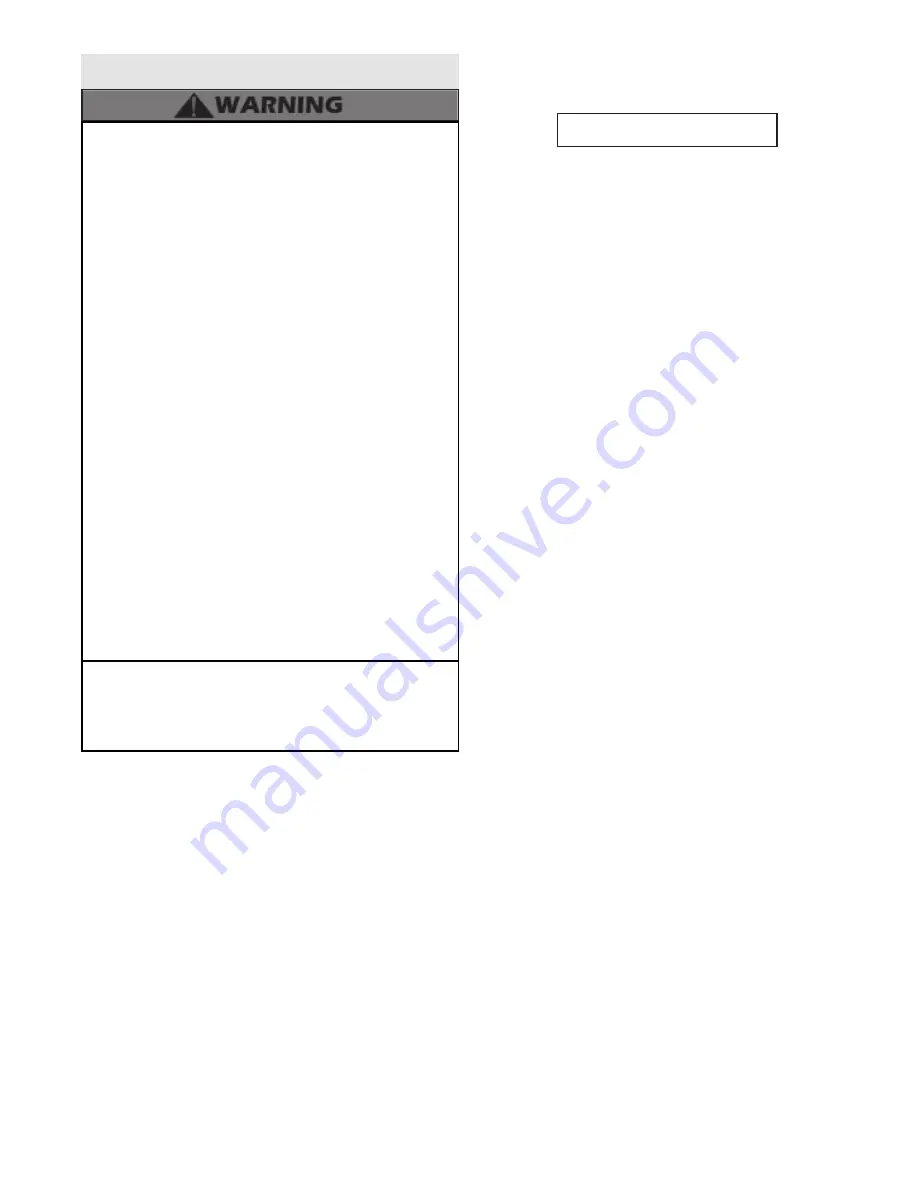
WHL-016 Rev. 4.14.16
49
Part 9 - Start-Up Procedure
FOR YOUR OWN SAFETY READ BEFORE OPERATING
1. This boiler does not have a pilot. It is equipped with an
ignition device which automatically lights the burner. Do not
try to light the burner by hand.
2. BEFORE OPERATING: Smell all around the boiler area for
gas. Be sure to smell next to the floor because some gas is
heavier than air and will settle on the floor.
3. WHAT TO DO IF YOU SMELL GAS
•
Do not try to light any boiler.
•
Do not touch any electric switch, do not use any phone
in your building.
•
Immediately call your gas supplier from a neighbor’s
phone. Follow the gas suppliers’ instructions.
•
If you cannot reach your gas supplier, call the fire
department.
•
Turn off the gas shutoff valve (located outside the
boiler) so that the handle is crosswise to the gas pipe.
If the handle will not turn by hand, don’t try to force
or repair it, call a qualified service technician. Force or
attempted repair may result in a fire or explosion.
