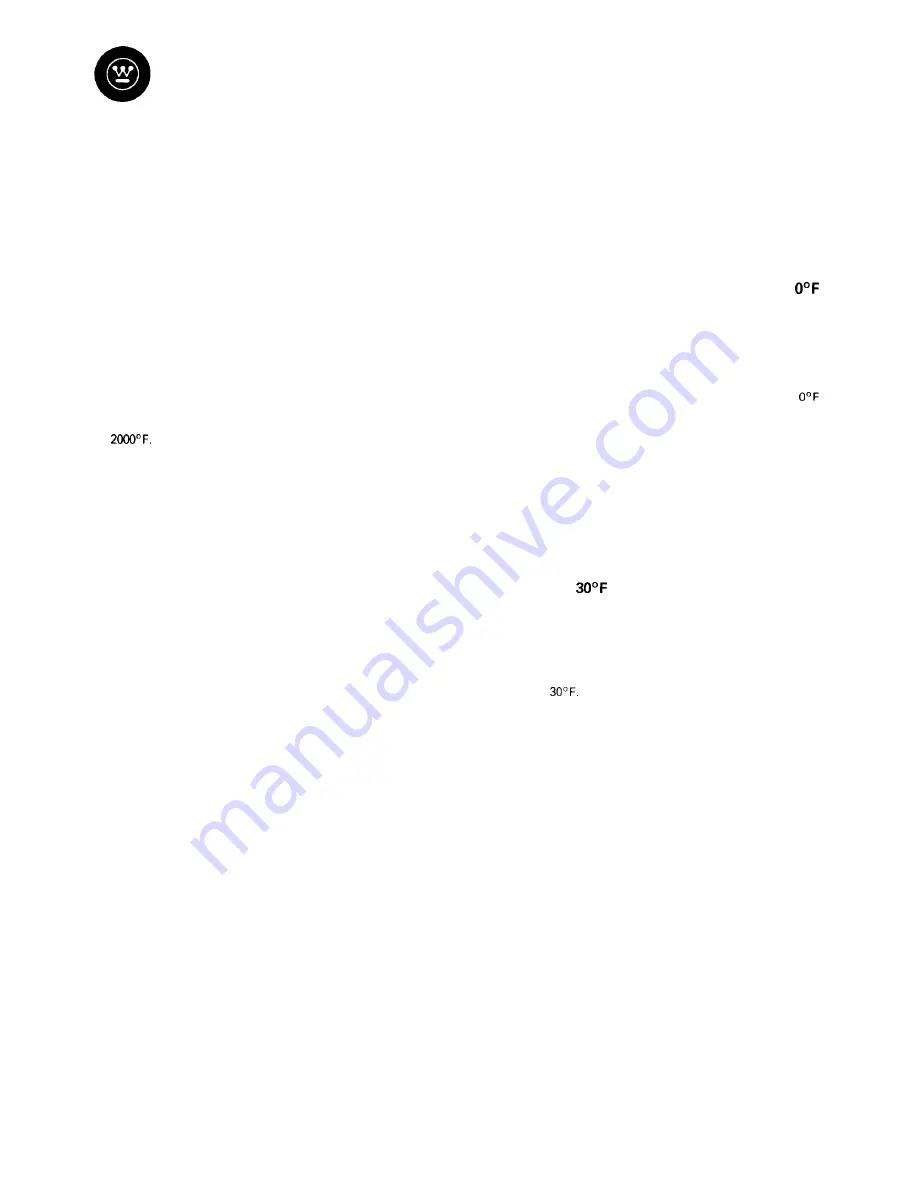
Installation Bulletin
PDG4
Page 3
with a hand gun. The suggested greasing
interval is indicated on a sticker attached to
the unit.
