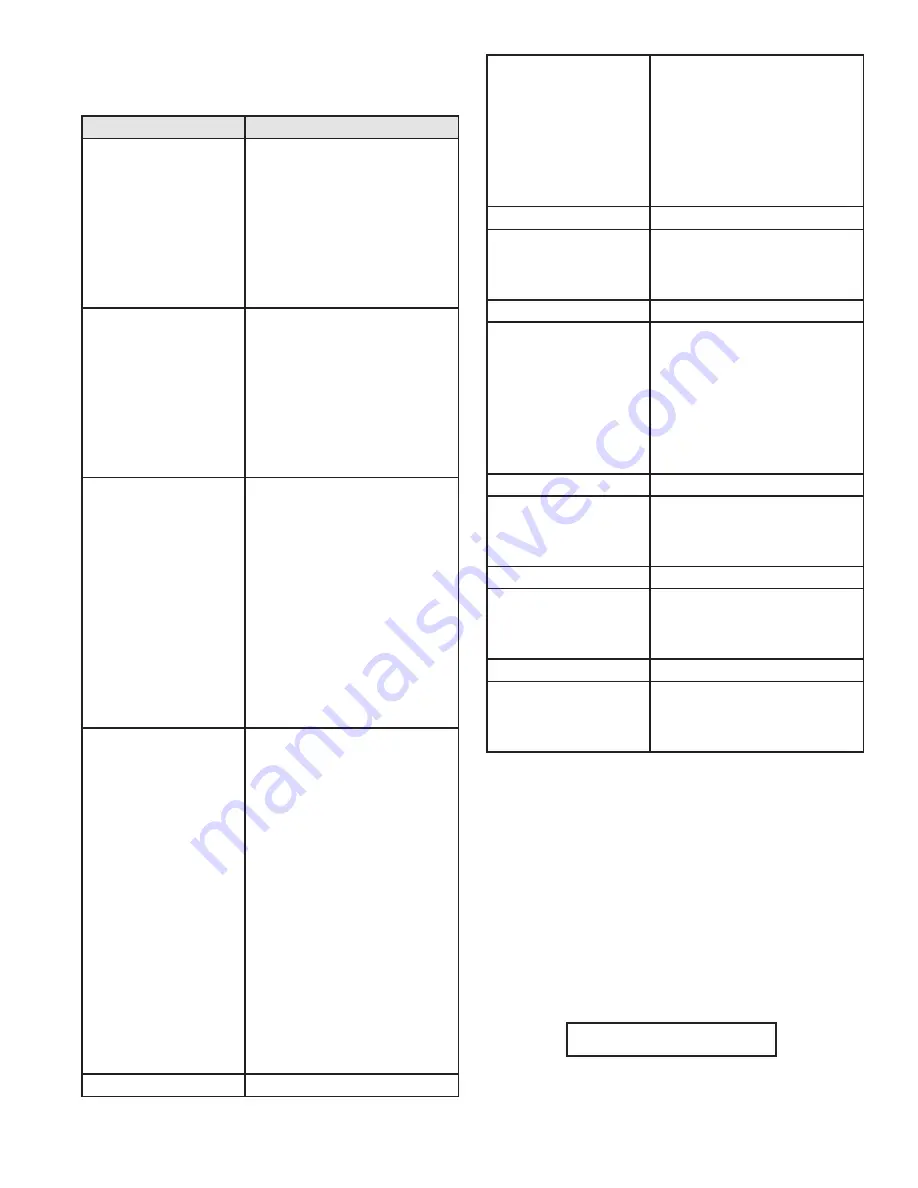
WHL-016 Rev. 4.14.16
55
Screen
Description
CASCADE MASTER READY
SYS PUMP OFF
This screen displays when the boiler
is configured as a Cascade Master
and the system is ready to accept
a demand for heat. The second line
indicates the cascade system pump
output status. This screen alternates
with the default screen every 5
seconds or can be accessed by
pressing the
<
key from the default
screen.
CASCADE NO FOLLOWER
SYS PUMP OFF
This screen displays when the boiler
is configured as a Master Boiler and
there are no connected follower
boilers, or the follower boilers are not
powered. The second line indicates
cascade system pump output status.