4. Do not use this boiler if any part has been under water.
Immediately call a qualified service technician to inspect the
boiler and to replace any part of the control system and any
gas control that has been damaged.
5. The boiler shall be installed so the gas ignition system
components are protected from water (dripping, spraying,
rain, etc.) during boiler operation and service (circulator
replacement, condensate trap, control replacement, etc.)
Failure to follow these instructions could result in property
damage, serious personal injury, or death.
A. Control Overview
The control is one of the primary safety devices of the boiler.
It monitors the safety sensors of the boiler to assure safe and
efficient operation.
The control has many features associated with system design.
This section addresses programming features, including
Boiler Settings / System Settings / Maintenance Settings and
System Diagnostics, to help in customizing your control. It
is important to fully understand control capabilities before
customization, as its factory defaults may already fit your
system design and not require any adjustment at all.
C. Operating Instructions
Before operating the unit, it is important to remove the cover
and verify that the gas line and water lines are connected to
boiler and fully purged. If you smell gas, STOP; Follow the safety
instructions listed in the first part of this section. If you do not
smell gas, follow the next steps.
1. Turn down the thermostats before applying power to the
boiler. If 0–10 volt or other inputs are used, make sure that they
are set so there is no call for heat while programming.
2. Turn on the power to the boiler or boilers if a cascade system
used.
3. Next, check the boiler settings. Adjustment and factory
defaults are outlined within this section. If a cascade system is
used, it is important that all the boilers have the same boiler
settings.
4. Next, check the system settings. Adjustments and factory
defaults are outlined within this section. If a cascade system is
used, it is important that the Master Boiler is programmed with
the correct system settings.
5. Create a demand on the boiler or boilers if a cascade system
is used. The user can monitor system functions when the boilers
are operational.
6. If the boilers fail to start, refer to the troubleshooting section
in the back of this manual.
If you discover any evidence of a gas leak, shut down the
boiler at once. Find the leak source with a bubble test and
repair immediately. Do not start the boiler again until the
leak is repaired. Failure to comply could result in substantial
property damage, severe personal injury, or death.
B. Navigation of the Display
The display includes a two line backlit LCD readout to provide
informative messages about the operation of the boiler. Many
operating parameters can be viewed and adjusted by using
the six buttons on the display. The function of each button is
described below.
RESET
– The RESET button has two functions.
– Resets any lockout error code
– Returns the user to the default display screen.
ENTER MENU CODE
000
ENTER
– The ENTER key is used to access parameter
programming mode. To access this mode, hold down the ENTER
key for more than 4 seconds. The readout will change to:
One of the zeroes will be blinking. Use the
^ v
arrow keys to
change the blinking digit to the correct value. Use the
< >
arrow
keys to select the next digit to change and again use the
^ v
keys
to change the value. Repeat until the correct code is entered.
Press the
ENTER
key to accept the code entered. If the code is
correct, the readout will change to the appropriate screen. If the
programming code is not accepted, the readout will continue to
display as shown above.
ENTER
is also used to enable a function for editing. After the user
navigates to the desired function, the user holds down
ENTER
for one second. When
ENTER
is released, the function value
will begin to blink. The function can now be changed using the
^ v
keys. After the new value is displayed, the user then presses
ENTER
for 1 second to lock the new value of the function. The
value will then stop blinking.
LEFT AND RIGHT ARROW KEYS
–
< >
are used to navigate
between the default display, status display, analog and
cascade displays if they are enabled. The
< >
keys are also used
in programming modes to change between programmable
functions. It is recommended you use the Menu Maps in the
back of this manual and the detailed menu instructions printed
in this section to help in menu navigation.
UP AND DOWN ARROW KEYS
–
^ v
are used to navigate
between the various functions displayed in the menu. After the
function is enabled for editing by pushing the
ENTER
key, the
^
v
keys are used to adjust the function upward or downward to
the desired value.
Summary of Contents for WBC 399
Page 14: ...WHL 016 Rev 4 14 16 14 Figure 6 Boiler Dimensions NOTE All Dimensions Are Approximate 055 080 ...
Page 21: ...WHL 016 Rev 4 14 16 21 Figure 9 Piping Symbol Legend ...
Page 42: ...WHL 016 Rev 4 14 16 42 Figure 33 Internal Connection Diagram ...
Page 65: ...WHL 016 Rev 4 14 16 65 Figure 37 Combustion System Replacement Parts 55 110kBTU Models ...
Page 67: ...WHL 016 Rev 4 14 16 67 Figure 39 Combustion System Replacement Parts 155 399kBTU Models ...