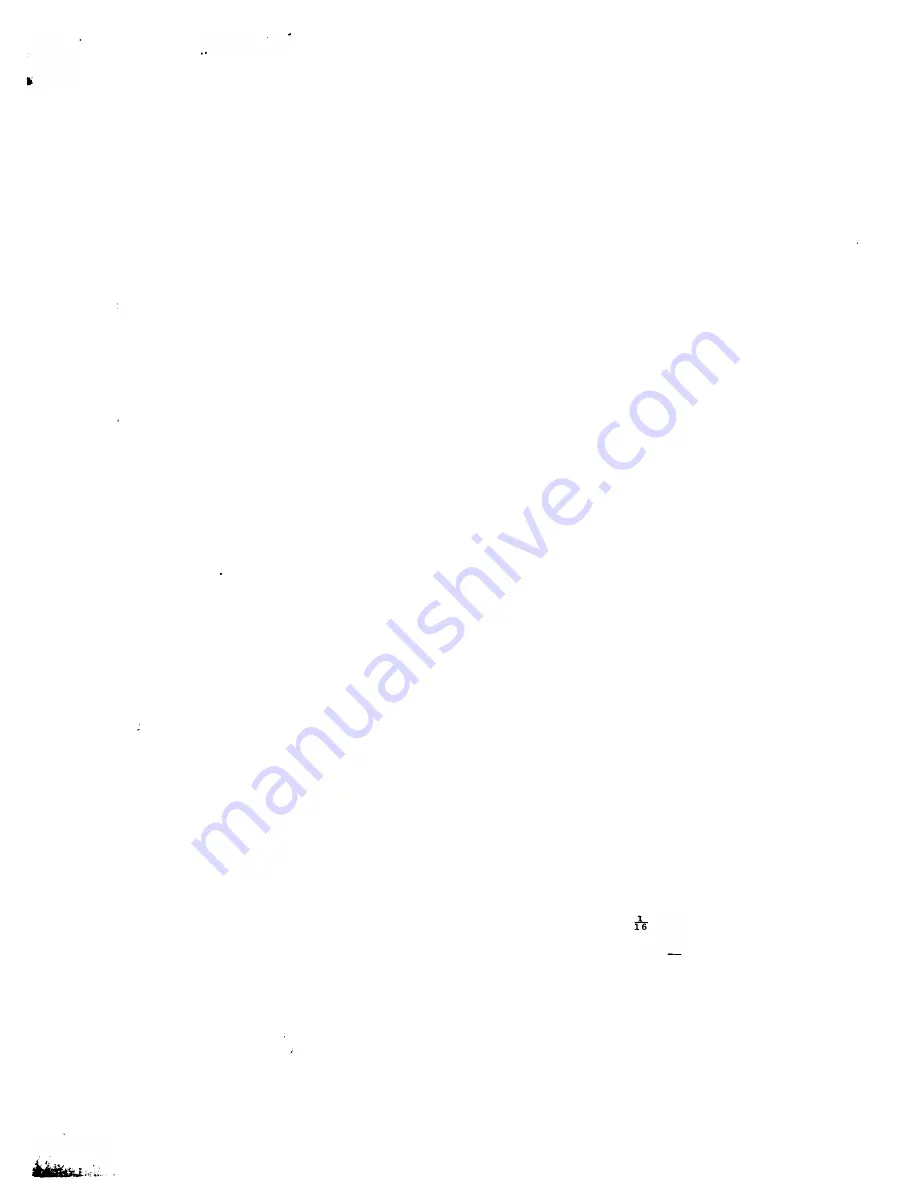
Type
50-DH-50
Air Circuit Breaker
Maintenance
The frequency of inspection, cleaning, etc. will
depend upon the activity and duty to which the
breaker is subjected and upon the cleanliness of
the atmosphere and surroundings of the breaker.
For normal applications of the breakers described
herein it is recommended that a preliminary or
visual inspection be made every three months. A
complete inspection, including removal of the
stacks for cleaning, should be made every twelve
months.