This screen alternates with the
default screen every 5 seconds or
can be accessed by pressing the
<
key from the default screen.
CASCADE NO SENSOR
SYS PUMP OFF
This screen displays when the boiler
is configured as a Master Boiler and
there is no system temperature
sensor connected or the system
sensor is defective. The cascade
system will still function in this
situation with reduced efficiency.
All boilers will run simultaneously
rather than in a staged fashion.
The second line indicates cascade
system pump output status. This
screen will alternate with the default
screen every 5 seconds or can be
accessed by pressing the
<
key from
the default screen.
CASCADE TT 0123 567
SYS PUMP ON 12:47P
This screen displays information
about cascade status. The TT in
the center of the top line shows
that cascade demand is coming
from the TT contact being closed.
You may also see DHW if the
demand is from a DHW sensor, or
0-10 if the demand is from a 0-10
volt input. The following numbers
show which boiler addresses are
currently communicating to the
master. If a boiler address is not
used or communicating, the number
will not display. In the example to
the left, boiler address #4 is not
communicating. When a boiler in the
system is firing, its address number
will alternate with a ‘.’ to signify it
is firing. The bottom line shows the
status of the system pump output
contacts.
Press v once.
CASCADE PWR 100%
PRESENT 01234567
This screen displays overall cascade
power output. The range of this
value is the number of boilers
communicating with the Master x
100. For example, if 8 boilers are
connected and firing, the maximum
cascade power is 800%. The second
line shows which boiler addresses
are communicating with the Master.
Press v once.
CASCADE SYST 118
o
F
CASCADE SET 190
o
F
This screen displays current system
temperature sensor reading on the
top line and the cascade system
temperature setting on the bottom.
Press v once.
BOILER 0 100%
BOILER 1 56%
This screen displays the current
cascade power demand output
on a per connected boiler basis
for boilers addressed as 0 and 1.
In the example, boiler 0 is being
commanded to fire at 100% and
boiler 1 at 56%. If this were a 2 boiler
system, the ‘CASCADE PWR’ screen
above would read 156%.
Press v once.
BOILER 2 0%
BOILER 3 0%
This screen displays the current
cascade power demand output on a
per connected boiler basis for boilers
addressed as 2 and 3.
Press v once.
BOILER 4 0%
BOILER 5 0%
This screen displays the current
cascade power demand output on a
per connected boiler basis for boilers
addressed as 4 and 5.
Press v once.
BOILER 6 0%
BOILER 7 0%
This screen displays the current
cascade power demand output on a
per connected boiler basis for boilers
addressed as 6 and 7.
Table 23 - Cascade Menu
B. Cascade Menu
This menu is accessed by pressing
<
at the default menu or
>
at
the status menu.
C. Boiler Test Mode
This function is intended to simplify gas adjustment. The
following tables include recommended combustion settings
by fuel type and boiler fan speeds. Automatic modulation does
not take place while the controller is in Test Mode. However,
the boilers will modulate down if the program set point is
reached while running in Test Mode. It is recommended to enter
Test Mode with the largest load possible to create such a heat
demand that Test Mode will not be interrupted. To enter Test
Mode press
^
and
ENTER
simultaneously.
NOTE:
The boiler will automatically exit Test Mode after 20
minutes of operation.
To leave Test Mode press
^
and
v
simultaneously.
SERVICE RUN 3400 RPM
PUMP ON 4:49P
Summary of Contents for WBC 399
Page 14: ...WHL 016 Rev 4 14 16 14 Figure 6 Boiler Dimensions NOTE All Dimensions Are Approximate 055 080 ...
Page 21: ...WHL 016 Rev 4 14 16 21 Figure 9 Piping Symbol Legend ...
Page 42: ...WHL 016 Rev 4 14 16 42 Figure 33 Internal Connection Diagram ...
Page 65: ...WHL 016 Rev 4 14 16 65 Figure 37 Combustion System Replacement Parts 55 110kBTU Models ...
Page 67: ...WHL 016 Rev 4 14 16 67 Figure 39 Combustion System Replacement Parts 155 399kBTU Models ...