings must not be used
in a system with this boiler. Doing so WILL VOID the warranty.
Use only copper, brass, or stainless steel fittings. Teflon thread
sealant must be used on all connections.
DO NOT pipe this boiler with black iron, galvanized steel, steel,
or lead pipe. Doing so will result in premature product failure
and property damage, and WILL VOID the warranty.
A. General Plumbing Information
Use two wrenches when tightening water piping at boiler. Use
one wrench to prevent the boiler return or supply line from
turning. Failure to prevent piping connections from turning
could cause damage to boiler components.
The building piping system must meet or exceed the the piping
requirements in this manual.
NOTE:
The addition of a high temperature limiting device is
important if the boiler is to be connected to a domestic hot
water system.
Plumbing of this product should only be done by a qualified,
licensed plumber in accordance with all local plumbing codes.
The boiler may be connected to an indirect water heater to
supply domestic hot water. Westinghouse offers indirect water
heaters in either stainless steel or glass-lined construction.
The control module uses temperature sensors to provide both
high limit protection and modulating temperature control. The
control module also provides low water protection by sensing
the water level in the heat exchanger. Some codes/jurisdictions
may require additional external controls..
B. Relief Valve
To avoid water damage or scalding due to relief valve operation:
•
Discharge line must be connected to relief valve outlet
and run to a safe place of disposal. Terminate the
discharge line in a manner that will prevent possibility of
severe burns or property damage should the relief valve
discharge.
•
Discharge line must be as short as possible and the same
size as the valve discharge connection throughout its
entire length.
•
Discharge line must pitch downward from the valve
and terminate at least 6” above the floor drain, making
discharge clearly visible.
•
The discharge line shall terminate plain, not threaded,
with a material serviceable for temperatures of 375
o
F or
greater.
•
Do not pipe discharge to any location where freezing
Connect discharge piping to a safe disposal location by following
these guidelines.
RE-INSPECTION OF T&P RELIEF VALVES: T&P valves
should be inspected AT LEAST ONCE EVERY THREE
YEARS, and replaced if necessary,
by a licensed plumbing
contractor or qualified service technician to ensure that the
product has not been affected by corrosive water conditions
and to ensure that the valve and discharge line have not been
altered or tampered with illegally. Certain naturally occuring
conditions may corrode the valve and its components over
time, rendering the valve inoperative. Such conditions can
only be detected if the valve and its components are physically
removed and inspected.
Do not attempt to conduct an
inspection on your own.
Contact your plumbing contractor
for a re-inspection to assure continued safety.
Do not thread a cap or plug into the relief valve or relief
valve line under any circumstances! Explosion and property
damage, serious injury, or death may result.
FAILURE TO RE-INSPECT THE T&P VALVE AS DIRECTED
COULD RESULT IN UNSAFE TEMPERATURE AND/OR
PRESSURE BUILD-UP WHICH CAN RESULT IN PROPERTY
DAMAGE, SERIOUS PERSONAL INJURY, OR DEATH.
could occur.
•
No valve may be installed between the relief valve and
boiler or in the discharge line. Do not plug or place any
obstruction in the discharge line.
•
Test the operation of the relief valve after filling and
pressurizing the system by lifting the lever. Make sure
the valve discharges freely. If the valve fails to operate
correctly, immediately replace with a new properly
rated relief valve.
•
Test T&P valve at least once annually to ensure the
waterway is clear. If valve does not operate, turn the
boiler “off” and call a plumber immediately.
•
Take care whenever operating relief valve to avoid
scalding injury or property damage.
FAILURE TO COMPLY WITH THE ABOVE GUIDELINES
COULD RESULT IN FAILURE OF RELIEF VALVE OPERATION,
RESULTING IN POSSIBILITY OF SUBSTANTIAL PROPERTY
DAMAGE, SEVERE PERSONAL INJURY, OR DEATH.
C. Backflow Preventer
Use a backflow preventer specifically designed for hydronic
boiler installations. This valve should be installed on the cold
water fill supply line per local codes.
All piping methods in this manual use primary / secondary
connections to the boiler loop. This is to avoid the possibility
of inadequate flow through the boiler. For other piping
methods, consult your local Westinghouse representative or
refer to Applications in this manual.
D. Expansion Tank
Expansion Tank and Make-Up Water
1. Ensure that the expansion tank is sized to correctly handle
boiler and system water volume and temperature.
Summary of Contents for WBMC**500
Page 36: ...WHL 033 Rev 1 29 16 36 Figure 27 Internal Connection Diagram ...
Page 59: ...WHL 033 Rev 1 29 16 59 Figure 32 500 Combustion System Replacement Parts Model ...
Page 60: ...WHL 033 Rev 1 29 16 60 Figure 33 850 Combustion System Replacement Parts Model ...
Page 61: ...WHL 033 Rev 1 29 16 61 Figure 34 Water Side Replacement Parts All Models ...
Page 62: ...WHL 033 Rev 1 29 16 62 Figure 35 Cabinet Replacement Parts All Models ...