3. Motor Bearings Each motor is equipped
with ball bearings. Ball bearings consume a
very small amount of lubricant, but enough
must be present at all times to prevent
motor injury. The length of time a bearing
can run without having grease added or
replaced will depend upon the operating
conditions. Under normal operating condi-
tions the motor bearings should be
lubricated at 2000 hour operating intervals,
The lubricant should be from a clean closed
container and should be anti-friction type
bearing grease free from solid fillers or
other harmful ingredients. Lubricant should
have a safe operating temperature of
The air inlet of the condenser coil should be
kept clean through a regular preventative
maintenance program.
Compressor
The oil level of the compressor(s) should be
checked periodically, with the unit shut off. If
oil is needed, allow unit to pumpdown and
then place system “OFF-ON” switch (S1) in
the off position. Close the suction and
discharge valves at the compressor. Partially
screw the pipe plug out of the filler hole (the
filler hole is located just above and left of the
crankcase sight glass on most compressors)
and allow pressure to bleed from crankcase
completely before removing plug.
Add oil through the filler hole, using only
Suniso G3 Refrigerant oil that has not been ex-
posed to air or other contaminates. (Do not
overfill).
Replace and tighten filler hold pipe plug.
Reopen compressor suction and discharge
valves. (CAUTION: Do not run compressor
when discharge valve is closed).
On systems equipped with the AC&R method
of oil equalization, the oil may be added
through the 1/4 SAE flare gage port of the up-
per valve on the oil reservoir when the stem is
in the front seated position. (The valve stem
must be backseated when the unit is
operating).
The oil level should be between the two sight
ports. Check oil level after 2 hours of operation
and again after 2 days of operation.
Winter Control Data
Due to the wide range of applications, it is
sometimes necessary to operate the Chillers at
ambients below summer conditions. Without
proper control, when ambients drop below 60F
the pressure differential between the condenser
and the evaporator is below the level to insure
proper thermal expansion valve operation. As a
result, the unit may cycle on low pressure con
trol with the possibility of evaporator freezing.
Westinghouse offers two types of system con-
trol allowing the units to operate at the winter
ambients indicated:
Fan Cycling
Medium Ambient Control To
(STANDARD EQUIPMENT - FACTORY
INSTALLED)
A fan cycling control is standard on all
Westinghouse Air Cooled Packaged Water
Chillers to provide proper operating head
pressures, in ambient conditions
to
This is an automatic operation and is ac-
complished by cycling one fan on two fan
units; two fans, in sequence, on three fan
units; and three fans, in sequence, on four fan
units. The last fan on each unit is connected
directly to the load side of the fan contactor,
which in turn is controlled by the operation of
the fan cycling pressure control(s) and the
compressor contactor auxiliary contact. This
arrangement provides positive start-up control
down to + 30F by delaying the condenser fan
operation until a predetermined head pressure
is obtained.
Fan Cycling And Heated
Receiver(s)
Low Ambient Control
( O P T I O N A L E Q U I P M E N T F A C T O R Y I N -
STALLED)
A heated receiver lone for each refrigerant cir-
cuit) to be used in conjunction with the fan
cycling control to assure compressor start in
ambient temperatures down to
is offered
as an optional priced feature.
This, also, is an automatic operation and is ac-
complished by a pressure cycling control (set
to cut in at 180 PSI and set to cut out at 210
PSI), sensing the receiver pressure and con-
trolling a heater. A check valve, factory install-
ed, in the refrigerant circuit between the
receiver and the condenser prevents refrigerant
migration from receiver to condenser during
the off cycle. When the receiver pressure drops
below 180 PSI, as would be encounted on the
off cycle at low ambient conditions, the
pressure switch would close and the receiver
heater would be energized. With the refrigrant
flow blocked from receiver to condenser by the
check valve and prevented from flowing from
receiver to evaporator by the liquid line
solenoid valve receiver pressure would rise and
be maintained sufficiently to allow expansion
valve operation when the unit starts. If at any
time, the receiver pressure would rise to 210
PSI the pressure control would open and the
receiver heater would be de-energized. A back-
up safety thermostat is provided to shut off the
heater in the event the receiver temperature
reaches 130F
Once the unit has started, head pressure would
be maintained by the fan cycling controls as
explained under heading “Fan Cycling Medium
Ambient Control” above.