�hen breaker operating duty is high or where
atmospheric conditions are dirty the inspections
should be made more frequently. The following
table is recommended as a guide for intervals be
tween inspections until such time as accumulated
experience from any particular application shall
indicate that the periods may be lengthened, or
shquld perhaps be shortened.
Inspection
Frequency of Operating
Detail
Duty
Clean Ex-
ternal sur-
faces
Blow out
Arcing
Chambers
Remove
and Clean
Arcing
Chamber
Inspect
Contacts
Inspect
Mechanical
Normal
5 Oper.
per day
3 Mos.
6 Mos.
12 Mos.
6 Mos.
Moderate Repetitive
15 Oper. 30 Oper.
per day
per day
3 Mos.
2 Mos.
3 Mos.
2 Mos.
6 Mos.
4 Mos.
6 Mos.
4 Mos.
Parts
12 Mos. 6 Mos.
4 Mos.
The frequency of repetitive operations should be
limited to a maximum of
20
in
10
minutes. The
maximum number of repetitive operations between
maintenance periods should be
2500
whether the
breaker is making inrush currents as encountered
in motor starting service and interrupting up to a
maximum of the breaker nameplate continuous
current rating or operating on other repetitive
operations which may be combined with fault
duty. However, inspection and possible mainte
nance will be required after each fault operation.
Caution
Parts of the circuit breaker that are in the high
voltage compartment of the unit are at line poten
tial; consequently the breaker should be isolated
from the line by disconnecting switches or contacts
before attempting any work on the breaker. For
additional safety measures see "SAFETY FOR
PERSONNEL".
General
Inspect the' breaker structure in general and
see that all bolts, nuts, etc., are tight and that all
cotter pins, locking clips, etc. are in place. Note
evidences of excessive wear or other improper oper
ation of the various parts.
Clean off any accumulation of dust and dirt
from the external surfaces. Dry compressed air is
best suited for this purpose. Waste the air for a
few seconds so that any residue of moisture that
has accumulated in the air line will not be sprayed
over insulating surfaces. Direct the air stream
thoroughly into all joints and crevices. If com
pressed air is not available, this cleaning may be
done with a clean dry cloth. Steam waste is not
recommended for this purpose because of its tend
ency to leave a residue of lint on insulating
surfaces.
8
Magnetic Circuit
The magnetic circuit assembly consists of the
blow-in coils, the magnetic poles and yoke. This
assembly is attached to and insulated from the
back plate by a micarta block which is tapped to
receive hexagon head bolts. Any tightening of
these bolts should be done with a wrench having a
lever arm of six-inches or less to avoid the possi
bility of stripping the threads in the micarta blocks.
Arcing Chambers
It should be borne in mind that the insulating
parts of the arcing chamber remain in position
across the contacts at all times. While the contacts
are in the open position these. insulating parts are
subjected to the full potential across the breaker.
Ability to withstand this potential will depend upon
the care given to the insulation in the arcing
chamber.
On general inspections the arcing chambers
should be blown out with compressed air by direct
ing the air stream upward from the contact area
and out through the stack. Play the dry air stream
thoroughly over the arc box sides (box like com
partment in which the arc is drawn) and through
each space between adjoining plates of the stack.
The arcing chamber should be removed periodi
cally and thoroughly inspected. Any residue of dirt
or arc combustion should be removed by a vigorous
brushing. A stiff wire brush is not recommended
for this purpose due to the possibility of scratching
or roughening the insulating surfaces and inviting
increased deposits of dirt in future service. Inspect
the stack plates for metallic deposits, breakage or
evidence of undue deterioration. The arc chambers
derive considerable of the interrupting ability from
the narrow upper end of the V-slots. That portion
of the slot is nominally
inch wide. When inter
rupting duty has caused the upper extremity of the
slot to increase in width to
136
inches the ceramic
plates should be replaced.
After the arcing chamber has been replaced in
position inspect to see that the contact tongue of
the stack has engaged the jaw connecting to the
blow-in coil and that the front arcing horn is
securely connected to the lower terminal by means
of the shunt straps. Also check the operation of
the moving contact blades to insure that the arc
chamber sides do not interfere with their travel.
,
•
•
•
www
. ElectricalPartManuals
. com